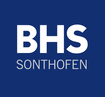
Catalog excerpts
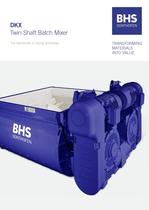
Twin-Shaft Batch Mixer The benchmark in mixing technology INTO VALUE
Open the catalog to page 1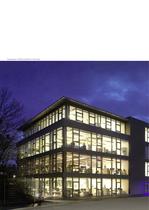
Headquarter of BHS-Sonthofen in Germany
Open the catalog to page 2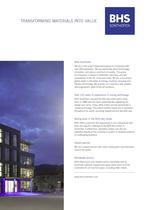
BHS-Sonthofen We are a mid-sized independent group of companies with over 300 employees. We are passionate about technology, innovative, and place a premium on quality. The group of companies is based in Sonthofen, Germany, and has subsidiaries in the US, China and India. We are a successful global player in the fields of mixing, crushing, recycling and filtration technology. We provide our customers with reliable, well-engineered, state-of-the-art solutions. Over 125 years of experience in mixing technology BHS-Sonthofen invented the first twin-shaft batch mixer back in 1888 and has been...
Open the catalog to page 3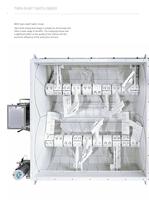
Twin-shaft batch mixer 4 BHS twin-shaft batch mixer Twin-shaft mixing technology is suitable for all formulas and offers a wide range of benefits. The mixing technique has a significant effect on the quality of the mixture and the economic efficiency of the production process.
Open the catalog to page 4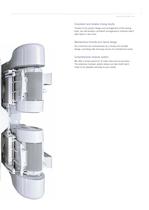
Consistent and reliable mixing results Thanks to the proven design and arrangement of the mixing tools, you will achieve consistent homogeneous mixtures batch after batch in less time. Maintenance-friendly and robust design Our machines are characterized by a sturdy and durable design, providing safe and easy access for maintenance work. Comprehensive modular system We offer a broad spectrum of mixer sizes and accessories. The extensive modular system allows our twin-shaft batch mixer to be adapted precisely to your needs.
Open the catalog to page 5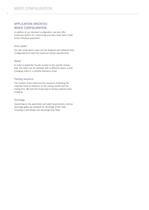
Application-oriented mixer configuration In addition to our standard configuration, we also offer numerous options for customizing your twin-shaft batch mixer to the individual application. Drive power Our twin-shaft batch mixer can be designed with different drive configurations to meet the maximum torque requirements. Speed In order to adapt the Froude number to the specific mixing task, the mixer can be operated with a different speed, a polechanging motor or a variable-frequency drive. Feeding sequence The location of the inlets and the sequence of feeding the materials have an...
Open the catalog to page 6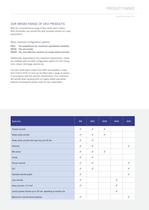
Product range 7 www.bhs-sonthofen.com Our broad range of DKX products With the comprehensive range of twin-shaft batch mixers, BHS-Sonthofen can provide the best possible solution for many applications. Basic machine configuration options DKX: The powerhouse for maximum operational reliability DKXS: The all-rounder DKXN: The cost-effective solution for ready-mixed concrete Additionally, depending on the individual requirements, mixers are available with versatile configuration options for the mixing tools, drives, discharge variants etc. The twin-shaft batch mixers from BHS are available in...
Open the catalog to page 7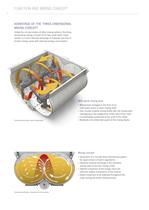
Function and mixing concept 8 Advantage of the three-dimensional mixing concept Unlike the circular motion of other mixing systems, the threedimensional mixing concept of the twin-shaft batch mixer results in a more intensive exchange of materials and thus in shorter mixing cycles with reduced energy consumption. BHS spiral mixing tools Functional principle: spiral mixing tools » Mixing tools arranged in the form of an interrupted spiral on each mixing shaft » Two counter-rotating mixing shafts with the mixing tools overlapping in the longitudinal center area of the mixer » Counterblades...
Open the catalog to page 8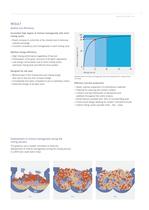
Result Quality and efficiency Consistent high degree of mixture homogeneity with short mixing cycles Mixture homogeneity (%) » Rapid increase in uniformity of the mixture due to intensive material exchange » Constant consistency and homogeneity in each mixing cycle Optimal energy efficiency » High mixing performance regardless of low rpm » Preservation of the grain structure of all batch ingredients » Low energy consumption due to short mixing cycles, optimized mixing tools and efficient drive system Designed for low wear » Minimal wear of the mixing tools and mixing trough liner due to low...
Open the catalog to page 9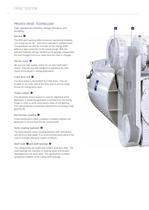
Proven drive technology High operational reliability, energy efficiency and durability Gearbox The BHS worm gearing offers maximum operational reliability and a long service life – even when exposed to extreme loads. The gearboxes are directly mounted on the mixing shafts without a rigid connection to the mixing trough. With the selected materials pairing, the BHS worm gearing compensates the load changes that occur every time the mixer is charged. Electric motor We use only high-quality motors for our twin-shaft batch mixers. They are specially designed to withstand the load cycles...
Open the catalog to page 10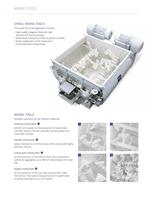
Spiral mixing tools The basis for a homogeneous mixture » High-quality hexagonal shaft with high torsional and flexural strength » Streamlined mixing arms made of special cast steel » Spiral configuration of the mixing arms » Easily adjustable mixing blades Mixing tools Suitable solutions for all mixture materials Universal mixing tools with 60° arm position for the production of ready-mixed concrete, precast concrete, specialty concrete grades and many other mixtures. Smooth mixing tools reduce adhesion to a minimum even when working with highly adhesive mixtures. Coarse-grain mixing...
Open the catalog to page 12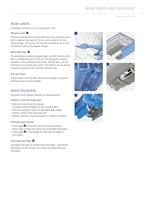
Wear liners and discharge 13 www.bhs-sonthofen.com Wear liners Innovative solutions for a long service life Rhombus tiles Rhombus-shaped tiles made of optimized cast chromium steel with a material thickness of 19 mm can be used to line the mixing trough. The service life can be increased by up to 30% compared to tiles of rectangular design. OPTILONG tiles For applications subject to greater wear, we offer rhombus tiles with a material thickness of 28 mm. By varying the material hardness of the individual rows of tiles, uniform wear can be achieved across all the wear zones. The lifetime...
Open the catalog to page 13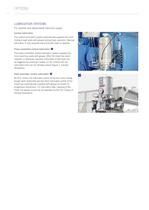
Lubrication systems For optimal and dependable lubricant supply Central lubrication The central lubrication system automatically supplies the inner mixing trough seals with grease during mixer operation. Manual lubrication is only required every time the mixer is cleaned. Pulse-controlled central lubrication The pulse-controlled central lubrication system supplies the inner axial face seals with grease. After the mixer has been cleaned, or whenever required, lubrication of the seals can be triggered by pressing a button on the control unit; the lubrication time can be infinitely varied...
Open the catalog to page 14All BHS Sonthofen Process Technology catalogs and technical brochures
-
BFR Rubber Belt Filter
12 Pages
-
RPF Rotary Pressure Filter
16 Pages
-
BF Indexing Belt Filter
16 Pages
-
CF Candle Filter
16 Pages
-
LCS Liquid Clarification Systems
24 Pages
-
Pressure plate filter (PF)
12 Pages
-
Rotary pressure filter
16 Pages
-
Indexing belt filter
16 Pages
-
PF
12 Pages
Archived catalogs
-
DMX Dry Powder Batch Mixer
20 Pages
-
Mixing & Crushing
32 Pages
-
NGU Universal Shredder
12 Pages
-
LFK Twin-Shaft Continuous Mixer
12 Pages
-
DKX Twin-Shaft Batch Mixer
20 Pages
-
NGV SpeedCut Granulator
12 Pages
-
RS Rotorshredder
16 Pages
-
RPM & RPMF Rotor Impact Mill
9 Pages
-
VR Rotary Shear
12 Pages
-
VSR Pre-Shredder
12 Pages
-
RPMV & RPMX Rotor impact mill
16 Pages
-
RBG Biogrinder
12 Pages
-
DKXC Combimix System
8 Pages
-
DKXK Twin-shaft batch mixer
2 Pages
-
RPMV
12 Pages
-
RPM
12 Pages
-
PB & PM
12 Pages
-
MONOMIX & TWINMIX
12 Pages
-
Biogrinder
12 Pages
-
VSI Rotor Centrifugal Crusher
16 Pages