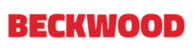

Catalog excerpts
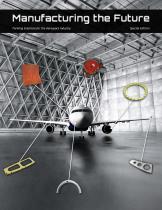
Manufacturing the Future Forming Solutions for the Aerospace Industry Special Edition
Open the catalog to page 1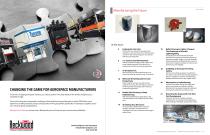
CHANGING THE GAME FOR AEROSPACE MANUFACTURERS In the ever-changing aerospace industry, you need a partner who stays ahead of the trends and gives you a competitive edge. From hot forming and compression molding to sheet hydroforming and beyond, no other OEM offers more experience building hydraulic presses and specialty forming equipment specifically for aerospace suppliers across such a diverse group of applications. #BringUsYourChallenge and see how a Beckwood press will improve your process and profitability. beckwoodpress.com/aerospace info@beckwoodpress.com 636.343.4100 Manufacturing...
Open the catalog to page 2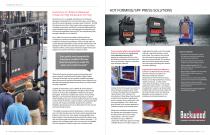
Ducommun Inc. Relies on Beckwood Presses for High Temperature Forming Ducommun, Inc. is a leading manufacturer of contoured aerospace components for commercial, business, and military aircraft as well as helicopters and space launch vehicles. To fulfill their diverse part orders, they employ many unique processes including compression molding for composite lightweighting, sheet hydroforming for low volume/high mix production and hot forming/superplastic forming (SPF) for manipulating high-strength materials such as titanium. Since 2006, Ducommun has relied on Beckwood Press Company to...
Open the catalog to page 3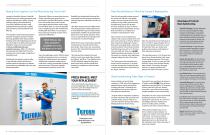
21st Century Tool DevelopmentBoeing Parts Supplier Cuts Tool Manufacturing Time in HalfPiper Aircraft Relies on Triform for Control & Repeatability Located in Steelville, Missouri, Steelville Manufacturing is a leading aerospace parts supplier specializing in milling, turning, waterjet cutting, and metal forming. Since1959, Steelville has been using traditional forming methods to supply parts for Boeing, Lockheed Martin and Sikorsky. They needed a modern forming solution powerful enough to provide net shape forming capability while reducing handfinishing work and facilitating quick die...
Open the catalog to page 4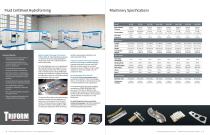
Features & Benefits • High-performance sheet metal and composite forming capability • Increased forming capacity via a universal bladder can form multiple parts in a single cycle • Dramatically lower tooling costs through elimination of mated dies • Minimized reliance on skilled labor through an intuitive, programmable control system with built-in recipe handling • Compact, flush-floor designs eliminate the need for pits or special foundations • Even application of pressure outperforms traditional rubber pad forming • Fast, inexpensive bladder changes for increased up-time • Reduced...
Open the catalog to page 5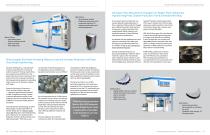
Rubber Pad Forming vs Deep Draw Hydroforming With Triform • No annealing needed • Production costs down 25% • Scrap rates less than 1% • Improved weld quality and overall appearance Airbus Supplier Eliminates Annealing, Reduces Costs and Increases Production with Deep Draw Sheet Hydroforming Aerospace Parts Manufacturer Changes from Rubber Pad to Deep Draw Hydroforming Press, Slashes Production Time & Eliminates Wrinkling An aerospace parts manufacturer was using a hydraulic rubber pad press to form a majority of their products. Flanged parts suffered from high scrap rates due to...
Open the catalog to page 6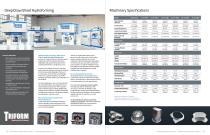
Machinery Specifications Features & Benefits • High-performance drawing capability for a variety of materials including the strongest alloys • Easily configured to operate in fluid cell mode for increased forming flexibility • Dramatically lower tooling costs through elimination of mated dies • Minimized reliance on skilled labor through an intuitive, programmable control system with built-in recipe handling • Simplified part development with the "In-Sight" feature • Fast, inexpensive bladder changes for increased up-time • Reduced unplanned downtime with simple preventive maintenance...
Open the catalog to page 7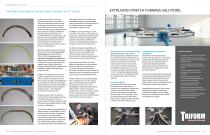
Stretching Your Resources Fall of the Artisan Operator: Extrusion Stretch Forming in the 21st Century A global manufacturer of aircraft structures and airframe assemblies was using antiquated stretch forming equipment to manufacture extrusion parts. While they were able to satisfy demand, producing parts that fell within their customers' quality specifications (Boeing, Northrup Grumman and Lockheed Martin) was challenging. The lack of process repeatability with their manually-operated extrusion stretch forming machines created certain process deficiencies, including a heavy reliance on...
Open the catalog to page 8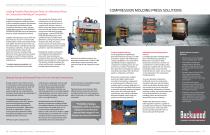
Build it Stronger, Lighter, Cheaper: The Challenges of Aircraft Lightweighting Leading Propeller Manufacturer Relies on a Beckwood Press for Compression Molding of Composites COMPRESSION MOLDING PRESS SOLUTIONS Boeing Chooses a Beckwood Press to Form Laminate Components A leading manufacturer of propellers needed a compression molding solution to form composite aerospace components. They partnered with Beckwood Press Company to develop a custom 100-ton heated platen press that could maximize productivity and offer precise temperature, pressure, speed, and positional control. Capable of...
Open the catalog to page 9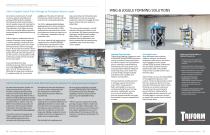
Outfitting an Aerospace Forming Facility Triform Supplies Seven Press Package to Aerospace Industry Leader An American manufacturer of aircraft structures, airframe assemblies, and aerospace MRO needed a complete forming solution that would minimize sub-tier supplier issues and maximize the organization’s manufacturing flexibility. They ultimately chose Triform because of the firm’s unrivaled ability to provide a diverse package of sophisticated forming equipment. Triform engineers collaborated with the customer to develop a fully-integrated 7-machine package consisting of three sheet...
Open the catalog to page 10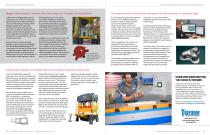
Alternatives to Sheet Hydroforming Removing the Guesswork from New Part Development Meggitt Safety Systems’ Hydraulic Deep Draw Press is a “Complete Forming Solution” Forming Simulation Software Gives Aerospace Parts Manufacturer a Competitive Edge California-based Meggitt Safety Systems manufactures fire protection equipment, safety apparatus, and other heat related sensors for the aerospace industry. While Meggitt’s product lines continually advanced, their aging hydraulic press from 1963 was stuck in a bygone era. They needed a modern forming solution that was more energy-efficient,...
Open the catalog to page 11All Beckwood Press catalogs and technical brochures
-
Benchtop Presses - DJ Series
2 Pages
-
About Beckwood
7 Pages
-
100 Ton Punching Press
1 Pages
-
150 Ton C - Frame Press
1 Pages
-
350 Ton Draw Press
1 Pages
-
200 Ton C - Frame Press
1 Pages
-
550 Ton Pre - Form Press
1 Pages
-
75 Ton C - Frame Press
1 Pages
-
300 Ton Track Pin Press
1 Pages
-
360 Ton 4 - Post Press
1 Pages
-
1,000 Ton 10 - Post Press
1 Pages
-
1,000 Ton 4 - Post Press
1 Pages
Archived catalogs
-
1200 Ton 4 - Post Press
1 Pages