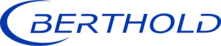
Group: Berthold

Catalog excerpts
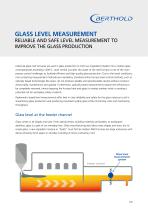
GLASS LEVEL MEASUREMENT RELIABLE AND SAFE LEVEL MEASUREMENT TO IMPROVE THE GLASS PRODUCTION Industrial glass melt furnaces are used in glass production to melt raw ingredients (batch) into a molten glass at temperatures exceeding 1200°C. Level control just after the outlet of the melt furnace is one of the main process control challenges to facilitate efficient and high-quality glass production. Due to the harsh conditions, non-contacting measurement methods are mandatory. Standard online furnace level control methods, such as optically based technologies like lasers, do not produce reliable and reproduceable results without constant, almost daily, maintenance and upkeep. Furthermore, optically based measurements require the refractory to be completely removed, hence exposing the furnace heat and gases to nearby workers what is creating a potential risk for workplace safety incidents. Radiometric based level measurements offer best in class reliability and safety for the glass industry to aid in streamlining glass production and producing consistent quality glass while minimizing costs and maximizing throughput. Glass level at the feeder channel Glass comes in all shapes and sizes. From optical lenses, building materials and bottles, to toothpaste additives, glass is a part of our everyday lives. Glass manufacturing also takes many shapes and sizes, but to create glass, a raw ingredient mixture or “batch” must first be melted. Melt furnaces are large enclosures with dense refractory brick layers on all sides including at times a refractory roof. Glass level measurement system Feeder channel
Open the catalog to page 1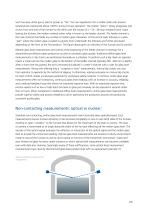
Such furnaces utilize gas or electric power to “fire” the raw ingredients into a molten state with process temperatures maintained above 1200°C during furnace operation. The molten “batch” slowly progresses and churns from one end of the furnace to the other over the course of a ~ 24 - 48 hour residence time. Upon leaving the furnace, the molten material enters what is known as the feeder channel. The feeder channel is the main channel that feeds any number of molten glass tributaries. At the end of each tributary is a glass “pull” where the molten glass is pulled via gravity from...
Open the catalog to page 2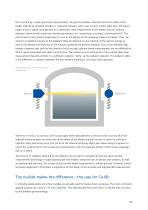
Non-contacting, nuclear glass level measurements use gamma radiation directed across the width of the feeder channel to correlate changes in measured radiation with a rise or fall in molten glass level. The figure below shows a typical arrangement of a radiometric level measurement at the feeder channel. Gamma radiation interacts with matter by transferring energy in an “everything or nothing” phenomenon (2). This phenomenon has a greater propensity to occur as the density of the opposing medium increases. Thus, the amount of radiation present at the radiation detector depends on the...
Open the catalog to page 3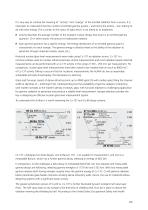
It is very easy to confuse the meaning of “activity” and “energy” of the emitted radiation from a source. It is important to understand that the number of emitted gamma quanta – and hence the activity – has nothing to do with their energy. This is similar to the colour of light which is not linked to its brightness. ■ Activity describes the average number of the isotope’s nuclear decays that result in an emitted gamma quantum. Or in other words: the amount of radioactive material. gamma quantum has a specific energy. The energy distribution of an emitted gamma quant is characteristic for...
Open the catalog to page 4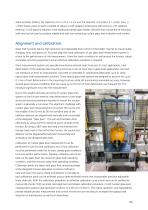
Administration (OSHA), the steel HVL of Cs-137 is 1.6 cm and the steel HVL of Co-60 is 2.1 cm (6). Thus, a > 30% thicker piece of steel is needed to reduce Co-60 radiation entering by half versus Cs-137 radiation entering. Co-60 gamma radiation more readily penetrates glass feeder channels that include dense refractory walls and can be used to produce reliable and safe non-contacting nuclear glass level indication and control. Alignment and calibration: Glass melt furnaces require high resolution and repeatable level control of the feeder channel to ensure stable charging, flow, and glass...
Open the catalog to page 5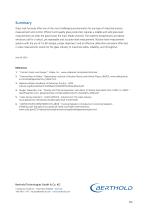
Summary Glass melt furnaces offer one of the most challenging environments for any type of industrial process measurement and control. Efficient and quality glass production requires a reliable and safe glass level measurement just after the glass leaves the main feeder channel. The extreme temperatures and dense refractory call for a robust, yet repeatable and accurate level measurement. Nuclear level measurement systems with the use of Co-60 isotope, proper alignment, and an effective calibration procedure offer best in class measurement results for the glass industry to maximize safety,...
Open the catalog to page 6All Berthold Technologies Process Control catalogs and technical brochures
-
Mould level measurement
4 Pages
-
Density measurement
5 Pages
-
Continuous level measurement
5 Pages
-
Retrofit
3 Pages
-
Article "Made to measure"
3 Pages
-
Moisture in pasta production
3 Pages
-
Glass level measurement
3 Pages
-
Mould level measurement
4 Pages
-
LB 475 Fracturing system
3 Pages
-
Multiphase level measurement
7 Pages
-
Produkt InlineSENS
4 Pages
-
Industry Sugar
9 Pages
-
LB472 Bulk Flow Meter
12 Pages
-
MEVIS
4 Pages
-
NUMo - LB 134 UMo II
2 Pages
-
Radiation Protection Instruments
12 Pages
-
Micro-Polar
16 Pages
-
DuoSeries Detectors LB 4700
2 Pages
-
Rod Source Shielding
4 Pages
-
Safety Source Capsule SSC
2 Pages
-
Level Switch LB 471
6 Pages