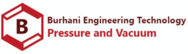
Catalog excerpts
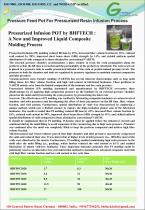
Pressurized Infusion POT by BHFTECH : A New and Improved Liquid Composite Molding Process Pressurized Infusion (PI) molding reduced fill time by 45%, increased fiber volume fraction by 16%, reduced void content by 98%, improved short beam shear (SBS) strength by 14%, and yielded uniform spatial distribution of voids compared to those obtained by conventional VARTM. The external pressure chamber accommodates a glass window to track the resin propagation along the preform so that the fill time is recorded and the permeability of the preform is calculated. The resin reservoir is placed in a pressure tank to enable pressurized infusion of the resin at predetermined pressure levels. The pressure in both the chamber and tank are regulated by pressure regulators to maintain constant compaction and inlet pressures Vacuum-assisted resin transfer molding (VARTM) has several inherent shortcomings such as long mold filling times, low fiber volume fraction, and high void content in fabricated laminates. These problems in VARTM mainly arise from the limited compaction of the laminate and low resin pressure. Pressurized infusion (PI) molding introduced and manufactured by BHFTECH overcomes these disadvantages by (i) applying high compaction pressure on the laminate by an external pressure chamber placed on the mold and (ii) increasing the resin pressure by pressurizing the inlet resin reservoir. The effectiveness of PI molding was verified by fabricating composite laminates at various levels of chamber and inlet pressures and investigating the effect of these parameters on the fill time, fiber volume fraction, and void content. Furthermore, spatial distribution of voids was characterized by employing a unique method, which uses a flatbed scanner to capture the high-resolution planar scan of the fabricated laminates. The results revealed that PI molding reduced fill time by 45%, increased fiber volume fraction by 16%, reduced void content by 98%, improved short beam shear (SBS) strength by 14%, and yielded uniform spatial distribution of voids compared to those obtained by conventional VARTM. It should be emphasized that in PI molding, Pchamber must be applied before the infusion is started and continued during the mold filling to avoid expansion of the vacuum bag due to high resin pressure. Pchamber was continued after the mold was completely filled to keep the preform compacted and achieve high fiber volume fraction. Microstructural and visual evidence proved that high chamber and inlet pressures successively compressed the voids and reduced their size. It was shown that at higher levels of inlet pressure (i.e., 180 kPa), most of the voids were dissolved in the matrix. Furthermore, PI molding enabled maintaining high resin pressure in the mold after the mold filling (i.e., packing), which further reduced the void content to 0.1% and enabled fabrication of almost void-free laminates. These important outcomes postulate that PI molding could be judiciously used as an alternative low-cost fabrication method to manufacture advanced composite materials with high fiber volume fraction and low void content at low cycle time Model No Capacity Gallon Capacity Litres Custom Sizes Manufactured on Demand 110 General Patters Road. Chennai – 600002. India. +919677296252, bhftech.info@gmail.com
Open the catalog to page 1All Burhani Engineering Technology catalogs and technical brochures
-
Expoxy resin
1 Pages
-
Vacuum Glove Box Metal Body
4 Pages
-
Acrylic Vacuum Glove Box
2 Pages
-
Epoxy Resin
2 Pages
-
Vacuum Leak Test Chamber
2 Pages
-
Heated Vacuum Chamber / Oven
1 Pages
-
Vacuum Degassing Chamber
1 Pages