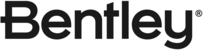

Catalog excerpts
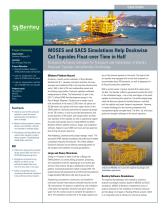
CASE STUDY Project Summary Organization: Dockwise Shipping B.V. Location: Bay of Bengal, Myanmar Project Objective: • Detailed installation design of SHWE platform jacket and topsides. • Load-out, transportation, and launch of 22,000-metric-ton jacket. • Load-out, transportation, and floatover of 30,000-metric-ton topsides. Products used: MicroStation MOSES ProjectWise SACS Fast Facts • Dockwise was the T&I contractor selected to install the recordbreaking jacket and topsides in terms of weight. • Bentley’s offshore platform analysis, design, and installation software was selected for detailed design. • MicroStation and ProjectWise were used by team members in project offices located in The Netherlands, United States, and China. ROI • Efficiencies achieved during detail design saved 5,000 man-hours of the 30,000 engineering hours. • Simulations conducted using MOSES and SACS cut the estimated topsides float-over time from four days to two days. • Safety considerations during simulations allowed the installation to be performed without incident. MOSES and SACS Simulations Help Dockwise Cut Topsides Float-over Time in Half Dockwise Achieves Schedule for Transport and Installation of World’s Heaviest Topsides Using Bentley Technology Offshore Platform Record Dockwise, a wholly owned subsidiary of Royal Boskalis Westminster N.V., develops innovative solutions for heavy transport and installation (T&I) in the maritime infrastructure sector. With a fleet of 23 semi-submersible vessels and two floating super pallets, Dockwise operates worldwide headquartered in Breda, The Netherlands. As part of the USD 1.5 billion SHWE field development project in the Bay of Bengal, Myanmar, Dockwise set a weight record with installation of the nearly 22,000-metric ton jacket and 30,000-metric ton topsides with deck support frame for the SHWE platform. Dockwise performed the engineering design for the T&I contract, as well as provided transportation and launch operation of the jacket, and transportation and floatover operation of the topsides, as well as operational support for jacket and topsides load-out. Using MOSES and SACS, Bentley’s offshore platform analysis, design, and installation software, helped to save 5,000 man-hours and two operation days during the project execution. one of the heaviest topsides in the world. The state-of-theart topsides was equipped with a hotel and restaurant to accommodate about 200 personnel, as well as apparatus for drilling and production capabilities. With a vertical center of gravity located 48.3 meters above the keel, the topsides’ stability requirements pushed the limits of the installation barge – one of only two barges in the world capable of performing this operation. The bottle-shaped barge made the float-over operation feasible because it satisfied both the stability and jacket footprint requirements. However, it created challenges for the mooring arrangement and transportation global strength needs. The short, fat, and heavy jacket also brought challenges to the launch operation. Alex Rodenburg, Dockwise senior project manager, noted: “The successful SHWE topsides installation and jacket launch marked a significant milestone for Dockwise. This further validates Dockwise’s evolution into an offshore contracting partner for the transport and installation of oil and gas platforms.” Large and Heavy Structures Sitting in 110 meters of water in the Bay of Bengal, the SHWE platform is a central drilling, production, processing, and compression facility for exporting gas to an onshore gas terminal. Once onshore, the gas is distributed to the buyer’s pipeline. Commercial production started in August 2013. The project became fully operational by mid 2014 with the production of approximately 500 million cubic feet of gas per day. Engineering, procurement, construction, and installation contractor Hyundai Heavy Industry selected Dockwise as the T&I subcontractor for operation, engineering, and installation of the jacket and topsides. Dockwise was given about 2.5 years from the contract award to complete the operation in 2012. The installation involved one of the largest jackets and SACS and MOSES were used for engineering design and installation operations. Bentley Software Simulations The engineering challenges were tackled by numerous analyses and design iterations based on MOSES and SACS simulations. MOSES is Bentley’s comprehensive suite of analysis software for the installation of offshore structures and the design of all types of floating offshore systems. SACS is an integrated suite of software for structural analysis
Open the catalog to page 1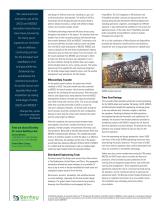
“Our advanced and innovative use of the SACS and MOSES simulation tools that we have been pioneering for many years supports our evolution into an offshore contracting partner for the transport and installation of oil and gas platforms. Dockwise has established the standard procedure for jacket launch and topsides float-over installation by taking advantage of using SACS and MOSES.” – Wenjie Wu, senior structure engineer, Dockwise Find out about Bentley at: www.bentley.com Contact Bentley 1-800-BENTLEY (1-800-236-8539) Outside the US +1 610-458-5000 Global Office Listings...
Open the catalog to page 2All Bentley Systems Europe B.V. catalogs and technical brochures
-
Digital Airport Project Showcase
18 Pages
-
Water_Hazelwood_Coal_Mine
2 Pages
-
Water_Simtejo_case_study
2 Pages
-
Wimbledon Stadium_Case Study
2 Pages
-
WSP-Shard_Case_Study
3 Pages
-
Bentley’s Water Project Showcase
92 Pages
-
Mine Water Software Solution
4 Pages
-
AutoPLANT Equipment V8i
2 Pages
-
AutoPLANT Piping V8i
2 Pages
-
ConstructSim
2 Pages
-
promis•e
2 Pages
-
Bentley Datasheets
2 Pages
-
Making PDS Interoperable
17 Pages
-
Bentley OpenPlant PowerPID
2 Pages
-
STAAD.Pro
2 Pages
Archived catalogs
-
Water modelling
24 Pages
-
Bentley Water V8 XM
2 Pages
-
Bentley Cadastre Specsheet
2 Pages
-
STAAD Foundation
2 Pages
-
RAM CADStudio
2 Pages
-
Bentley MAP
2 Pages
-
Bentley Structural Brochure
2 Pages
-
Bentley Project Yearbook 2006
82 Pages
-
Bentley SewerCAD
2 Pages
-
Bentley WaterCAD
2 Pages
-
Bentley WaterGEMS
2 Pages
-
Bentley HAMMER
2 Pages
-
Bentley StormCAD
2 Pages
-
Bentley SewerGEMS
2 Pages
-
Bentley AutoPlant P&ID
2 Pages
-
Bentley Microstation
2 Pages
-
Bentley Architecture
2 Pages
-
Bentley ProjectWise brochure
2 Pages
-
Bentley CivilStorm
2 Pages
-
Bentley ProjectWise
4 Pages
-
Bentley PowerDraft
2 Pages
-
Bentley AutoPipe Specsheet
2 Pages