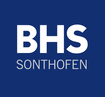
Catalog excerpts
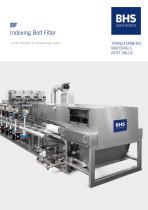
Gentle filtration of sedimenting media TRANSFORMING MATERIALS INTO VALUE
Open the catalog to page 1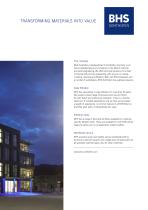
TRANSFORMING MATERIALS INTO VALUE The company BHS-Sonthofen, headquartered in Sonthofen, Germany, is an owner-operated group of companies in the field of machine and plant engineering. We offer technical solutions in the field of mechanical process engineering, with a focus on mixing, crushing, recycling and filtration. With over 300 employees and a number of subsidiaries, BHS-Sonthofen has a global presence. Cake filtration BHS has specialized in cake filtration for more than 50 years. We supply a broad range of pressure and vacuum filters for both batch and continuous operation. There is...
Open the catalog to page 3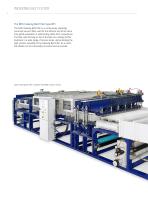
INDEXING BELT FILTER 4 The BHS Indexing Belt Filter (type BF) The BHS Indexing Belt Filter is a continuously operating, horizontal vacuum filter used for the efficient and at the same time gentle separation of sedimenting solids from suspensions. The filter cake forming on top of the belt can undergo further treatment in a wide range of process steps, demonstrating the high process versatility of the Indexing Belt Filter. As a result, the filtrates can be individually recovered and processed. Open Indexing Belt Filter of type BF 200-080 in plastic version
Open the catalog to page 4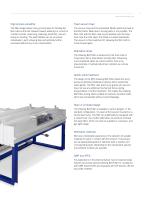
High process versatility Fixed vacuum trays The filter design allows many process steps for treating the filter cake as the belt indexes forward: washing (co-current or counter-current), reslurrying, steaming, extraction, vacuum drying or pressing. The wash filtrates can be recovered individually in each indexing step and optimally further processed without any cross-contamination. The vacuum trays and the associated filtrate outlets are fixed to the filter frame. Wear due to moving parts is not possible. The filter cloth with the filter cake moves stepwise over the trays. Each time the...
Open the catalog to page 5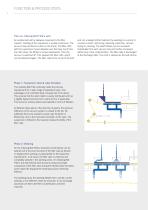
FUNCTION & PROCESS STEPS 6 How our Indexing Belt Filters work An endless belt with a stepwise movement is the filter medium. Feeding of the suspension is usually continuous. The vacuum trays are fixed in place on the frame. The filter cloth with the suspension moves stepwise over the trays. Each time the cloth stops, the filtrate is sucked downwards. Then the vacuum is switched off. This releases the filter cloth, which can be advanced again. The filter cake forms on top of the belt Phase 1: Suspension feed & cake formation The Indexing Belt Filter optimally meets the process requirements...
Open the catalog to page 6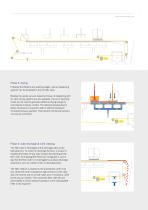
Phase 3: Drying Following the filtration and washing stages, various dewatering systems can be employed to dry the filter cake. Besides the purely vacuum-based technique of dewatering with air, other drying systems are also available. Hot air or steaming hoods can be used to generate additional drying energy for reducing the moisture content. The optional pressing device allows mechanical compaction with or without blowing for increased pressure gradient. Thermal and mechanical systems can also be combined. Phase 4: Cake discharge & cloth cleaning The filter cake is discharged at the...
Open the catalog to page 7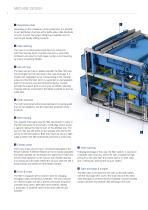
Depending on the consistency of the suspension, it is possible to use distribution channels with a baffle plate, plate distributor or spoon nozzles. Slurry-feed designs are available even for viscous and rapidly settling products. 2 The cake is normally washed with full-cone nozzles for solid-free washing liquid. Overflow channels or sieve plate distributors are used for multi-stage counter-current washing by means of washing filtrates. 3 The fixed vacuum tray is installed beneath the filter cloth over the full length from the feed area to the cake discharge. It is divided into segregated...
Open the catalog to page 8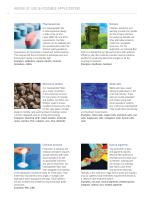
Pharmaceuticals Our Indexing Belt Filter of pharmaceutical design is state of the art and meets GMP, CIP and ATEX requirements. Our filter systems can be validated and are manufactured under the strictest quality guidelines. Suspensions are processed in closed and inerted systems. This ensures that the final product is absolutely pure and that product quality is consistently high. Examples: antibiotics, natural extracts, hormone derivatives, statins Biofuels Filtration, extraction and washing of solids from liquids are the primary methods for producing biofuels and other alternative...
Open the catalog to page 10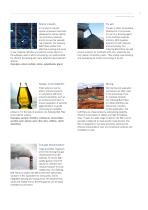
Silicon industry In the silicon industry special processes have been developed to ensure optimal use of primary materials and to recover the valuable raw materials. Our Indexing Belt Filters enable cost-effective recycling and reuse of raw materials. Whether you want to recover silicon or the additives used in silicon processing, our systems allow for efficient processing with many different cake treatment options. Examples: silicon carbide, silicon, polyethylene glycol Fly ash is either immediately disposed of or processed for use as a bonding agent in the building materials industry. BHS...
Open the catalog to page 11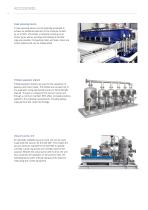
Cake pressing device A cake pressing device can be optionally employed to achieve an additional reduction of the moisture content by up to 50%. Pneumatic or hydraulic pressing up to 10 bar (g) as well as pressing and blowing of the filter cake are possible. Compacting rollers and press rollers are further options that can be implemented. Filtrate separator station Filtrate separator stations are used for the separation of gaseous and liquid media. The filtrates are pumped out of the separators using appropriate pumps or barometrically drained. The gas is conveyed to the vacuum pump unit...
Open the catalog to page 12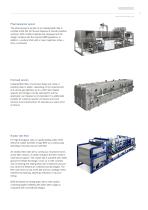
Pharmaceutical version The pharmaceutical version of an Indexing Belt Filter is certified to EN ISO 22716 and disposes of smooth-polished surfaces. FDA-certified materials are employed and the design complies with the required GMP guidelines. In addition, a surface finish with a mean roughness index < 0.8 µ is achieved. Enclosed version Indexing Belt Filters of enclosed design are made of stainless steel or plastic, depending on the requirements, and ensure gas-tightness up to ± 100 mbar. Sealed systems and nitrogen circuits optimized to suit the application can likewise be incorporated. It...
Open the catalog to page 13All BHS Sonthofen Process Technology catalogs and technical brochures
-
BFR Rubber Belt Filter
12 Pages
-
RPF Rotary Pressure Filter
16 Pages
-
CF Candle Filter
16 Pages
-
LCS Liquid Clarification Systems
24 Pages
-
Pressure plate filter (PF)
12 Pages
-
Rotary pressure filter
16 Pages
-
Indexing belt filter
16 Pages
-
PF
12 Pages
Archived catalogs
-
DMX Dry Powder Batch Mixer
20 Pages
-
Mixing & Crushing
32 Pages
-
NGU Universal Shredder
12 Pages
-
LFK Twin-Shaft Continuous Mixer
12 Pages
-
DKX Twin-Shaft Batch Mixer
20 Pages
-
NGV SpeedCut Granulator
12 Pages
-
RS Rotorshredder
16 Pages
-
RPM & RPMF Rotor Impact Mill
9 Pages
-
VR Rotary Shear
12 Pages
-
VSR Pre-Shredder
12 Pages
-
RPMV & RPMX Rotor impact mill
16 Pages
-
RBG Biogrinder
12 Pages
-
DKXC Combimix System
8 Pages
-
DKXK Twin-shaft batch mixer
2 Pages
-
RPMV
12 Pages
-
RPM
12 Pages
-
PB & PM
12 Pages
-
MONOMIX & TWINMIX
12 Pages
-
Biogrinder
12 Pages
-
VSI Rotor Centrifugal Crusher
16 Pages
-
Twin-shaft batch mixer
20 Pages