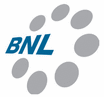
Catalog excerpts
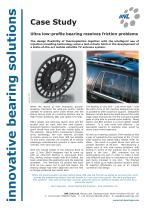
Ultra low-profile bearing resolves friction problems The design flexibility of thermoplastics together with the intelligent use of injection moulding technology solve a last-minute hitch in the development of a state-of-the-art mobile satellite TV antenna system. innovative bearing solutions Case Study When the launch of KVH Industries’ groundbreaking TracVision A5 ultra-low profile mobile satellite TV antenna came under threat with the failure during trails of a bushing solution due to high friction problems, BNL was called in to help. BNL’s design and technical teams soon got the project back on track with two new customdesigned injection moulded parts – a bearing and giant thrust race that form the mobile base of the antenna. Using KVH’s revolutionary phasedarray technology, the new antenna provides in-motion access to more than 300 live satellite TV and music channels via virtually all in-vehicle passenger entertainment systems in sport utility vehicles, mini-vans and cars. With the overall height of the antenna fixed at just 11.5cm, BNL’s designers had to come up with an ultra-thin bearing in ultra-quick time. But, having worked closely with KVH before, the team understood the application and the potential problems. The TracVision A5 project had been alive for two years, but in just two weeks, the bearing design had been approved and the first prototype produced two weeks later. The bearing is very thin – just 9mm high – with the pitch circle of the raceway designed as large as possible to offer maximum support. Integrated features include belt drive teeth around the outer edge, brass inserts to fix it to the unit and moulded pads on one side to provide extra stability. Being plastic, the BNL product is a much lighter weight solution. It is also more cost effective - an equivalent bearing in stainless steel would be many times more expensive. As well as a bearing solution, KVH needed to find a way of supporting the perimeter of the 77.5cm wide antenna and asked BNL’s design team for ideas. The result is a giant thrust race with an outside diameter of 63.5cm. Manufacturing a plastic part of this size causes problems with tooling in terms of the expense due to wasted space in the tool. BNL overcame this by sectionalising the part in order to make it both cost effective and easy to manufacture with each part being moulded in one shot. The finished part is made up of eight identical sections which fit together effortlessly by way of an integral connection clip design. “When the bushing system we were testing failed, BNL was the first call we placed as we knew they could provide the engineering support that was needed in a very short time period. We had a problem and they solved it. They told us what they could do, delivered what we needed on budget and in time for a successful launch.” Gerry Maynard - Senior Mechanical Engineer - KVH Industries, Inc. BNL (UK) Ltd Manse Lane Knaresborough North Yorkshire HG5 8LF UK T: +44 (0)1423 799200 (main) F: +44 (0)1423 862259 (main) E: sales@bnl-bearings.com www
Open the catalog to page 1All BNL catalogs and technical brochures
-
Water Shower Enclosures
1 Pages
-
Plastic bearing
1 Pages
-
Standard Products
16 Pages
-
Heavy Duty Bearings
1 Pages
-
Twin Shot Technology
1 Pages
-
Integrated Assemblies
1 Pages
-
Shaft Technology
1 Pages
-
Water Technology
1 Pages
-
Mini Bearings
2 Pages
-
Free Flow Technology
1 Pages
Archived catalogs
-
BNL - Clips & Fixings
1 Pages