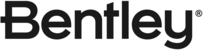

Catalog excerpts
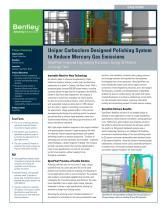
CASE STUDY Bentley Advancing Infrastructure Project Summary Organization: Unipar Carbocloro Solution: Manufacturing Location: Cubatao, Sao Paulo, Brazil Project Objectives • Optimize internal engineering processes using limited resources to better meet growing project demands. • Design polishing system to increase efficiency and further reduce mercury gas emissions to well below current international standards. • Demonstrate commitment to quality, environmental sustainability, safety, and security. Products Used OpenPlant Unipar Carbocloro Designed Polishing System to Reduce Mercury Gas Emissions OpenPlant Improved Engineering Processes, Saving 33 Percent in Design Time Fast Facts • The re-use of existing data and processes preserved Unipar's investment in legacy systems. • The flexibility and versatility of OpenPlant enabled the team to customize the application for 31 pipe specifications. • The team created 3D models to streamline the review process for improved information mobility. ROI • Using OpenPlant allowed Unipar to develop its engineering solution internally, eliminating the significant costs of hiring an outside consultant. • Bentley's flexible, interoperable software saved 33 percent in design time, enabling the team to complete the project ahead of the tight deadline. • Using the software to automate the material lists based on model specifications saved time and eliminated errors from otherwise manual production. Inevitable Need for New Technology An industry leader in chemical manufacturing, Unipar Carbocloro produces chlorine, caustic soda, and derivative compounds at its plant in Cubatao, Sao Paulo, Brazil. With a processing plant covering 650,000 square meters, including a private natural heritage reserve recognized by the Wildlife Center of Sao Paulo State Department, the company is committed to world-class standards not only for quality, but also for environmental protection, safety, and security, with sustainable initiatives dating back to 1985. Aligned with its vision to support surrounding communities and the environment, Unipar initiated a BRL 1 million project encompassing the design of a polishing system for exhaust gas emitted from a mercury vapor abatement tower that would increase efficiency and reduce gas emissions to well below international standards. With tight project deadlines imposed on this project combined with growing project demand, Unipar recognized the need for improved internal engineering processes and updated technology systems to optimize productivity. "Evolution of technology was not only necessary, but inevitable," explained Carlos Rodrigues, a project engineer at Unipar. The company wanted a versatile solution that could be implemented to meet its own specifications, not only for this project but for future projects, without needing to hire third-party consultants. OpenPlant Provides a Flexible Solution A Bentley software user for more than 22 years, Unipar wanted to keep its current data and files on the same platform and therefore faced the challenge of integrating its current applications within a new environment. The company also needed a customizable capability that could be used intelligently for 31 exclusive piping specifications. The team chose OpenPlant, and in eight months Unipar internally developed its library of pipe specifications, piloting the software to design the polishing system. Delivering the polishing system included installation of structures to be interlinked to the mercury abatement tower platform, skid installation, hydraulic seals, piping, pressure, and drainage networks and required that the equipment be integrated into current processes. Using OpenPlant, the team modeled the system amid serious space and time constraints, limited engineering resources, and a lean budget. The flexibility, versatility, and interoperability of OpenPlant enabled the team to combine former 2D models with newly created 3D elements to produce a collaborative virtual model for more accurate clash analysis, improving information mobility and streamlining reviews for better decision making. Versatility Delivers Benefits OpenPlants flexibility and ease of use enabled Unipar to develop its own application to meet its unique engineering specifications without external consultants, saving significant costs. Furthermore, given Unipar's lean employee structure, the ability to administer and maintain the software without the need for a 100-percent dedicated resource was a distinct advantage. Working in an intelligent 3D modeling environment accelerated design of the new polishing system by 33 percent and project deliverables were produced ahead of the required deadline. Using the software improved project collaboration, enhanced review cycles, automated production of material lists, and ensured company standards were consistently applied throughout the entire project.
Open the catalog to page 1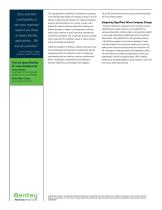
"Easy operation and flexibility of use were important reasons we chose to deploy Bentley applications...We are very satisfied." - Carlos Rodrigues, Project Engineer, Unipar Carbocloro Find out about Bentley at: www.bentley.com Contact Bentley 1-800-BENTLEY (1-800-236-8539) Outside the US +1 610-458-5000 Global Office Listings www.bentley.com/contact The interoperability of OpenPlant facilitated the integration of the specified pipe design with already existing 2D and 3D elements, optimizing clash analysis for improved modeling accuracy and eliminating errors. Having a visual, multifaceted...
Open the catalog to page 2All Bentley Systems Europe B.V. catalogs and technical brochures
-
Digital Airport Project Showcase
18 Pages
-
Water_Hazelwood_Coal_Mine
2 Pages
-
Water_Simtejo_case_study
2 Pages
-
Wimbledon Stadium_Case Study
2 Pages
-
WSP-Shard_Case_Study
3 Pages
-
Bentley’s Water Project Showcase
92 Pages
-
Mine Water Software Solution
4 Pages
-
AutoPLANT Equipment V8i
2 Pages
-
AutoPLANT Piping V8i
2 Pages
-
ConstructSim
2 Pages
-
promis•e
2 Pages
-
Bentley Datasheets
2 Pages
-
Making PDS Interoperable
17 Pages
-
Bentley OpenPlant PowerPID
2 Pages
-
STAAD.Pro
2 Pages
Archived catalogs
-
Water modelling
24 Pages
-
Bentley Water V8 XM
2 Pages
-
Bentley Cadastre Specsheet
2 Pages
-
STAAD Foundation
2 Pages
-
RAM CADStudio
2 Pages
-
Bentley MAP
2 Pages
-
Bentley Structural Brochure
2 Pages
-
Bentley Project Yearbook 2006
82 Pages
-
Bentley SewerCAD
2 Pages
-
Bentley WaterCAD
2 Pages
-
Bentley WaterGEMS
2 Pages
-
Bentley HAMMER
2 Pages
-
Bentley StormCAD
2 Pages
-
Bentley SewerGEMS
2 Pages
-
Bentley AutoPlant P&ID
2 Pages
-
Bentley Microstation
2 Pages
-
Bentley Architecture
2 Pages
-
Bentley ProjectWise brochure
2 Pages
-
Bentley CivilStorm
2 Pages
-
Bentley ProjectWise
4 Pages
-
Bentley PowerDraft
2 Pages
-
Bentley AutoPipe Specsheet
2 Pages