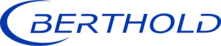

Catalog excerpts
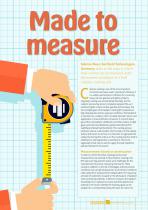
Sabrina Nees, Berthold Technologies, Germany, looks at the ways in which level control can be improved under the extreme conditions of a fluid catalytic cracking unit. atalytic cracking is one of the most important conversion processes used in petroleum refineries. It is a widely used process in refineries for converting heavy oils into gasoline and lighter products. Originally, cracking was accomplished thermally, but the catalytic process has almost completely replaced this, as it produces higher octane number gasoline and less heavy fuel oils and light gases. Fluid catalytic cracking (FCC) operates at high temperatures and low-pressure conditions. The feedstock is injected into a catalyst which circulates between reactor and regenerator to ensure efficient conversion. It converts heavy gas oil from atmospheric distillation and other streams to light gases, petrochemical feedstock, gasoline blendstock (FCC naphtha) and diesel fuel blendstock. The cracking process produces coke as a side product which remains on the catalyst surface and lowers its activity. It is important to regenerate the catalyst by burning this coke in air. The cracking reaction itself is endothermic and regeneration is exothermic. Hence the regeneration heat can be used to supply the heat needed to preheat the feed to the reactor. Measurement based on attenuation In order to control the entire cracking process, level measurements are essential. In fluid catalytic cracking units (FCCUs), level measurement poses some challenges for the manufacturers of process measuring instruments. These include, in addition to the risk of blockages, extreme process conditions such as high temperatures. Such extreme conditions make radiometric measurements indispensable. The measuring principle of radiometry is based on the attenuation of radiation when penetrating materials. A detector measures the radiation emanating from a radioactive source and attenuated by the material in the vessel, whereby the resulting signal can be assigned to a corresponding measured value, by means of a 29 Reprinted from April 2020
Open the catalog to page 1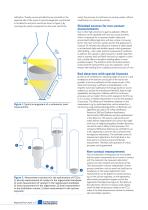
calibration. Thereby source and detector are mounted on the opposite side of the vessel. A typical arrangement would entail a rod detector and point sources (as shown in Figure 1). By mounting the system components on the outer wall of the vessel, they are easy to install even on existing vessels, without modifications or process downtimes. Shielded sources for non-contact measurements Due to their high sensitivity to gamma radiation, efficient detectors can be operated with very low source activities, which is important for a customer’s health, safety and environment (HSE) programme, and...
Open the catalog to page 2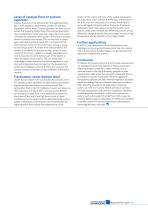
Level of catalyst fines in cyclone separator Catalyst fines have to be removed from the regenerator flue gas to fulfil regulatory requirements, protect downstream equipment, and for reuse. Cyclonic separators are then used to extract the remaining catalyst fines. The solid particles settle down at the bottom of the separator, where their level can be controlled by radiometric level systems. The fines are removed when the catalyst level exceeds 70% and the valve is closed again when the level drops below 10%. It is important that there is always catalyst in the bottom part, serving as a plug...
Open the catalog to page 3All Berthold Technologies Process Control catalogs and technical brochures
-
Density measurement
5 Pages
-
Continuous level measurement
5 Pages
-
Retrofit
3 Pages
-
Moisture in pasta production
3 Pages
-
Glass level measurement
3 Pages
-
Mould level measurement
4 Pages
-
LB 475 Fracturing system
3 Pages
-
Multiphase level measurement
7 Pages
-
Produkt InlineSENS
4 Pages
-
Industry Sugar
9 Pages
-
LB472 Bulk Flow Meter
12 Pages
-
MEVIS
4 Pages
-
NUMo - LB 134 UMo II
2 Pages
-
Radiation Protection Instruments
12 Pages
-
Micro-Polar
16 Pages
-
DuoSeries Detectors LB 4700
2 Pages
-
Rod Source Shielding
4 Pages
-
Safety Source Capsule SSC
2 Pages
-
Level Switch LB 471
6 Pages