
Catalog excerpts
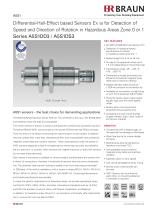
Differential-Hall-Effect based Sensors Ex ia for Detection of Speed and Direction of Rotation in Hazardous Areas Zone 0 or 1 Series A5S1DD3 / A5S1DS3 KEY FEATURES SIL3/IEC 61508:2010 certified by TÜV Detection of rotational speed and direction of rotation in hazardous areas Zone 0 or 1 Speed range from 0 Hz to 25 kHz Air gap to the gear/pole wheel up to 1.5 mm (depending on the profile size) Temperature range -40…+125 °C (-40…+255 °F) Differential principle diminishes the influence of external magnetic stray fields and of machine vibration Sealed stainless steel enclosure > 200 bar pressure to the sensor tip Available for connection via tight plug, or with firmly attached Teflon® cable A5S1 Overall View A5S1 sensors – the best choice for demanding applications The BRAUN Speed Sensors Series A5S are TÜV certified for SIL3 acc. IEC 61508:2010 and therefore meet the high SIL3 standards. Powerful square wave output signal equally high over the entire speed range Sensor short circuit proof and protected versus polarity error Accepting fine and coarse profiles, as gear wheels, slots, cams, holes in any ferrous material The correct choice of sensor is always a prerequisite to achieving a successful solution. Therefore BRAUN A5S1 sensors base on the proven Differential-Hall-Effect principle. Contact-free with a large air gap, so the potential for damage is eliminated Their low end of 0 Hz allows monitoring the machine down to zero speed. In addition, they are contact-free, wear-free, maintenance-free, and unsusceptible versus external magnetic stray fields and machine vibration. These characteristics make the series of A5S1 sensors especially suited for all applications where high accuracy and reliability are at a premium. In contrast, other sensors like magnet-inductive or static Hall sensors do not meet these demands. Each sensor in the series is available in various lengths and diameters and comes with a choice of connections. However, functionally all sensors have the same characteristics. The stainless steel sensor housing is sealed at the front and pressure-resistant (> 200 bars). A flat shaft is available or with a screw-in thread M12x1, M14x1, M14x1,5, M16x1, M16x1,5, M18x1, M18x1,5, M22x1, 5/8-18UNF-2A. Customized dimensions and thread specifications are possible. To meet the specific requirements of hazardous areas, we provide specialized types Wear-free due to its unique design principle Maintenance-free during lifetime, therefore minimized TCO Unsusceptible versus external magnetic stray fields and machine vibration Operates down to zero speed Can not be damaged by faulty wiring Almost every wheel profile can be used A5S1 Sensors do not influence each other, no mounting distance in between is required certified for ATEX, UKEX, IECEx, and other international standards such as UL/CSA and EAC (the Eurasian Customs Union with Russia, Kazakhstan, and Belarus). In addition, for hazardous areas (Zone 0-1), we provide an intrinsically safe implementation in conjunction with our Barrier D461. www.braun-
Open the catalog to page 1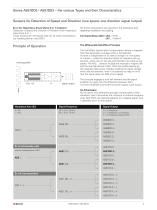
Series A5S1DD3 / A5S1DS3 – the various Types and their Characteristics Sensors for Detection of Speed and Direction (one speed, one direction signal output) Ex ia for Hazardous Areas (Zone 0 or 1 location) Detection of Speed and Direction of Rotation within hazardous areas Zone 0 or 1. These sensors are intrinsically safe (Ex ia) when connected to our Isolating Barrier units D461. No further precautions are required in the hazardous area regarding installation and cabling. The Differential-Hall-Effect Principle The Hall effect (named after its discoverer) utilizes a magnetic field that...
Open the catalog to page 2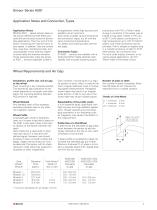
Sensor Series A5S1 Application Notes and Connection Types Application Notes BRAUN A5S1… speed sensors base on the proven Differential-Hall-Effect principle and are the best choice for demanding applications. Their low end of 0 Hz allows monitoring the machine down to zero speed. In addition, they are contactfree, wear-free, maintenance-free, and unsusceptible versus external magnetic stray fields and machine vibration. These characteristics make the series of A5S1… sensors especially suited to all applications where high accuracy and reliability are at a premium. Each series includes...
Open the catalog to page 3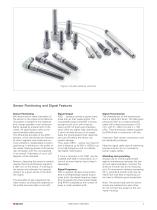
Figure includes special versions Sensor Positioning and Signal Features Sensor Positioning We recommend a radial orientation of the sensor to the wheel circumference. Its position in parallel to the rotational axis, though possible, may involve problems caused by a lateral shift of the wheel. All specifications refer to the recommended radial position. The differential principle of the A5S1… sensors, which diminishes the influence of other magnetic stray fields and machine vibrations, necessitates a correct positioning in reference to the profile of the wheel. Marking planes at the sensor...
Open the catalog to page 4
Standard Design Versions length L Plug-in version shown with straight metal connector Plug-in version shown with angled metal connector Version with fixed Teflon® cable attached NPT-version with fixed Teflon® cable, only for 5/8"-18 (inch) thread See Ordering Key for available thread diameters D and length L A5S1DD3 / A5S1DS3
Open the catalog to page 5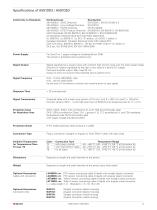
Specifications of A5S1DD3 / A5S1DS3 Conformity to Standards EU-Directive(s) Standard(s) 2014/30/EU (EMC Directive) EN 61326-1, EN IEC 61326-3-2 2014/35/EU (Low Voltage Directive) EN 61010-1 2011/65/EU (RoHS Directive) EN IEC 63000 2014/34/EU (ATEX Product Directive) EN 60079-0, EN 60079-11, EN 60079-26 UKEX Standards: BS EN 60079-0, BS EN 60079-11, BS EN 60079-26 US Standards: National Electrical Code (NEC) dated 2014 UL 60079-0, UL 60079-11, UL 913 - 8 th edition, UL 61010-1, edition 3 Canadian Standards: Canadian Electrical Code (CEC) dated 2012 CSA C22.2 Nos. 60079-0, 60079-11, 157-92,...
Open the catalog to page 6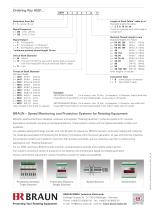
Length of fixed Teflon® cable in m* Standard lengths for cable: x = 2, 5, 8, 10, 15, 20 *(omit for versions with screw-plug-in connection) Hazardous Area (Ex) 1 = Ex version (Ex ia) Signal Frequency b = DD : Hz...25 kHz 0 b = DS : 0 Hz...12 kHz Signal Output c = 0 : x Frequency 1 c = 3 : 1x Frequency / 1x Direction* c = 4 : 2x Frequency, phase-shifted* *minimum nominal thread length 74 mm Unit of Shaft Diameter d = M : Metric d = N : Inch and 1/2"-NPT at rear end of sensor (only in conjunc- tion with thread 5/8"-18 (inch) and fixed Teflon® cable) d = U : Inch Thread of Shaft Diameter...
Open the catalog to page 7All BRAUN GMBH Industrie-Elektronik catalogs and technical brochures
-
A5S1DS4…-n
7 Pages
-
A5S1DS3-n (Ex nA)
7 Pages
-
A5S1DS0-n (Ex nA)
7 Pages
-
A5S1DD4-n (Ex nA)
7 Pages
-
A5S1DD3-n (Ex nA)
7 Pages
-
D461R1
6 Pages
-
A5S1DS4-n (Ex nA)
7 Pages
-
A5S1DS4 (Ex ia)
7 Pages
-
A5S1DS3 (Ex ia)
7 Pages
-
A5S1DS0 (Ex ia)
7 Pages
-
A5S1DD4 (Ex ia)
7 Pages
-
A5S1DD0 (Ex ia)
7 Pages
-
A5S0DS4 (non-hazardous area)
7 Pages
-
A5S0DS3 (non-hazardous area)
7 Pages
-
A5S0DS0 (non-hazardous area)
7 Pages
-
A5S0DD4 (non-hazardous area)
7 Pages
-
A5S0DD3 (non-hazardous area)
7 Pages
-
A5S0DD0 (non-hazardous area)
7 Pages
-
A5S1DD0-n (Ex nA)
7 Pages
-
Series D521.xx
4 Pages
-
A5S Overview
8 Pages
-
E16521D.2 (SIL2)
6 Pages
-
E16521D.1 (SIL2)
6 Pages
-
E16521D.3 (SIL2)
6 Pages
-
E16x342 (SIL3)
4 Pages
-
E16x352 (SIL3)
4 Pages
-
E16x346 (SIL3)
4 Pages
-
E16x356 (SIL3)
4 Pages