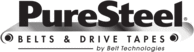
Group: Belt Technologies Inc

Catalog excerpts
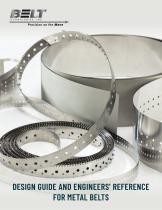
DESIGN GUIDE AND ENGINEERS’ REFERENCE FOR METAL BELTS
Open the catalog to page 1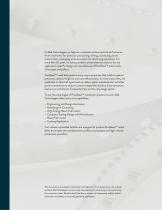
At Belt Technologies, we help our customers achieve optimal performance from machinery for precision positioning, timing, conveying, power transmission, packaging and automated manufacturing operations. For more than 50 years, we have provided a comprehensive resource for the application-specific design and manufacture of PureSteel™ metal belts, drive tapes and pulleys. PureSteel™ metal belts possess many unique properties that result in superior precision, control, longevity and cost effectiveness. In many cases, they are preferable to other belt types (such as rubber, plastic and...
Open the catalog to page 2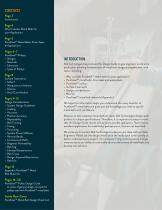
CONTENTS Page 3 Introduction Page 4 Why Consider Metal Belts for your Application Page 5 PureSteel™ Metal Belts, Drive Tapes & Applications Pages 6-7 PureSteel™ Pulleys • Designs • Materials • Tolerances • Types of Pulleys Page 8 Surface Treatments • Teflon® • Neoprene or Urethane • Silicone • Hard Coat Anodize Pages 9-15 Design Considerations • System Design Guidelines • Loading • Accuracy • Position Accuracy • Repeatability • Belt Tracking • Timing • Tensioning • System Frame Stiffness • Reverse Bends • Cantilevered Shafts • Magnetic Permeability • Belt Sag • Elevated Temperatures • Belt...
Open the catalog to page 4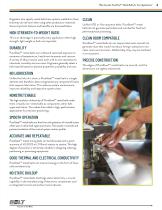
Engineers who specify metal belts have options available to them that they do not have when using other products or materials. Some important features and benefits are discussed below. HIGH STRENGTH-TO-WEIGHT RATIO This is an advantage in practically every application where high strength, light weight or both are important. DURABILITY PureSteel™ metal belts can withstand sustained exposure to extremes of temperature, hostile environments and vacuum. A variety of alloys may be used, each with its own resistance to chemicals, humidity and corrosion. Engineers generally select a belt material...
Open the catalog to page 5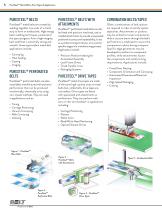
5 PureSteel™ Metal Belts, Drive Tapes & Applications PureSteel™ metal belts are created by welding together two ends of a metal strip to form an endless belt. High energy beam welding techniques, pioneered in the space program, form a high integrity butt weld that is extremely strong and smooth. Some typical plain metal belt applications include: • Conveying • Heat Sealing • Casting • Imaging PURESTEEL™ PERFORATED BELTS PureSteel™ perforated belts are plain metal belts manufactured with precision perforations that can be produced mechanically, chemically or by using non-impact methods. They...
Open the catalog to page 6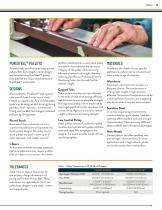
PURESTEELTM PULLEYS All metal belts and drive tapes travel around pulleys. Belt Technologies custom designs and manufactures PureSteel™ pulleys that optimize the unique characteristics of PureSteelTM metal belts. DESIGNS Most pulleys for PureSteelTM belt systems take one of three forms: round stock, I-beam or capped tube. Any of these pulley types may be designed with drive lug timing pockets, relief channels, conventional timing teeth or Belt Technologies’ patented ball bearing timing teeth. Round Stock Because of their relatively low cost, round stock pulleys are incorporated into most...
Open the catalog to page 7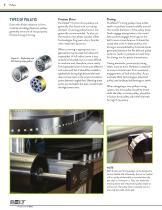
TYPES OF PULLEYS Even with all the variations in form, material and design features, pulleys generally serve one of two purposes: friction driving or timing. Figure 6 – Perforated and ball bearing tape pulleys Friction Drive PureSteelTM friction drive pulleys are generally flat faced with no timing element. Crowning pulley faces is not generally recommended. To discuss the reasons why, please contact a Belt Technologies Engineer who is familiar with metal belt dynamics. When crowning is appropriate, two geometries may be used: full radius and trapezoidal. A full radius crown is less...
Open the catalog to page 8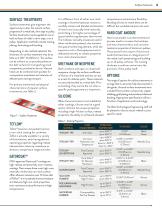
SURFACE TREATMENTS Surface treatments give engineers the opportunity to alter the natural surface properties of a metal belt, drive tape or pulley. Surface treatments may be applied to one or both surfaces of a belt or drive tape, or to a pulley. Application methods include coating, plating, laminating and bonding. Depending on the method selected, the thickness of a surface treatment may be as little as 0.001” (0.025mm). The surface can be uniform or, to provide pockets on the belt surface for transporting small components, punched or die cut. Vacuum holes can be combined with pockets for...
Open the catalog to page 9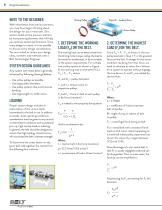
NOTE TO THE DESIGNER With information from previous sections, you may have begun thinking about the design for your metal belt. This section builds on the previous sections by incorporating elements that will help you optimize system performance. Since every design is unique, it is not possible to discuss every design consideration. You are invited to review your design ideas, numbers and methods with a Belt Technologies Engineer. SYSTEM DESIGN GUIDELINES Any system with metal belts is generally enhanced by following these guidelines: • Use as few pulleys as possible. • Use large pulley...
Open the catalog to page 10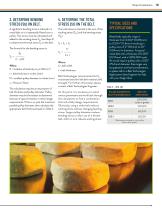
3. DETERMINE BENDING STRESS (Sb) ON BELT. A significant bending stress is induced in a metal belt as it is repeatedly flexed over a pulley. This stress must be calculated and added to the working stress SW (see Step 4) to determine the total stress St on the belt. The formula for the bending stress is: Where: E = modulus of elasticity in psi (N/mm2) t = belt thickness in inches (mm) D = smallest pulley diameter in inches (mm) u = Poisson’s Ratio This calculation requires an assumption of belt thickness and pulley diameter. Pulley diameter may be the easiest to determine because of space...
Open the catalog to page 11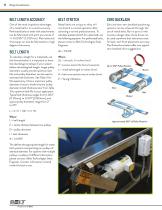
ZERO BACKLASH BELT LENGTH ACCURACY BELT STRETCH One of the most important advantages of a metal belt is its overall accuracy. Perforated belts or belts with attachments can be fabricated with pitch accuracies of +/-0.0005” (0.0127mm). Plain belts and drive tapes can also be fabricated to a high degree of accuracy. BELT LENGTH To calculate a length for a metal belt, use the formula below. It is important to know the ideal design envelope of your system before calculating belt length. Larger pulley diameters usually provide optimum belt life, and pulley diameters can be used to estimate belt...
Open the catalog to page 12Archived catalogs
-
Design and Applications Guide
25 Pages