
Group: ITW Industrial finishing
Catalog excerpts
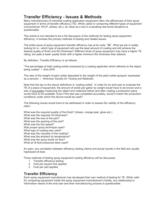
Many manufacturers of industrial coating application equipment often cite efficiencies of their spray equipment in terms of transfer efficiency (TE). While useful in comparing different types of equipment (conventional, HVLP, airless, etc.), its value as a tool in evaluating real-world situations is questionable. This article is not intended to be a full discussion of the methods for testing spray equipment efficiency. It reviews the primary methods of testing and related issues. The entire issue of spray equipment transfer efficiency has at its roots, $$Ӕ. What we are in reality looking for is - which type of equipment will use the least amount of coating and still achieve the desired quality of finish and film thickness? Different kinds of spray equipment may have a higher TE rating, but yield a lower quality finish with a higher minimum film thickness than desired. By definition, Transfer Efficiency is as follows: The percentage of total coating solids employed by a coating applicator which adheres to the object being coatedӔ -- Ohio EPA The ratio of the weight of paint solids deposited to the weight of the paint solids sprayed, expressed as a percent. -- American Society for Testing and Materials Note that the key to the above definitions is coating solidsӔ. In order for an end-user to evaluate the TE of a piece of equipment, the amount of solids per gallon by weight would have to be known and a way of accurately measuring the object and materials before and after coating a production piece would have to be available. Even if the test was completed accurately, would it match the production conditions under which the device would be used? The following issues would have to be addressed in order to assess the validity of the efficiency claim: What was the required quality of the finish? (sheen, orange peel, gloss etc.) What was the required mil thickness? What was the size of the part? What was the spacing of the part? What was the line speed? Was proper spray technique used? What type of coating was used? What was the viscosity of the coating? What was the ambient air temperature? What was the spray booth air flow? What air & fluid pressures were used? As seen, any correlation between efficiency testing claims and actual results in the field are usually haphazard at best. Three methods of testing spray equipment coating efficiency will be discussed. 1. Transfer efficiency testing. 2. Cost per square foot applied 3. Cost per part applied. > Each spray equipment manufacturer has developed their own method of testing for TE. While valid for comparing equipment inside the spray equipment manufacturers facility, any relationship to information needs of the end-user and their manufacturing process is questionable. >
Open the catalog to page 1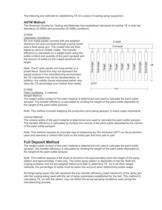
The following are methods for establishing TE for a piece of coating spray equipment. > The American Society for Testing and Materials has established standards for testing TE in both the laboratory (D-5009) and production (D-5286) conditions. D-5009 Laboratory Conditions .Six inch metal panels covered with pre-weighed aluminum foil and conveyed through a spray booth past a fixed spray gun. The coated foils are then baked to remove volatile matter. The transfer efficiency is calculated on a weight basis using the solids content and quantity of the paint sprayed and the amount of solids on...
Open the catalog to page 2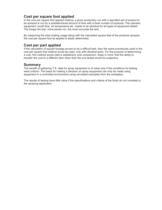
In the cost per square foot applied method, a given production run with a specified set of product to be sprayed is run for a predetermined amount of time with a fixed number of products. The operator, equipment, booth flow, air temperature etc. needs to be identical for all types of equipment tested. The longer the test, more pieces run, the more accurate the test. By measuring the total coating usage along with the calculated square feet of the products sprayed, the cost per square foot as applied is easily determined. > If the calculation of square footage proves to be a difficult task,...
Open the catalog to page 3All Binks catalogs and technical brochures
-
AG-364
4 Pages
-
Premium Elevator Systems
7 Pages
-
RVC
2 Pages
-
AGMD PRO
2 Pages
-
AX200L AIR MOTOR ASSEMBLIES
10 Pages
-
AIR ASSIST PUMP ASSEMBLY
16 Pages
-
BINKS MX SERIES
4 Pages
-
AA1600M
6 Pages
-
MAG II
4 Pages
-
2100
4 Pages
-
75
2 Pages
-
AG-363
2 Pages
-
GEMINI II Series
8 Pages
-
LEL Spray Guns
2 Pages
-
MX412
28 Pages
-
BINKS TROPHY SERIES
60 Pages
Archived catalogs
-
Rhino Automatic Spray Gun
1 Pages
-
Sun Skeeter
4 Pages
-
Magnalube-G
5 Pages
-
A-F High Efficiency Filter
3 Pages
-
Air Motor Oil - Motor Oil
7 Pages
-
Cleaner
5 Pages
-
Desiccant (air dryer)
4 Pages
-
Premium Desiccant
4 Pages
-
Lubricating Oil
4 Pages
-
White Booth Coat
6 Pages
-
Binks Pump Purj - Pump Purg
4 Pages
-
Watt Lube
3 Pages
-
Scrubs
4 Pages
-
A-F Filter
3 Pages
-
Wet Sol Plus
5 Pages
-
Spray Gun Lube
4 Pages
-
Booth Filter
4 Pages
-
spray vantage 3
2 Pages