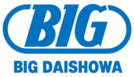

Catalog excerpts
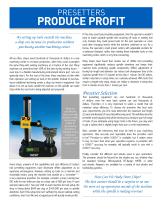
PRODUCE PROFIT By setting up tools outside the machine, a shop can increase its production without purchasing another machining center. All too often, shops invest hundreds of thousands of dollars in a new machining center to increase production, when they could accomplish the same thing with existing machinery at a fraction of the cost. Many machines cut metal less than 50% of the time during working hours— even less in a flexible manufacturing environment where part runs are generally short. For the rest of the time, these machines sit idle while their operators are setting up tools in the spindle. Instead of purchasing an additional machining center, a shop can invest in equipment that allows it to set up tools outside the machine, so the spindle can make chips while the next tool is being adjusted and prepared. Diaset is a cost effective, easy to use high precision, contact tool presetter suitable for any workshop environment. Individual locking mechanisms along the Z and X axes provide fine adjustments. Some shops, unaware of the capabilities and cost efficiency of today’s tool presetting equipment, have dismissed offline adjustment as an expensive extravagance. However, setting up tools on a machine tool essentially means using the machine tool spindle as a “presetter”— a very expensive presetter. For example, consider a shop running four CNC mills for two shifts per day at a shop rate of $80 per hour. If each operator takes only 1 hour per shift on each machine for tool setup, the shop is losing about $640 per day, or $160,000 per year, to spindle downtime. And if this setup time isn’t sufficient to ensure optimal cutting conditions, short tool life and scrapped parts will quickly erode profits. If this shop used tool presetting equipment, then the operators wouldn’t have to waste valuable spindle time touching off tools or making trial cuts. Instead, they could preset tools for the next operation or reset tools after changing inserts while the machine continues to run. As a bonus, the operators could preset cutters with adjustable pockets for a balanced chipload, rather than setting these indexable tools on the machining center, which is very time-consuming. Many shops have found that routine use of offline tool presetting equipment significantly reduces spindle downtime and keeps their machine tools producing quality components. Offline adjustment of boring bar length and diameter can reduce tool-changeover time at the machine spindle from 15 minutes to less than 1 minute. On CNC lathes, similar reductions in setup times are routinely achieved. With tools that require a length-only setup, shops can realize a reduction in setup time from 5 minutes to less than 1 minute per tool. Presetter Selection Tool presetting equipment can cost hundreds of thousands of dollars; even the most basic system can cost thousands of dollars. Therefore, it is very important to select a model that will maximize setup efficiency. To choose the presetter that best suits your requirements, you first must determine the maximum tool length (Z-axis) and diameter (X-axis) that will be measured. This will determine the presetter travel capacity that will be necessary to measure your full range of tools. If you anticipate using larger tools in the future, you may want to get a system that is slightly larger than your current requirements. Next, consider the tolerances that must be held in your machining operations. How accurate and repeatable does the presetter need to be? Precision to within 0.0001" is available, but it makes sense to buy no more than what your operation requires. A presetter with a 0.0001" accuracy, for example, will typically result in cuts with a 0.0001" accuracy. Finally, consider the different tool shanks used in your operations. The presetter should be fixtured for the shanks you run, whether they be standard V-flange, DIN-standard, BT-flange, NMTB, or lathe tool shanks. Adapters are available for a variety of tool shanks and toolholding systems. How Can We Make More Chips? The best answer should be a surprise to no one Do more set up operations outside of the machine while the spindle is maki
Open the catalog to page 1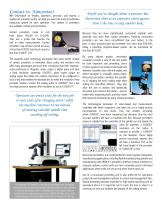
With information on lengths, diameters, precision, and shanks, a quality tool presetter vendor can help you select the most cost-effective measuring system for your operation. Two classes of presetters are available: contact and noncontact. Contact presetters range in cost from about $5,000 to $10,000. They use a probe that touches the tool to make measurements. Contact presetters may achieve overall accuracy of less than 0.0005" and check runout to less than 0.0003" T.I.R. The magnetic-scale technology associated with some earlier models of contact presetters is outmoded. Glass scales and...
Open the catalog to page 2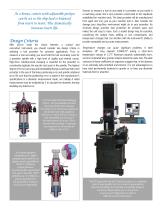
As a bonus, cutters with adjustable pockets can be set so the chip load is balanced from insert to insert. This dramatically increases insert life. Design Criteria After you’ve made the choice between a contact and noncontact instrument, you should consider two design criteria in selecting a tool presetter for precision applications. First, to measure a tool accurately, you must hold the tool accurately. Look for a presetter spindle with a high level of rigidity and minimal runout. High-force retention-knob clamping is essential for the presetter to consistently duplicate the way the tool...
Open the catalog to page 3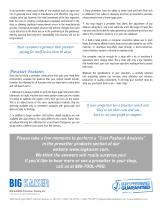
A tool presetter constructed solely of one material such as aged cast iron is generally more costly to manufacture and, therefore, may carry a higher price tag. However, this initial investment will be less expensive than the cost of creating a temperature-regulated environment in the shop or allowing significant measurement errors in the manufacturing process. A temperature-stable structure will prevent changes that could cause distortion in the linear axis or in the positioning of the guideways, thereby assuring that long-term repeatability and accuracy will not be compromised. Most...
Open the catalog to page 4All BIG KAISER Precision Tooling Inc. catalogs and technical brochures
-
MEASURING INSTRUMENTS
8 Pages
-
CUTTING DATA TABLES
144 Pages
-
MODULAR WORKHOLDING SYSTEM VOL. 3
112 Pages
-
BIG KAISER Drill Tapper
4 Pages