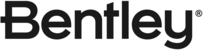

CADDS Group Optimizes Safety of Iron Ore Facilities with Innovative Guarding System Design
1 /
2Pages
Catalog excerpts
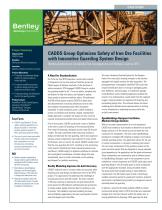
< r/jamm'Y / Bentley* Advancing Infrastructure ^ Project Summary Organization CADDS Group Solution Mining and Offshore Engineering Location Dampier, Western Australia, Australia Project Objectives • To develop a standardized design solution to increase safety at mining facilities. • To improve workflow processes to optimize design accuracy and production and reduce costs. • To decrease design and fabrication time for the guarding system. Products Used AssetWise® ALIM, ContextCapture, Descartes, MicroStation®, OpenBuildings™ Designer, ProSteel, ProStructures CADDS Group Optimizes Safety of Iron Ore Facilities with Innovative Guarding System Design Bentley Applications Accelerate Site Investigations and Reduce Costs by 30% Fast Facts • CADDS used Bentley's 3D and reality modeling applications to design and pilot its innovative, modular guarding system for RTIO, optimizing worksite safety. • The use of point clouds and reality meshes enhanced investigation and visualization of on-site infrastructure, facilitating accurate representation of the as-built environment. ROI Bentley's digital, standardized design solution saved CADDS an estimated AUD 24 million across all RTIO mining sites. MicroStation, OpenBuildings Designer, and ContextCapture helped achieve a 10% reduction in design and fabrication costs. Altering the designs within the 3D model space saved 12 weeks otherwise associated with on-site installation modifications. A Need for Standardization Rio Tinto Iron Ore (RTIO) operates a world-class network of integrated iron ore mine and port facilities across the Pilbara region of Western Australia. At the forefront of safety innovation, RTIO engaged CADDS Group to conduct site guarding audits for all 17 iron ore plants, complete site verification for high risk assets, and replace or update those assets to optimize workforce safety. The estimated AUD 80 million project required CADDS to obtain data and documentation of existing infrastructure at all sites and complete the guarding work within the plants' scheduled 12-week shutdown cycles. CADDS needed to review its workflows and develop a digital, standardized design approach to complete the project on time since the network comprised brownfield sites with dated infrastructure. Prior to this project, CADDS would send a team of drafters to the site to create 2D drawings of the existing facilities. From these 2D drawings, designers would create 3D as-built models. The team used these often-inaccurate models to design and fabricate the new guarding, which was expensive because unique components were required for every install. Furthermore, once on site for the install, CADDS usually found that the new guarding did not fit, resulting in time-consuming, costly rework. Realizing that these manual processes were insufficient, CADDS sought to digitalize workflows to optimize site investigation and develop a modular design that was standardized, easy to install, eliminated on-site welding, and allowed for condition monitoring. Reality Modeling Improves As-built Accuracy CADDS' objective was to increase safety and accuracy while reducing costs and design and fabrication time for the RTIO project. The organization first addressed the challenge of creating accurate as-built 3D models. The team invested in 3D laser scanning to capture the site and imported the point clouds into MicroStation and Descartes for processing to create usable, digital reference files for existing on-site structures. This capability improved modeling accuracy, and with Bentley applications the team could quickly transfer even the largest point cloud files. The team introduced ContextCapture for the Dampier, Parker Point site audit, sending surveyors to the location equipped with digital cameras for data acquisition. The photogrammetric investigation identified 700 issues that required rectification due to missing or damaged guards, poor deflection, excessive gaps, or insufficient signage. Using Bentley's reality modeling application enabled the creation of a multiresolution reality mesh from the captured images, reducing reliance on expensive 3D scanning and accelerating design time. The software allows for easier modeling and a detailed visual representation of existing on-site infrastructure, optimizing accuracy within the as-built environment. OpenBuildings Designer Facilitates Modular Design Solution With an accurate representation of on-site equipment, CADDS had reliable as-built models to determine an optimal design solution to fit the infrastructure and meet the time constraints for installation. The team used OpenBuildings Designer for intelligent 3D modeling to design its innovative, modular guarding system. The application allows for the use of custom components in a dynamic modeling environment. The two major components of the guarding system are the posts and mesh panels that are designed in varying standard sizes depending on the application and the plant environment. These components are connected by pins at different points. In OpenBuildings Designer, each of the components can be modeled as a smart component and CADDS could adjust each guarding design in the 3D model space to verify compliance with the appropriate standard. Using simulated models, the team performed strength testing to meet deflection requirements. The 3D models were critical in identifying suitable connection points for guard post locations, potential clash points, and determining proximity to dangerous areas to optimally place the guarding. In addition, using the 3D model enabled CADDS to clearly communicate design intent to RTIO and make any requested changes from the client directly within the model, prior to issuing prefabrication drawings. RTIO approved the final
Open the catalog to page 1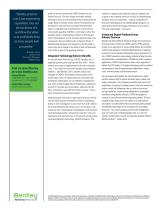
“Bentley products aren’t just engineering capabilities, they are the backbone of a workflow that allow us to confidently keep as many people safe as possible.” – Brendan Jarvis, Systems and Processes Manager, CADDS Group Find out about Bentley at: www.bentley.com Contact Bentley 1-800-BENTLEY (1-800-236-8539) Outside the US +1 610-458-5000 Global Office Listings www.bentley.com/contact model of the new system and CADDS piloted it at the Parker Point site. The new design eliminates welding, allowing for easy on-site assembly while reducing material usage. Being a modular system where all...
Open the catalog to page 2All Bentley Systems Europe B.V. catalogs and technical brochures
-
Digital Airport Project Showcase
18 Pages
-
Water_Hazelwood_Coal_Mine
2 Pages
-
Water_Simtejo_case_study
2 Pages
-
Wimbledon Stadium_Case Study
2 Pages
-
WSP-Shard_Case_Study
3 Pages
-
Bentley’s Water Project Showcase
92 Pages
-
Mine Water Software Solution
4 Pages
-
AutoPLANT Equipment V8i
2 Pages
-
AutoPLANT Piping V8i
2 Pages
-
ConstructSim
2 Pages
-
promis•e
2 Pages
-
Bentley Datasheets
2 Pages
-
Making PDS Interoperable
17 Pages
-
Bentley OpenPlant PowerPID
2 Pages
-
STAAD.Pro
2 Pages
Archived catalogs
-
Water modelling
24 Pages
-
Bentley Water V8 XM
2 Pages
-
Bentley Cadastre Specsheet
2 Pages
-
STAAD Foundation
2 Pages
-
RAM CADStudio
2 Pages
-
Bentley MAP
2 Pages
-
Bentley Structural Brochure
2 Pages
-
Bentley Project Yearbook 2006
82 Pages
-
Bentley SewerCAD
2 Pages
-
Bentley WaterCAD
2 Pages
-
Bentley WaterGEMS
2 Pages
-
Bentley HAMMER
2 Pages
-
Bentley StormCAD
2 Pages
-
Bentley SewerGEMS
2 Pages
-
Bentley AutoPlant P&ID
2 Pages
-
Bentley Microstation
2 Pages
-
Bentley Architecture
2 Pages
-
Bentley ProjectWise brochure
2 Pages
-
Bentley CivilStorm
2 Pages
-
Bentley ProjectWise
4 Pages
-
Bentley PowerDraft
2 Pages
-
Bentley AutoPipe Specsheet
2 Pages