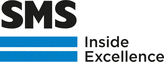

Catalog excerpts
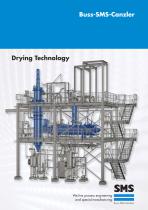
Drying Technology
Open the catalog to page 1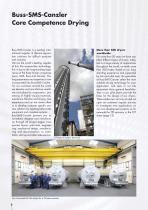
Buss-SMS-Canzler Core Competence Drying Buss-SMS-Canzler is a leading international supplier of thermal separation solutions for difficult products and mixtures. We are the world’s leading supplier of thin film evaporation technology, this is due to the long-standing experience of the three former companies Luwa, SMS, Buss and Canzler. This long experience and expertise is now incorporated into Buss-SMS-Canzler. For our customers around the world we develop and manufacture machines and plants for evaporation, processing of highly viscous materials, membrane filtration and drying. Our...
Open the catalog to page 2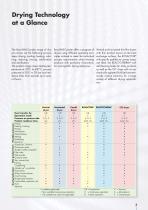
The Buss-SMS-Canzler range of dryers carries out the following process steps: drying, cooling, heating, calcining, reacting, mixing, sublimation and sterilisation. The product range covers heating temperatures of -20°C to 400°C, process pressures of 0,01 to 30 bar and residence times from seconds up to several hours. Buss-SMS-Canzler offers a program of dryers using different operating principles tailored to meet the individual process requirements when treating products with particular characteristics and specific drying behaviour. Vertical and horizontal thin film dryers with thin product...
Open the catalog to page 3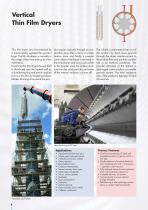
Vertical Thin Film Dryers Thin film dryers are characterised by a mechanically agitated thin product layer. The film thickness is normally in the range of less than one up to a few millimetres. In vertical thin film dryers the wet feed is distributed over the heated wall by a distributing ring and evenly applied to it in a thin film by hinged pendulum blades. Running downward the pro- duct passes typically through an evaporation zone, then a slurry or crystallisation zone and finally a powder zone. Most of the liquid is removed in the evaporation and slurry zone while in the powder zone the...
Open the catalog to page 4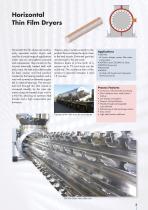
Horizontal Thin Film Dryers Horizontal thin film dryers are continuously operated contact dryers and used for a broad range of applications under vacuum, atmospheric pressure and overpressure. They consist of a horizontal externally heated shell with end covers, the inlet and outlet nozzles for feed, vapour and final product, nozzles for the heating medium and a rotor with screwed on elements supported in external bearings. The wet product fed through the inlet nozzle is conveyed steadily by the rotor elements along the heated dryer wall in a thin film, allowing an optimum heat transfer and...
Open the catalog to page 5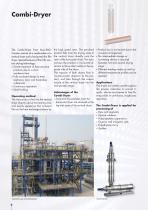
Combi-Dryer The Combi-Dryer from Buss-SMS-Canzler consists of a combination of a vertical dryer and a horizontal thin film dryer. Special features of thin film contact drying technology: • Gentle treatment of heat sensitive products due to a short residence time • Fully enclosed design to treat explosive, toxic and hazardous substances • Continuous operation • Small hold-up Operating method The wet product is fed into the vertical dryer directly above the heating zone and evenly spread as thin turbulent film on the heat exchange surface by the high speed rotor. The pre-dried product falls...
Open the catalog to page 6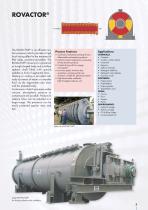
The ROVACTOR® is an efficient contact processor which provides a high local mixing effect for the treatment of filter cakes, powders and pellets. The ROVACTOR® consists of a cylindrical or trough shaped body and a hollow agitator shaft fitted with special paddles in form of segmental discs. Heating or cooling is provided indirectly by means of steam or a transfer fluid via the segmented rotor discs and the jacketed body. Continuous or batch processes under vacuum, atmospheric pressure or overpressure are possible. Product residence times can be adjusted in a large range. The processor can...
Open the catalog to page 7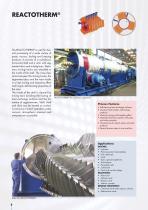
The REACTOTHERM® is used for thermal processing of a wide variety of pasty, viscous, fouling and lumping products. It consists of a cylindrical, horizontal shell and a rotor with segmented discs and mixing bars. Stationary mixing hooks are attached to the inside of the shell. The close clearance between the mixing hooks, the segmented discs and the rotor results in a high mixing and kneading effect and largely self-cleaning properties of the rotor. The inside of the shell is cleaned by mixing bars avoiding the fouling of heat exchange surfaces and the formation of agglomerates. Shell, shaft...
Open the catalog to page 8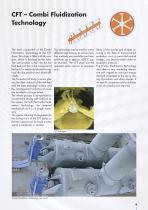
CFT – Combi Fluidization Technology The main component of the Combi Fluidization Technology is the CFT dryer. This dryer is filled with dry product, which is fluidized by the rotor. The wet product is fed into the hot fluid bed and due to the movement of the bed it is evenly distributed throughout the dry product and dried efficiently. The formation of sticky/viscous phases, the direct contact of the wet feed with the heat exchange surface and the consequential formation of crusts are avoided to a large extent. The whole process is comparable to conventional drying with external reflux...
Open the catalog to page 9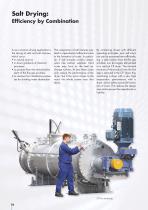
A very common drying application is the drying of salts and salt mixtures, which occur: • in natural sources • in down gradients of chemical processes • as product from the neutralization plant of the flue gas scrubber • as residue from membrane processes for drinking water abstraction The composition of salt mixtures may lead to operational malfunctions due to the formation of crusts. In particular, if salt mixtures contain components like sodium sulphate, hard crusts may form on the heat exchange surface. At best these crusts only reduce the performance of the dryer, but if the worst...
Open the catalog to page 10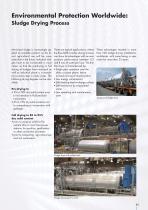
Environmental Protection Worldwide: Sludge Drying Process Municipal sludge is increasingly applied as valuable product, as the direct agricultural use will be more restrictive in the future. Industrial sludges have to be incinerated in most cases, so that the pre-drying or full drying of sludges from municipal as well as industrial plants is a mandatory process step in many cases. The following drying degrees can be classified: Pre-drying to • 35 to 50% dry solid content prior to incineration in fluidized bed incinerators • 65 to 75% dry solid content prior to composting or incineration...
Open the catalog to page 11All Buss SMS Canzler GmbH catalogs and technical brochures
-
Horizontal Thin Film Drye
1 Pages
-
Evaporation Technology
3 Pages
-
Membrane Technology
4 Pages
-
HYVAP DZH
2 Pages
-
REACTOTHERM®
2 Pages
-
Combi-Dryer
2 Pages
-
Sewage sludge drying
6 Pages
-
High Viscosity Technology
8 Pages
-
SMS Technologies
24 Pages
-
Short Path Evaporators
1 Pages
-
Horizontal Thin Film Drye
1 Pages
-
Vertical Thin Film Dryers
1 Pages