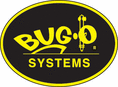
Catalog excerpts
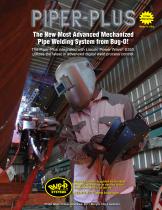
3 Year Warranty Made in USA The New Most Advanced Mechanized Pipe Welding System from Bug-O! The Piper-Plus integrated with Lincoln Power Wave® S350, utilizes the latest in advanced digital weld process control. Bug-O Systems is guided by honesty, integrity and ethics in service to our customers and in all we do. 412-331-1776 www.bugo.com Photo taken at New Industries, Inc. - Morgan City, Louisiana
Open the catalog to page 1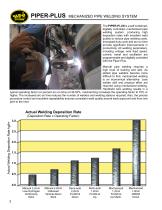
MECHANIZED PIPE WELDING SYSTEM The PIPER-PLUS is a self contained, digitally controlled, mechanized pipe welding system, producing high deposition rates with excellent weld quality to reduce pipe welding costs. Increased duty cycle and arc-on time provide significant improvements in productivity. All welding parameters, including voltage, wire feed speed, current, travel and oscillation are programmable and digitally controlled with the Piper-Plus. Manual pipe welding requires a high level of training and skill. As skilled pipe welders become more difficult to find, mechanized welding is an...
Open the catalog to page 2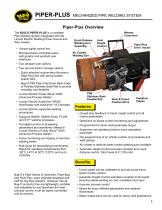
MECHANIZED PIPE WELDING SYSTEM Piper-Plus Overview The BUG-O PIPER-PLUS is a complete Pipe Welding System integrated with the Lincoln Electric Welding Power Source and Wire Feeder. • Unique digital control box • Microprocessor controlled panel with graphic and pendant user interfaces Weaver Cross Arm Quick Release Welding Gun Assembly Auto Height Control Piper-Plus Drive Tractor • Two pendant user options • Two rail and tractor carriage options ○ Quick attached custom-bent Aluminum Rigid Ring Rail with spring loaded spacer bars ○ Bug-O PSR Piper Flex Band Rails made of Flexible Stainless...
Open the catalog to page 3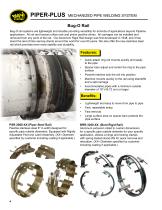
MECHANIZED PIPE WELDING SYSTEM Bug-O Rail Bug-O rail systems are lightweight and durable providing versatility for all kinds of applications beyond Pipeline applications. All rail and tractors utilize rack and pinion positive drives. All carriages can be installed and removed from any point of the rail. Our Aluminum Rigid Rail design was first developed in 1948, and it has stood the test of time serving clients around the world for over 60 years. We also offer the new stainless steel rail which provides even more stability and durability. Quick attach ring rail mounts quickly and easily to...
Open the catalog to page 4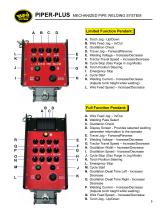
MECHANIZED PIPE WELDING SYSTEM Limited Function Pendant: A. Torch Jog - Up/Down B. Wire Feed Jog – In/Out C. Oscillation Check D. Travel Jog – Forward/Reverse E. Welding Voltage – Increase/Decrease F. Tractor Travel Speed – Increase/Decrease G. Cycle Stop (Gas Purge in Jog Mode) H. Torch Position Steering I. Emergency Stop J. Cycle Start K. Welding Current – Increase/Decrease (Adjusts torch height while welding) L. Wire Feed Speed – Increase/Decrease Full Function Pendant: A. Wire Feed Jog – In/Out B. Welding Pass Select C. Oscillation Check D. Display Screen - Provides selected welding...
Open the catalog to page 5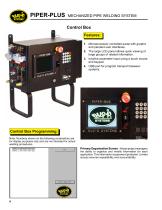
MECHANIZED PIPE WELDING SYSTEM Control Box Features: 1. Microprocessor controlled panel with graphic and pendant user interfaces. 2. The large LCD panel allows quick viewing of large groups of related information. 3. Intuitive parameter input using a touch mouse and keypad. 4. USB port for program transport between systems. Control Box Programming: Note: Numbers shown on the following screenshots are for display purposes only and are not intended for actual welding procedures. Primary Organization Screen – Allows project managers the ability to organize and modify information for each...
Open the catalog to page 6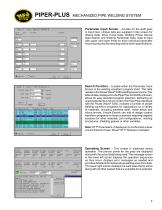
MECHANIZED PIPE WELDING SYSTEM ulri Trim unim>rf Parameter Input Screen - All data for the weld pass is input here. Unique tabs are supplied in this screen for Weave Data, Drive Travel Data, Welding Power Source Data Search and Welding Parameter Data. Data is input with upper and lower limits for each individual parameter thus ensuring that the resulting weld is within specifications. HEW» I TrfVtl_J SWPCh |_ Hfldlnf j Search Function - Located within the Parameter Input Screen is the welding waveform program chart. This data resides in the Power Wave® S350 welding powersource.This table of...
Open the catalog to page 7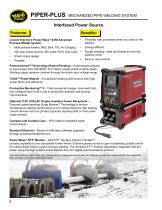
MECHANIZED PIPE WELDING SYSTEM Interfaced Power Source Features: Lincoln Electric’s Power Wave® S350 Advanced Process Welder System. • Flexibility with processes when not used on the pipeline Multi-process inverter, MIG, Stick, TIG, Arc Gouging Energy efficient 425 amp power source; 300 amps 100% duty cycle Smart robust design Rough handling - tried and tested all over the pipeline world PowerConnectTM Technology (Patent-Pending) – Automatically adjusts to input power from 200-600V, 50 or 60Hz, single phase or three phase. Welding output remains constant through the entire input voltage...
Open the catalog to page 8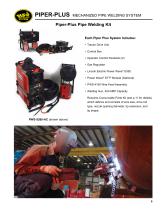
MECHANIZED PIPE WELDING SYSTEM Piper-Plus Pipe Welding Kit Each Piper Plus System Includes: • Tractor Drive Unit • Control Box • Operator Control Pendants (2) • Gas Regulator • Lincoln Electric Power Wave® S350 • Power Wave® STT® Module (Optional) • PWS-4100 Wire Feed Assembly • Welding Gun, 450 AMP Capacity Requires Consumable Parts Kit (see p.11 for details) which defines and consists of wire size, drive roll type, nozzle opening diameter, tip extension, and tip shape.
Open the catalog to page 9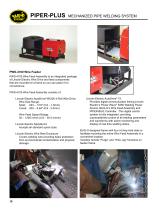
MECHANIZED PIPE WELDING SYSTEM PWS-4100 Wire Feeder PWS-4100 Wire Feed Assembly is an integrated package of Lincoln Electric Wire Drive and feed components that are mounted to a frame so you can place it for convenience. PWS-4100 Wire Feed Assembly consists of: Lincoln Electric AutoDrive® 4R220 4-Roll Wire Drive. Wire Size Range: Solid: .023 – 1/16" (0.6 – 1.6mm) Cored: .035 – 5-64" (0.9 - 2.0mm) Wire Feed Speed Range: 30 – 1200 in/min (0.8 – 30.5 m/min) Lincoln Electric Spindle Kit Accepts all standard spool sizes. Lincoln Electric Wire Reel Enclosure Covers welding wire providing basic...
Open the catalog to page 10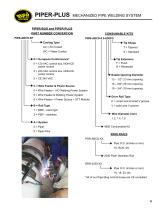
MECHANIZED PIPE WELDING SYSTEM PIPER-BUG and PIPER-PLUS PART NUMBER CONVENTION CONSUMABLE KITS Cooling Type D = European Conformance* 0 = 120 VAC control box, NON-CE power source Tip Extension F = Flush R = Recessed 2 = 240 VAC control box, NON-CE power source Nozzle Opening Diameter C = Wire Feeder & Power Source 0 = Wire Feeder – NO Welding Power System 5 = Wire Feeder & Welding Power System Drive Roll Type 6 = Wire Feeder + Power Source + STT Module K = cored wire knurled V groove B = Rail Type 2 = PSR – stainless V = solid wire V groove RING RAILS PSR-ABCD-XX 2000 Piper Stainless Rail...
Open the catalog to page 11All BUG-O SYSTEMS catalogs and technical brochures
-
UNI-BUGS
4 Pages
-
AUTOMATIC ARC GOUGING SYSTEM
4 Pages
-
FIXTURING EQUIPMENT
4 Pages
-
PIPER-PLUS PIPE WELDING SYSTEM
12 Pages
-
STIFFENER WELDERS
4 Pages
-
SUPPORTS AND ACCESSORIES
4 Pages
-
RAILS & ATTACHMENTS
8 Pages
-
BEVELERS
2 Pages
-
GO-FER® IV
6 Pages
-
AUTOMATIC HEIGHT CONTROL
2 Pages
-
Zipper Welder
4 Pages
-
K-BUG 5050/K-BUG 6050
4 Pages
-
Arc Gouger
4 Pages
-
FixturesEquipment
4 Pages
-
Tank Fabrication
8 Pages
-
DC Speed Weaving Kit
2 Pages
-
Supports & Accessories
4 Pages
-
Programmable Shape Machine
4 Pages
-
DC-IV Tractor
2 Pages
-
Trac-Bug
2 Pages
-
Uni-bug III
4 Pages
-
Unibug II
4 Pages
-
Speed Weaver II
4 Pages
-
Beam Bug III
4 Pages
-
Universal Bug-o-matic
4 Pages
-
Con-o
2 Pages
-
Cir-o
2 Pages
-
Hob-o
2 Pages
-
General Catalogue
24 Pages
-
Modular Drive System
16 Pages
-
Weld Backings
2 Pages
-
Portable Plate Beveler
2 Pages
-
Hob-o Blind Area Kit
2 Pages
-
Torches
2 Pages
-
Go-fer III
6 Pages
-
Programmable Gantry
4 Pages
-
Auto Height Control
2 Pages
-
TAR-GIT
2 Pages
-
Pitbull Beveler
2 Pages
-
Stiffener Welder
4 Pages
-
DC General Welding Kit
2 Pages
-
All Position Overlay System
2 Pages
-
Heavy Duty Sub-arc Tractor
2 Pages
-
Pipe-Bug
4 Pages
Archived catalogs
-
Sprinkler Brochure
6 Pages
-
Weld Backings
2 Pages