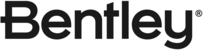

ArcelorMittal Burns Harbor Operation Uses AssetWise Performance Management to Achieve USD 2.1 Million in Savings in One Year
1 /
4Pages
Catalog excerpts
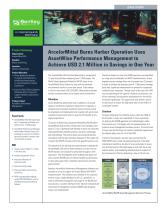
CASE STUDY Project Summary Organization: ArcelorMittal USA Solution: Metals and Mining Location: Indiana, United States Project Objective: • Senior leadership directive to develop and implement a reliability business process to reap the benefits of capital expenditure. • Launch a World Class Equipment Reliability effort to drive and support reliability improvement activities. Products Used: AssetWise Performance Management Fast Facts • ArcelorMittal Flat Roll Operations has 12 operating facilitates and employs over 17,000 people. • AssetWise Performance Management Health Indicator Panel consolidates all sources of condition data and provides a central view of the health of assets. ROI • Saved a total of USD 2.1 million in the first year. • Avoided equipment failure. • Improved efficiency of corrective work. • Lowered energy usage. • Improved safety and working conditions. • RCM recommended redesign saved USD 200,000 per year by avoiding unnecessary bearing failures. ArcelorMittal Burns Harbor Operation Uses Bentley InRoads AssetWise Performance Management to Powerful tools for the design of civil infrastructure Achieve USD 2.1 Million in Savings in One Year ® The ArcelorMittal USA Flat Roll Operations is comprised of 12 operating facilities employing over 17,000 people. The World Class Equipment Reliability (WCER) team at the ArcelorMittal Burns Harbor hot strip mill has achieved very dramatic results in a one-year period. Total savings in the first year were USD 2,076,900. Other positive benefits include increased safety and a cleaner work environment. Situation Senior leadership determined that in addition to investing capital in production equipment replacement or upgrade, a complete and consistent reliability business process would be developed and implemented and coupled with world-class reliability practices and tools to reap the full benefits of any capital expenditure. To launch its World Class Equipment Reliability (WCER) effort, ArcelorMittal USA formed a central team with members from each U.S. site. It partnered with Bentley to learn and utilize the renowned Bentley reliability process, practices, technology, and methodology. This central team was trained by Bentley consultants and the team members deployed to their plant site to launch the WCER initiative within the specific business unit. The objective of the training and coaching was to prepare the ArcelorMittal USA central team members to be the internal WCER trainers and coaches for personnel throughout their operations. This development effort enabled each plant site with a central WCER team of internal reliability practitioners to drive and support their reliability improvement activities going forward. Bentley’s AssetWise Performance Management software was selected as a tool to support the ArcelorMittal USA WCER implementation. The software was installed on its corporate servers using a single database for all U.S. operations. In order to effectively manage the full scope of the WCER business process, a custom interface to the Tabware computerized maintenance management system (CMMS) was designed, tested, and implemented. The Burns Harbor hot strip mill (HSM) operation was identified as a high priority candidate for WCER implementation. It was experiencing an average delay rate of greater than 22 percent. In order to achieve the business plan of 17.58 percent average delay rate, significant improvements in production equipment reliability were necessary. Through much of the year, the HSM was not operating at full capacity. However, as economic conditions improved, the production requirements for the facility increased significantly. This opportunity was another reason to take action to reduce the high delay rate for the HSM in a sustainable manner. Solution To begin addressing the reliability issues within the HSM at Burns Harbor, a team was assembled to focus exclusively on applying the WCER approach and methodologies within this business unit. This began with the implementation of a proactive asset management business process. The initial area of focus was the finishing mill, which consistently experienced the highest delay rates for all of the HSM. Critical to the program’s success was ensuring that the HSM WCER team, which represented 6 percent of the total maintenance workforce, be able to focus exclusively on proactive activities and not be pulled away to deal with day-to-day reactive duties. Area leadership demonstrated its support of the improvement effort by dedicating a total of 10 full-time PLAN Align Reliability Strategy with Business Goals Work Identification Identify Physical Assets Contributing to Goals Continuous Improvement Loop CONTROL Work Planning Work Scheduling Sustained Maintenance Loop Prioritize Assets by Consequence/ Relative Risk Establish Targeted Performance Requirements Performance Analysis Work Execution ArcelorMittal WCER Asset Management Business Process
Open the catalog to page 1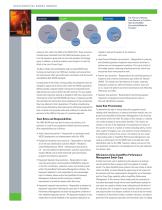
ARCELORMITTAL BURNS HARBOR Current State The Process of Moving From Reactive to Proactive – How ArcelorMittal Successfully Made the Transition Desired State Proactive Proactive resources from within the HSM to the WCER effort. These resources included seven individuals from the HSM maintenance group, one from the operations group and two from the operations technology group. In addition, an external resource was brought in to lead the effort in the role of Asset Coach. The Burns Harbor Central Reliability Team provided WCER skills training and coaching to the HSM team members and ensured...
Open the catalog to page 2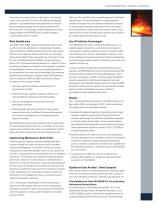
ARCELORMITTAL BURNS HARBOR them active to ensure that they do in fact apply in the operating context of the new asset. The use of this software functionality allowed for rapid implementation and deployment of technically based maintenance programs for the like type systems within the finishing mill. Their strategy to employ templates and analysis copying enabled the HSM WCER team to rapidly implement 11,236 indicators within 12 months. With use of the AssetWise Performance Management Asset Health Indicator Panel, the team was enabled to manage equipment problems by exception since the...
Open the catalog to page 3All Bentley Systems Europe B.V. catalogs and technical brochures
-
Digital Airport Project Showcase
18 Pages
-
Water_Hazelwood_Coal_Mine
2 Pages
-
Water_Simtejo_case_study
2 Pages
-
Wimbledon Stadium_Case Study
2 Pages
-
WSP-Shard_Case_Study
3 Pages
-
Bentley’s Water Project Showcase
92 Pages
-
Mine Water Software Solution
4 Pages
-
AutoPLANT Equipment V8i
2 Pages
-
AutoPLANT Piping V8i
2 Pages
-
ConstructSim
2 Pages
-
promis•e
2 Pages
-
Bentley Datasheets
2 Pages
-
Making PDS Interoperable
17 Pages
-
Bentley OpenPlant PowerPID
2 Pages
-
STAAD.Pro
2 Pages
Archived catalogs
-
Water modelling
24 Pages
-
Bentley Water V8 XM
2 Pages
-
Bentley Cadastre Specsheet
2 Pages
-
STAAD Foundation
2 Pages
-
RAM CADStudio
2 Pages
-
Bentley MAP
2 Pages
-
Bentley Structural Brochure
2 Pages
-
Bentley Project Yearbook 2006
82 Pages
-
Bentley SewerCAD
2 Pages
-
Bentley WaterCAD
2 Pages
-
Bentley WaterGEMS
2 Pages
-
Bentley HAMMER
2 Pages
-
Bentley StormCAD
2 Pages
-
Bentley SewerGEMS
2 Pages
-
Bentley AutoPlant P&ID
2 Pages
-
Bentley Microstation
2 Pages
-
Bentley Architecture
2 Pages
-
Bentley ProjectWise brochure
2 Pages
-
Bentley CivilStorm
2 Pages
-
Bentley ProjectWise
4 Pages
-
Bentley PowerDraft
2 Pages
-
Bentley AutoPipe Specsheet
2 Pages