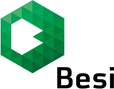
Catalog excerpts
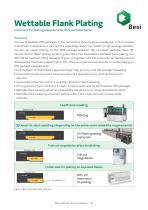
Wettable Flank Plating Immersion tin plating equipment for QFN wettable flanks Summary The use of leadless QFN packages in the automotive industry grows rapidly due to the increase in electronic components in cars and the expanding electric car market. A high package reliability requires tin solder plating on the QFN package sidewall, the so-called wettable flank. BE Semiconductor (Besi) plating product group Meco has developed a wettable flank plating line (WFL20) for lead-less (QFN) packages (Figure 1). Together with the immersion tin plating process developed by chemicals supplier Sytron this offers a unique total solution for tin solder plating on QFN package sidewalls with: • A throughput of 20 standard singulation tape-rings per hour with full package traceability. • Lower total production costs, because a second singulation cut or etching step are not required. • Lower total production costs by omitting optional tin electroplating. • A fine-grained 2-3 µm immersion tin layer on bare copper and tin electroplated QFN packages. • Wettable flank passing industrial solderability standards for IC component lead durability. • Wettable flanks allowing automatic optical solder fillet inspection and increase solder reliability. Leadframe molding Molding Optional tin electroplating (depending on the solder joint reliability requirements) Sn Electroplating (optional) Full cut singulation after tin plating Full cut Singulation Immersion tin plating on exposed flanks Figure 1. Besi wettable flank solution Meco Wettable flank whitep
Open the catalog to page 1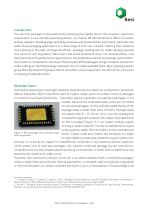
Introduction The use of IC packages in the automotive industry grows rapidly due to the increase in electronic components in cars and the expanding electric car market. BE Semiconductors (Besi) is a worldleading supplier of leading edge assembly processes and equipment for lead-frame, substrate and wafer level packaging applications in a wide range of end-user markets. Starting from selective silver plating of die pads, through die attach, package molding and tin solder plating towards trim and form and singulation, Besi covers the entire production chain. For miniaturization, cost...
Open the catalog to page 2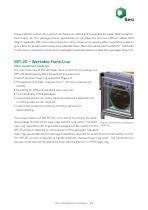
these methods is that only a part of the flank is tin plated and is available for solder fillet formation. Particularly, for thin packages these approaches do not allow the minimum 100 μm solder fillet height needed for AOI in the mass production. Only immersion tin plating after singulation is able to give a fully tin plated and thereby fully wettable flank. Meco has developed the WFL20 – Wettable Flank Line for industrial immersion tin plating for wettable flanks on lead-less packages (Figure 1). WFL20 – Wettable Flank Line Main equipment features The main features of the wettable flank...
Open the catalog to page 3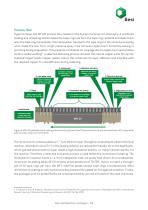
Process flow Figure 4 shows the WFL20 process flow, based on the Sytron immersion tin chemistry. A combined loading and unloading station takes the tape rings are from the tape ring cassette and loads them onto the tape ring manipulator. The manipulator transports the tape rings to the various processing units inside the line. First, a high pressure spray rinse removes copper burrs formed by sawing or punching during singulation. This prevents incomplete tin coverage due to copper burrs and enables uniform solder wetting3. A selective descaling process removes the natural copper oxide film...
Open the catalog to page 4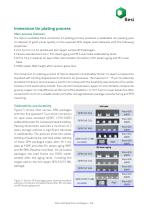
Immersion tin plating process Main process features The Sytron wettable flank immersion tin plating process produces a solderable non peeling pure tin deposit of good visual quality on the exposed QFN copper lead sidewalls with the following properties: • 2 to 3 μm tin on tin plated and full copper surface QFN packages. • Passes standard zero hour, 8 h steam aging and 16 h oven bake solderability tests. • 0.5 to 1.5 μm residual tin layer after intermetallic formation in 8 h steam aging and 16 h oven bake. • 100% solder fillet height after ceramic glass test. The immersion tin plating...
Open the catalog to page 5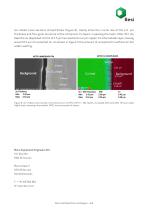
Ion-milled cross-sections of lead flanks (Figure 6), clearly show the crucial role of the 2-3 μm thickness and fine-grain structure of the immersion tin layers in passing the tests. After 16 h dry bake the as-deposited tin film of 2.5 μm has reacted to a 2 μm copper-tin intermetallic layer, leaving around 0.5 μm of unreacted tin. As shown in Figure 5 this amount of unreacted tin suffices for full solder wetting. Figure 6: Ion-milled cross-section of immersion tin on QFN 4.5X7.5 – 48L flanks, as-plated (left) and after 16 hours bake (right) tests showing intermetallic (IMC) and unreacted tin...
Open the catalog to page 6All BE Semiconductor Industries N.V. catalogs and technical brochures
-
9800 TC next
2 Pages
-
Chemical deflashing
2 Pages
-
Esec 2100 hSix
2 Pages
-
Fico MMS-X
2 Pages
-
Fico AMS-X
2 Pages
-
Fico AMS-W
2 Pages
-
Datacon 8800 CHAMEOadvanced
2 Pages
-
Datacon 8800 TC advanced
2 Pages
-
Esec 2100 hSi / sDadvancedi
2 Pages
-
Datacon 2200 evo advanced
2 Pages
-
INVESTOR PRESENTATION
52 Pages
-
Fico AMS-W Top Foil
2 Pages
-
Fico MMS-LM Top Foil
2 Pages
-
Esec 2100 FC hS
2 Pages
-
Esec 2009 fSE
2 Pages
-
Esec 2009 SSIE
2 Pages
-
Esec DB 2100 DS
2 Pages
-
Esec 2100 sDadvanced
2 Pages
-
Datacon 2200 evo hS
2 Pages
-
Datacon 2200 evoplus
2 Pages
-
Esec 2100 hS
2 Pages
-
Fico Compact Line - X
2 Pages
-
Fico AMS-LM Top Foil
2 Pages
-
Esec 2100 sDplus
2 Pages
-
Esec 2100 xPplus
2 Pages
-
Meco EDL/EPL
2 Pages
-
Fico Filter Line
2 Pages
-
Fico Sawing Line
2 Pages
-
Fico MMS-LM
2 Pages
-
Fico AMS-LM
2 Pages
-
DB 2100 Z Pattern
4 Pages
-
Datacon DS9000e
2 Pages
-
Fico Compact Line
2 Pages
-
Esec DB 2009 SSIE
2 Pages
-
Meco EDF/EPL
2 Pages
-
Fico AMS-W
2 Pages
-
Esec DB 2009 fSE
2 Pages
-
Esec DB 2100 FC
2 Pages
-
8800 FC QUANTUM
4 Pages
-
2200 evo
4 Pages
-
2200 evoplus
2 Pages
Archived catalogs
-
Fico MMS-LM Top Foil
2 Pages
-
Fico AMS-W Top Foil
2 Pages