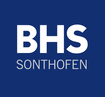
Catalog excerpts
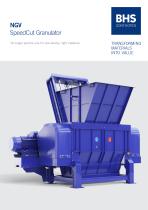
On-target particle size for low-density, light materials TRANSFORMING MATERIALS INTO VALUE
Open the catalog to page 1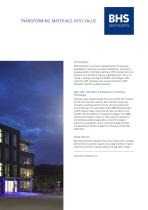
TRANSFORMING MATERIALS INTO VALUE The Company BHS-Sonthofen is an owner-operated group of companies specialized in machinery and plant engineering. The group is headquartered in Sonthofen, Germany. BHS provides technical solutions for mechanical process engineering with a focus on mixing, crushing, recycling and filtration technologies. With more than 300 employees and several subsidiaries, BHS-Sonthofen maintains a global presence. More than 100 Years of Experience in Crushing Technology 100 years have already passed since we built the first crushers for the rock and stone industry. We...
Open the catalog to page 3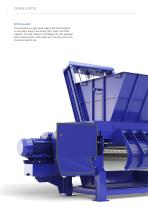
BHS Granulator The Granulator is a high-speed single-shaft cutter designed for secondary sizing of low-density, light, elastic and brittle materials. The feed material is cut between the rotor equipped with fly blades and the static blade seat. The final product has the desired particle size.
Open the catalog to page 4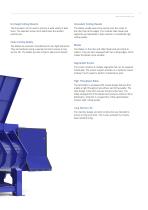
On-Target Cutting Results Consistent Cutting Results The Granulator can be used to process a wide variety of feed stock. The selected screen pitch determines the desired particle size. The blades usually wear more quickly near the center of the rotor than at the edges. The modular static blade seat segments are adjustable to help maintain a consistently high cutting quality. Clean Cutting Quality The blades are precision manufactured to very tight tolerances. They are hardened using a special process to ensure a long service life. The blades are also simple to adjust and replace. Blades The...
Open the catalog to page 5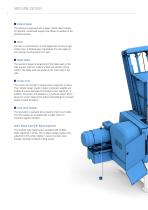
Infeed Hopper The machine is equipped with a large, central infeed hopper. On demand, customized hoppers are offered in addition to the standard versions. 2 The rotor is produced from a solid forged part and has a high inertia mass. A rotating wear ring protects the rotor edges at the housing mounting point from wear. 3 The special V-shaped arrangement of the blade seats on the rotor ensures optimum material infeed and optimal cutting results. The blade seats are welded to the main body of the rotor. 4 The screen unit consists of several screen segments in series. This modular design...
Open the catalog to page 6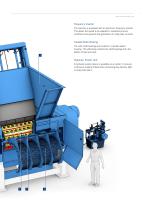
Frequency Inverter The machine is equipped with an electronic frequency inverter. This allows the speed to be adapted to individual process conditions and prevents the generation of costly peak currents. Isolated Rotor Bearing The rotor shaft bearings are located in a double-walled housing. This effectively protects the shaft bearings from the effects of heat and dust. 1 Hydraulic Pusher Unit A hydraulic pusher device is available as an option. It ensures continuous material infeed when processing low-density, light or bulky feed stock.
Open the catalog to page 7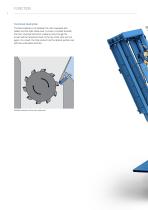
Functional Description The feed material is cut between the rotor equipped with blades and the static blade seat. A screen is located beneath the rotor. Oversize feed stock unable to pass through the screen will be transported back to the top of the rotor and cut again. As a result, the final product has the desired particle size with few undersized particles. Detailed illustration of the static blade seat
Open the catalog to page 8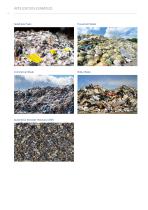
Substitute Fuels Household Waste Commercial Waste Bulky Waste Automotive Shredder Residues (ASR)
Open the catalog to page 10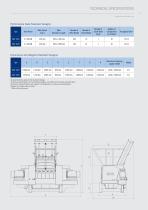
TECHNICAL SPECIFICATIONS 11 www.bhs-sonthofen.com Performance Data (Standard Designs) Type Drive Power Rotor Diameter x Length Number of Rotor Blades Number of Static Blades Number of Static Blade Seats Number of Cutting Rows on the Rotor Dimensions and Weights (Standard Designs) Type Work Access Opening Length x Width All specifications apply to the standard design. Technical specifications for customized designs may differ from the data provided here. All technical specifications are subject to change due to continuous development. Subject to change without n
Open the catalog to page 11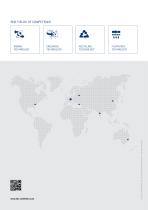
CRUSHING TECHNOLOGY RECYCLING TECHNOLOGY FILTRATION TECHNOLOGY 05.2016_801000246_EN, © 2016 BHS-Sonthofen GmbH – All rights reserved. MIXING TECHNOLOGY
Open the catalog to page 12All BHS Sonthofen Process Technology catalogs and technical brochures
-
BFR Rubber Belt Filter
12 Pages
-
RPF Rotary Pressure Filter
16 Pages
-
BF Indexing Belt Filter
16 Pages
-
CF Candle Filter
16 Pages
-
LCS Liquid Clarification Systems
24 Pages
-
Pressure plate filter (PF)
12 Pages
-
Rotary pressure filter
16 Pages
-
Indexing belt filter
16 Pages
-
PF
12 Pages
Archived catalogs
-
DMX Dry Powder Batch Mixer
20 Pages
-
Mixing & Crushing
32 Pages
-
NGU Universal Shredder
12 Pages
-
LFK Twin-Shaft Continuous Mixer
12 Pages
-
DKX Twin-Shaft Batch Mixer
20 Pages
-
RS Rotorshredder
16 Pages
-
RPM & RPMF Rotor Impact Mill
9 Pages
-
VR Rotary Shear
12 Pages
-
VSR Pre-Shredder
12 Pages
-
RPMV & RPMX Rotor impact mill
16 Pages
-
RBG Biogrinder
12 Pages
-
DKXC Combimix System
8 Pages
-
DKXK Twin-shaft batch mixer
2 Pages
-
RPMV
12 Pages
-
RPM
12 Pages
-
PB & PM
12 Pages
-
MONOMIX & TWINMIX
12 Pages
-
Biogrinder
12 Pages
-
VSI Rotor Centrifugal Crusher
16 Pages
-
Twin-shaft batch mixer
20 Pages