
Catalog excerpts
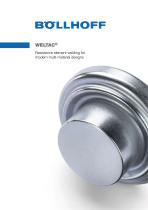
WELTAC® Resistance element welding for modern multi-material car body design
Open the catalog to page 1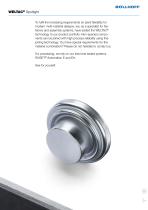
The WELTAC® system General Setting process Your advantages Fastener module Variants WELTAC® element Joint qualities Assembly system module WELTAC® Automation EH WELTAC® outlook Core components at a glance
Open the catalog to page 3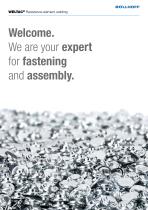
WELTAC® Resistance element welding – Technology Car bodies are increasingly influenced by multi-material design. The classical joining technologies, for example resistance spot welding, cannot be used since the materials are not or only limited thermally compatible. This concerns mainly aluminium and steel. In order to fulfil these requirements, Böllhoff - as a specialist for fasteners and assembly systems - added another technology to its existing product portfolio. By using the resistance element welding WELTAC®, you are flexible: lightweight materials (aluminium, sandwich materials,...
Open the catalog to page 4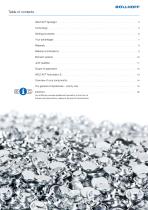
WELTAC® Resistance element welding – Your advantages Your benefits at a glance: n High-strength joints n Use of existing, conventional spot-welding equipment in the body construction shop possible n On a single body construction line, different multi-material designs can be flexibly combined n Wide application range regarding material qualities and thicknesses (aluminium and steel), incl. press-hardened steel n Processing with a proven, electric-hydraulic RIVSET® system n All from a single source: joint design, element, automation and worldwide after-sales service in the wellknown Böllhoff...
Open the catalog to page 5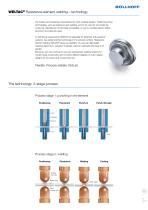
WELTAC® Resistance element welding – Materials WELTAC® offers a wide application range in regard to steel and aluminium combinations in two-sheet, three-sheet and four-sheet stack-ups: Aluminium n Aluminium sheets, extruded profiles and die casting components n Aluminium material thicknesses from 0.8 mm to 3.2 mm using standardised fastener design (higher material thicknesses available on request) Steel n Cold- and hot-rolled steel of all property classes n Press-hardened steel Do you have individual requirements regarding material combinations? Talk to us.
Open the catalog to page 6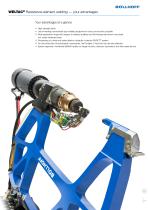
WELTAC® Resistance element welding – Material combinations Al5xxx sheet 0.8 mm High-strength steel 2.0 mm Al6xxx extrusion profil 3.0 mm Structual adhesive Steel deep-drawing grade 1.0 mm Al die cast 3.0 mm Structual adhesive High-strength steel 1.75 mm Al6xxx sheet 1.2 mm Steel deep-drawing grade 1.0 mm Press-hardened steel 1.6 mm Super high-strength steel 1.5 mm Al5xxx sheet 1.5 mm Structual adhesive Steel deep-drawing grade 1.0 mm Al5xxx sheet 0.8 mm Al7xxx sheet 2.0 mm Steel deep-drawing grade 1.0 mm Press-hardened steel 1.6 mm Super high-strength steel 1.5 mm Structual adhesive Al5xxx...
Open the catalog to page 7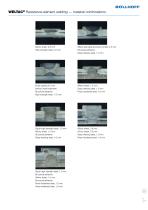
The WELTAC® system General Setting process Your advantages Fastener module Variants WELTAC® element Joint qualities Assembly system module WELTAC® Automation EH WELTAC® outlook Core components at a glance
Open the catalog to page 9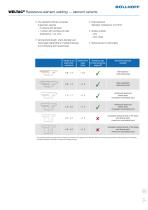
WELTAC® Resistance element welding – Variants n Standard portfolio includes 6 geometrical variants – 5 variants using a flat head – 1 variant using a countersunk head – (interference contour < 0.4 mm) n Variation of shaft length, shaft diameter and head height aligned with material thickness and mechanical requirements n Heat treatment Standard: cured to 410 HV10 n Plating systems – Zinc – Zinc-nickel n Produced in our own production using a cold-forging process Field of application sheet thickness (mm) Clamping groove* for loosening necessary? Design/ mechanical load Flat head shape / low...
Open the catalog to page 10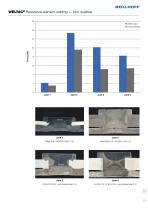
WELTAC® Resistance element welding – Joint qualities 16 n Shear strength n Cross tension strength
Open the catalog to page 11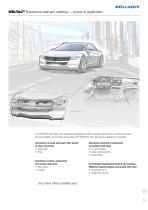
The WELTAC® technology has been particularly developed for special requirements in the car body design. Components made of different materials can be joined reliably with WELTAC®, e. g.: Outer panels in aluminium (thin sheet) on steel structures n Side panels n Roof Panel components made of aluminium in steel environments n Floor parts n Front wall
Open the catalog to page 12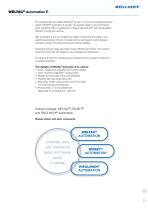
Structural parts made of aluminium in steel environments n C- and D-pillar n Crash reinforcements n Instrument panel support Multifunctional die casting parts in steel environments n Suspension strut n Hinge knot rear lid ... and many more applications
Open the catalog to page 13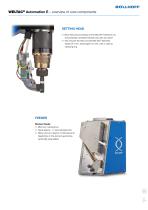
The WELTAC® system General Setting process Your advantages Fastener module Variants WELTAC® element Joint qualities Assembly system module WELTAC® Automation EH WELTAC® outlook Core components at a glance
Open the catalog to page 15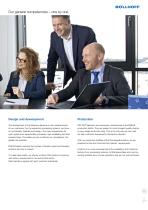
WELTAC® Automation EH Our resistance element welding WELTAC® is linked to our proven assembly system RIVSET® Automation EH. Due its the modular design, the system is designated for applications in large-scale production with maximum flexibility during production planning. A high duration of life and minimum maintenance effort are important factors and basis for a successful production. The highlights of WELTAC® Automation EH at a glance: n Modular and comprehensive machine designs n Machine configuration via plug & play n Process times ≤ 1.5 seconds / element (depending on the setting tool)...
Open the catalog to page 17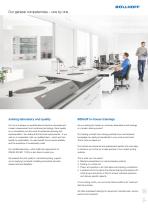
WELTAC® Resistance element welding – Core components at a glance TOOL Setting tool EH n Setting tool with electrical drive for setting forces 10 – 35 kN n Pre-clamping force adjusted with pressure springs n Various mounting points on the setting tool for perfect position on the robot n C-frames throat depths to 1,000 mm n Modular die post with special die support and C-frame for the slug removal FEED Element feeder n Minimum maintenance at maximum availability n Feeds approx. 45 elements/minute n Stockage of approx. 4,000 elements (optionally expandable)
Open the catalog to page 18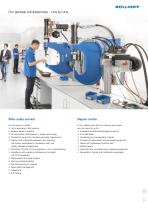
SETTING HEAD n Blow feeding and processing of WELTAC® elements via pneumatic-controlled transport into the duct bend n Ensures also the feeding of small WELTAC® elements (shaft Ø 4 mm, total length 2.6 mm), with or without clamping ring C-FRAME The modular system: With the new C-frame, you will have the possibility to generate a minimum number of base frames for a maximum number of setting tool variants. Your advantages: n Optimised Nearly parallel opening of the C-frame supports improved connectivity quality. n Simple You can configure the rivet setting tools by yourself. n Effective The...
Open the catalog to page 19All BÖLLHOFF catalogs and technical brochures
-
KAPTI NUT® Captive nuts
4 Pages
-
HITSERT® Screwlock
6 Pages
-
HELICOIL® Smart
28 Pages
-
QUICKLOC®
16 Pages
-
Products and Services
40 Pages
-
ONSERT®
10 Pages
-
RIVTAC®
14 Pages
-
HELICOIL® Tangfree
28 Pages
-
Product Guide
20 Pages
-
HELICOIL® Plus
56 Pages
-
TEPRO®
24 Pages
-
IMTEC® Moulded inserts
8 Pages
-
SEAL LOCK® Sealing nuts
8 Pages