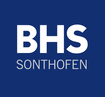
Catalog excerpts
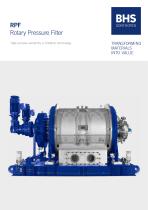
High process versatility in filtration technology TRANSFORMING MATERIALS INTO VALUE
Open the catalog to page 1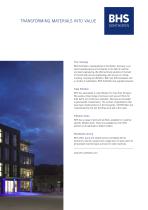
TRANSFORMING MATERIALS INTO VALUE The company BHS-Sonthofen, headquartered in Sonthofen, Germany, is an owner-operated group of companies in the field of machine and plant engineering. We offer technical solutions in the field of mechanical process engineering, with a focus on mixing, crushing, recycling and filtration. With over 300 employees and a number of subsidiaries, BHS-Sonthofen has a global presence. Cake filtration BHS has specialized in cake filtration for more than 50 years. We supply a broad range of pressure and vacuum filters for both batch and continuous operation. We have...
Open the catalog to page 3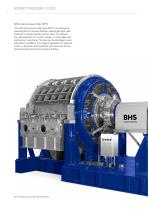
ROTARY PRESSURE FILTER 4 BHS rotary pressure filter (RPF) The BHS rotary pressure filter (type RPF) is a continuously operating filter for pressure filtration, allowing gas-tight cake treatment in several separate process steps. For example the cake treatment can consist of single- or mutli-stage cake washing and cake drying. The cake can be discharged under atmospheric conditions. The range of applications is wide and covers, in particular, bulk chemicals, fine chemicals and the pharmaceutical and food processing industries. RPF X16 rotary pressure filter with CenterDrive
Open the catalog to page 4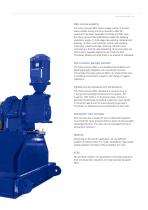
High process versatility The rotary pressure filter makes a large number of process steps possible during one drum revolution. After the suspension has been separated into filtrate and filter cake, the rotary pressure filter additionally enables the following operations: single- or multi-stage cake washing, displacement washing, counter-current washing, closed-cycle washing, reslurrying, solvent exchange, steaming, extraction and mechanical or thermal cake dewatering. All process steps are performed in separate segment zones inside the filter. This allows filtrates and other fluids to be...
Open the catalog to page 5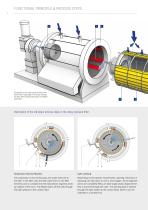
FUNCTIONAL PRINCIPLE & PROCESS STEPS 6 3D graphic of the rotary pressure filter, with drum shown separately. The arrows indicate the flow of feed media (dark blue) and filtrate (light blue). Description of the individual process steps in the rotary pressure filter Suspension feed & filtration Cake washing The suspension is fed continuously and under pressure to the filter. In the filter cells, the filter cake forms on the filter elements and is conveyed into the downstream segment zones by rotation of the drum. The filtrate drains off the cells through the pipe systems to the control head....
Open the catalog to page 6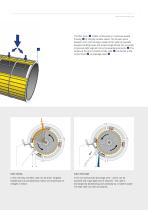
The filter drum 1 rotates continuously in a pressure-sealed housing 2 at infinitely variable speed. The annular space between drum and housing is sealed to the sides by specially designed stuffing boxes and divided longitudinally into a number of pressure-tight segment zones by separating elements 3 . The surface of the drum consists of filter cells 4 connected to the control head 6 via drainage pipes 5 . Cake drying Cake discharge In the next step, the filter cake can be dried. Targeted dewatering is accomplished by means of compressed air, nitrogen or steam. In the...
Open the catalog to page 7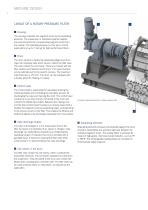
LAYOUT OF A ROTARY PRESSURE FILTER 1 The housing is divided into segment zones by the separating elements. The suspension or individual treatment agents are pressure-fed to the corresponding segment zones from the outside. The operating pressure is 3 bar (g) in normal applications or up to 7 bar (g) for high-performance filters. 2 The drum surface is divided by separating ledges and drum rings into individual cells which serve to collect the filter cake. The cells contain the cell inserts. These are covered with the filter medium and fastened to the drum. The cake thickness can be optimally...
Open the catalog to page 8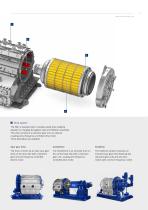
The filter is equipped with a variable-speed drive enabling adaption to changing throughput rates and filtration properties. This drive consists of a reduction gear unit, an optional coupling and a frequency-controlled drive motor. Three alternatives are available: Spur gear drive The drum is driven by an open spur gear drive on the drive side with a reduction gear unit and frequency-controlled electric motor. The CenterDrive is an enclosed drive on the control head side with a reduction gear unit, coupling and frequencycontrolled drive motor. The TwinDrive variant comprises an enclosed...
Open the catalog to page 9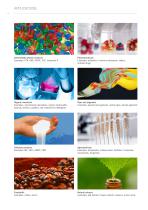
Intermediate plastic products Examples: PTA, ABS, HDPE, PVC, bisphenol A Pharmaceuticals Examples: antibiotics, hormone derivatives, statins, antiviral drugs Organic chemicals Examples: vulcanization derivatives, sodium hydrosulfite, phenyls, amines, paraffins, raw materials for detergents Dyes and pigments Examples: pearlescent pigments, aniline dyes, silicate pigments Cellulose products Examples: MC, HEC, HMEC, CMC Agrochemicals Examples: phosphates, molluscicides, fertilizers, herbicides, insecticides, fungicides Foodstuffs Examples: coffee, starch Natural extracts Examples: leaf...
Open the catalog to page 10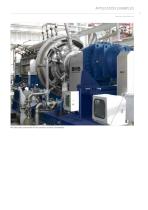
APPLICATION EXAMPLES 11 www.bhs-sonthofen.com RPF B16 rotary pressure filter for the production of plastic intermediates
Open the catalog to page 11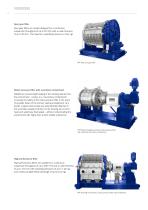
Spur gear filter Spur gear filters are usually designed for a continuous suspension throughput of up to 25 m³/h with a cake thickness of up to 30 mm. The maximum operating pressure is 3 bar (g). RPF B16 spur gear filter Rotary pressure filter with secondary containment Additional, pressure-tight sealing of the working spaces from the environment – known as a “secondary containment” – increases the safety of the rotary pressure filter in the event of possible failure of the primary sealing arrangement. Any liquids or gases that escape are systematically detected in the secondary sealing...
Open the catalog to page 12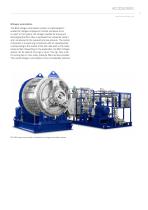
Nitrogen recirculation The BHS nitrogen recirculation system is implemented to enable the nitrogen employed in inerted processes to be re-used. In this system, the nitrogen needed for drying and discharging the filter cake is separated from entrained solvent and compressed to the required process pressure. The central component is a liquid ring compressor with an operating fluid corresponding to the solvent of the last cake wash in the rotary pressure filter. Depending on the application, the BHS nitrogen system can be rated at 3 bar (g) or up to 7 bar (g). Twin units for serving two or...
Open the catalog to page 13All BHS Sonthofen Process Technology catalogs and technical brochures
-
BFR Rubber Belt Filter
12 Pages
-
RPF Rotary Pressure Filter
16 Pages
-
BF Indexing Belt Filter
16 Pages
-
CF Candle Filter
16 Pages
-
LCS Liquid Clarification Systems
24 Pages
-
Pressure plate filter (PF)
12 Pages
-
Indexing belt filter
16 Pages
-
PF
12 Pages
Archived catalogs
-
DMX Dry Powder Batch Mixer
20 Pages
-
Mixing & Crushing
32 Pages
-
NGU Universal Shredder
12 Pages
-
LFK Twin-Shaft Continuous Mixer
12 Pages
-
DKX Twin-Shaft Batch Mixer
20 Pages
-
NGV SpeedCut Granulator
12 Pages
-
RS Rotorshredder
16 Pages
-
RPM & RPMF Rotor Impact Mill
9 Pages
-
VR Rotary Shear
12 Pages
-
VSR Pre-Shredder
12 Pages
-
RPMV & RPMX Rotor impact mill
16 Pages
-
RBG Biogrinder
12 Pages
-
DKXC Combimix System
8 Pages
-
DKXK Twin-shaft batch mixer
2 Pages
-
RPMV
12 Pages
-
RPM
12 Pages
-
PB & PM
12 Pages
-
MONOMIX & TWINMIX
12 Pages
-
Biogrinder
12 Pages
-
VSI Rotor Centrifugal Crusher
16 Pages
-
Twin-shaft batch mixer
20 Pages