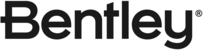

GEA Uses Bentley Technology to Deliver Innovative Milk Processing Plants for Leading Dairy Manufacturer
1 /
2Pages
Catalog excerpts
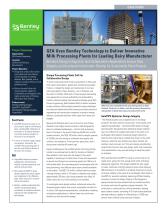
Advancing Infrastructure Project Summary Organization: GEA Process Engineering Location: Lichfield and Pahiatua, New Zealand Project Objective: • Design and construct the world's joint-largest and most efficient milk drying plant in Lichfield, Waikato, New Zealand, with a capacity to produce 30 tons of milk powder per hour. • Deliver the world's first milk processing plant capable of withstanding an earthquake in the highly seismic area of Pahiatua, Wairarapa, New Zealand. Products used: AECOsim Building Designer, AutoPIPE®, AutoPLANT®, MicroStation®, Bentley Navigator, ProjectWise® GEA Uses Bentley Technology to Deliver Innovative Milk Processing Plants for Leading Dairy Manufacturer Bentley's Design Integration and Collaboration Applications Ensure Data Integrity and Accelerate Information Sharing for Sustainable Plant Projects Fast Facts • AutoPIPE allowed the team to create a seismic loop for the Pahiatua plant, enabling 900 millimeters of movement in all lateral directions to provide structural integrity in the event of an earthquake. • In terms of material usage, energy consumption, and waste, the Lichfield milk processing plant is now the most efficient facility of its kind in the industry. ROI ProjectWise helped to enhance collaboration and information mobility, improve productivity, and optimize time and costs. GEA utilized AutoPIPE to prove design integrity and ensure regulatory compliance for the Pahiatua plant, which was built in a seismi-cally active location. Bentley i-models accelerated data transfer and enhanced design coordination to streamline decision making and meet deadlines for both projects. Unique Processing Plants Call For Collaborative Design To meet continued growth of dairy consumption in China and other export destinations, global dairy manufacturing leader, Fonterra, initiated the design and construction of two new milk drying plants in New Zealand—one in Pahiatua, and the other in Lichfield. With each of these projects demanding new approaches to ensure profitability and sustainability, Fonterra retained leading international technology group GEA Process Engineering, New Zealand (GEA) to deliver complete turnkey solutions. Both projects presented unique challenges and required collaborative efforts among consulting structural engineering and construction companies to produce energy-efficient, sustainable facilities within tight time frames and budgets. Because the Pahiatua plant was to be built in one of New Zealand's most highly seismic locations, GEA designed the plant to withstand earthquakes—the first milk processing plant of this kind in the world. Producing 55,000 tons of milk powder annually, this NZD 100 million facility weighs upwards of 20,000 tons with concrete, reinforced steel panels and columns, and includes a 15-ton-per-hour spray dryer, and a drying tower standing 40 meters high. Equally challenging is the Lichfield whole milk drying facility, similar to one already built by GEA for Fonterra in Darfield, New Zealand, which was then the largest in the world. Capable of producing 4.4 million liters of raw milk (equivalent to almost two Olympic-size swimming pools) into 700 tons of milk powder daily, this processing plant was designed with the best performing, most efficient spray dryer currently available on the market. The NZD 120 million Lichfield facility includes a drying chamber, which is 18 meters in diameter and weighs approximately 200 tons, that during assembly was lifted 34 meters above the roof of the building to be installed. To investigate novel design methods, collaborate among the dispersed project teams, and ensure sustainable solutions for its client, GEA required comprehensive, collaborative modeling and analysis applications to deliver these two world-class facilities on time and within budget. With two new unparalleled milk processing plants in New Zealand, Fonterra can better meet the growing demands for milk powder in South East Asia and around the world. AutoPIPE Optimizes Design Integrity "The [Pahiatua] plant was straightforward in its design except for the base isolation construction, which posed some engineering challenges," commented GEA project manager Gary Reynolds. Recognizing that traditional design methods were not sufficient to support high loads in the event of an earthquake, GEA explored innovative design methods to build the first seismic base isolated dryer tower in the world. However, while the main building was base isolated, the ancillary structures were not. This extra design consideration coupled with the short two-year design, build, and commission time necessitated a very accurate design to keep the project on schedule. GEA used Bentleys AutoPIPE to create a seismic loop on all supply lines, giving the lines enough slack while still being adequately supported. This design enabled the safe supply of water, chemicals, and high-pressure steam while allowing 900 millimeters of movement in all lateral directions to ensure structural stability in the event of an earthquake. GEA relied on AutoPIPE for accurate modeling, examining different loading scenarios to prove the design integrity of the dangerous piping between the base isolated and non-isolated auxiliary structures and meet all regulatory design standards. The entire plant is constructed on a friction pendulum-bearing base isolation system, consisting of 50 triple action pendulum bearings making it capable of withstanding a 1/2500-year seismic event without losing structural integrity.
Open the catalog to page 1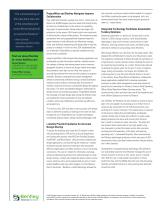
“The commissioning of this new plant was one of the smoothest and most efficient [projects] on record at Fonterra.” — Robert Spurway, Chief Operating Officer Global Operations, Fonterra Find out about Bentley at: www.bentley.com Contact Bentley 1-800-BENTLEY (1-800-236-8539) Outside the US +1 610-458-5000 Global Office Listings www.bentley.com/contact ProjectWise and Bentley Navigator Improve Collaboration Over 3,000 staff members worked more than 1 million hours to deliver the 30,000 kilogram-per-hour whole milk drying facility at Fonterra’s Lichfield plant. In the interest of completing...
Open the catalog to page 2All Bentley Systems Europe B.V. catalogs and technical brochures
-
Digital Airport Project Showcase
18 Pages
-
Water_Hazelwood_Coal_Mine
2 Pages
-
Water_Simtejo_case_study
2 Pages
-
Wimbledon Stadium_Case Study
2 Pages
-
WSP-Shard_Case_Study
3 Pages
-
Bentley’s Water Project Showcase
92 Pages
-
Mine Water Software Solution
4 Pages
-
AutoPLANT Equipment V8i
2 Pages
-
AutoPLANT Piping V8i
2 Pages
-
ConstructSim
2 Pages
-
promis•e
2 Pages
-
Bentley Datasheets
2 Pages
-
Making PDS Interoperable
17 Pages
-
Bentley OpenPlant PowerPID
2 Pages
-
STAAD.Pro
2 Pages
Archived catalogs
-
Water modelling
24 Pages
-
Bentley Water V8 XM
2 Pages
-
Bentley Cadastre Specsheet
2 Pages
-
STAAD Foundation
2 Pages
-
RAM CADStudio
2 Pages
-
Bentley MAP
2 Pages
-
Bentley Structural Brochure
2 Pages
-
Bentley Project Yearbook 2006
82 Pages
-
Bentley SewerCAD
2 Pages
-
Bentley WaterCAD
2 Pages
-
Bentley WaterGEMS
2 Pages
-
Bentley HAMMER
2 Pages
-
Bentley StormCAD
2 Pages
-
Bentley SewerGEMS
2 Pages
-
Bentley AutoPlant P&ID
2 Pages
-
Bentley Microstation
2 Pages
-
Bentley Architecture
2 Pages
-
Bentley ProjectWise brochure
2 Pages
-
Bentley CivilStorm
2 Pages
-
Bentley ProjectWise
4 Pages
-
Bentley PowerDraft
2 Pages
-
Bentley AutoPipe Specsheet
2 Pages