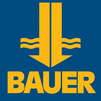
Catalog excerpts
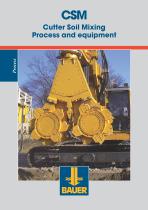
Cutter Soil Mixing Process and equipment
Open the catalog to page 1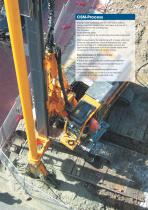
CSM-Process Mixing of self-hardening slurries with native soils by using a modified trench cutter technique is a new and effective method for constructing: Cut-off walls; earth retaining walls; soil improvement or for constructing foundation elements. CSM is used mainly for stabilizing soft or loose soils (non cohesive and cohesive), however the machinery used, derived from Bauer’s cutter technology, extends the applicability of the method to much harder strata when compared to other methods of soil mixing. Main advantages of the method are: • High productivity • The in-situ soil is used as...
Open the catalog to page 2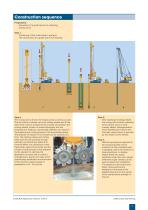
Construction sequence Preparation: Excavation of a guide trench for collecting surplus slurry Step 1: Positioning of the cutter head in wall axis. The construction of a guide wall is not required. Step 2: The mixing tool is driven into the ground at a continuous rate. The soil matrix is broken up by the cutting wheels and at the same time a fluid is pumped to the nozzles, set between the cutting wheels, where it is mixed thoroughly with the loosened soil. Adding a compressed airstream can improve the breaking and mixing process in the downstroke phase. The direction of rotation of the...
Open the catalog to page 3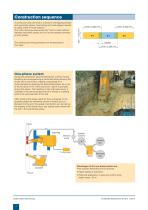
Construction sequence The cutting and mixing procedure can be executed in two ways: A continuous wall is formed in a series of overlapping primary and secondary panels. Overcutting into fresh adjacent panels is called „fresh-in-fresh method“. The cutter technique also allows the “hard-in-hard method”, whereby secondary panels are cut into the already hardened primary panels. One-phase system During the penetration (downstroke) phase, cutting, mixing, fluidifying and homogenising is performed while pumping the binder slurry into the soil. Adding compressed air is recommended for assisting...
Open the catalog to page 4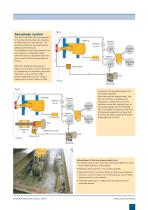
Two-phase system The soil is fluidified and homogenised in the downstroke phase by pumping of bentonite slurry into the soil. The mixing process can be supported by adding compressed air. The backflow of soil and bentonite can be pumped to a desanding plant where the sand is separated from the slurry which is then pumped back to the rig. CSM-rig Deliverypump Agitator Cement Cement Silo Agitator Bentonite Mixer When the backflow becomes too heavy for pumping, it can be removed by a backhoe or a scratching belt from the trench onto a screen where primary separation occurs. Using a hose pump...
Open the catalog to page 5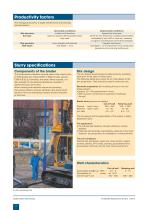
Productivity factors The average productivity is highly influenced by the following site parameters. Soil structure Soil type favourable conditions uniform soil structure loose to medium dense gravelly sand, silty sand Site geometry Wall depth long, straight wall sections wall depth > 10 m unfavourable conditions layered soil structure dense to very dense soil, cobbles and boulders embedded in soil, stiff or hard soil, cohesive or organic soil (reduction of the final strength) irregular wall layout wall depth < 10 m (influence of non-productive periods such as moving, setting-up) Slurry...
Open the catalog to page 6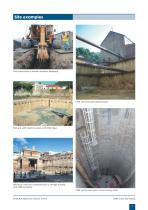
Site examples Wall construction in limited conditions (Malaysia) CSM-wall with props (Netherlands) Wall and uplift retention panels with CSM (Italy) Retaining a wall and underpinning for a heritage building with CSM (Australia) CSM-wall for start shaft microtunneling (USA) © BAUER Maschinen GmbH, 1/2014 CSM Cutter Soil Mixing
Open the catalog to page 7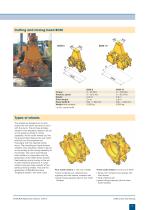
Cutting and mixing head BCM Torque Rotation speed Height Panel length Panel width B Weight (with wheels) * Types of wheels The wheels are designed to cut and loosen the soil matrix and then to mix it with the slurry. The soil type dictates whether more emphasis needs to be put on the wheel´s cutting or mixing capability. As the cutter wheels cut into the ground they break up the soil matrix and then mix the loosened soil thoroughly with the injected binder slurry. The prevailing soil type dictates whether more emphasis needs to be put on the cutting or the mixing capability of the wheels....
Open the catalog to page 9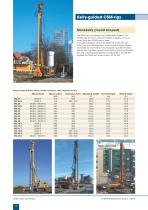
Kelly-guided CSM-rigs Monokelly (round shaped) The BCM unit is supported by a Monokelly system. For smaller rigs and for a maximum depth of approx. 20 m, a round Kelly bar (Ø 368 mm) is used. Two guide sledges connect the Kelly bar to the drill rig’s mast, they provide alignment, crowd and extraction forces and rotational movement. A hydraulically operated locking mechanism transfers crowd and extraction forces to the Kelly bar and a rotating arrangement incorporated in the guides enables the CSM unit to be turned +45° to -90°. Round shaped Kelly without Kelly extension, with rotation...
Open the catalog to page 10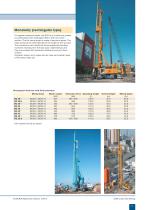
Monokelly (rectangular type) For greater treatment depth, the BCM unit is held and guided by a Monokelly with rectangular (600 x 340 mm) crosssection. The full string length is made of sectional pipes. The Kelly string can be extended above the height of the rig mast. The connectors can transfer all forces (especially bending moments resulting from the load case “assembling”) and they are covered with protection shields to ensure a flush surface. Hydraulic hoses, slurry pipes and air hose are located inside of the hollow kelly bar. Rectangular Kelly bar with Kelly extension Mixing head BG...
Open the catalog to page 11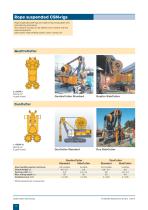
Rope suspended CSM-rigs Rope suspended CSM rigs are made for big mixing depth with minimized rig dimensions. The machine concept can be offered in four variants with the base components: base carrier, hose handling system, boom, mixing unit. 2 x BCM 5 Mixing unit (4 gear boxes) QuattroCutter Standard Quattro SideCutter DuoCutter Standard 1 x BCM 10 Mixing unit (2 gear boxes) QuattroCutter Standard SideCutter Hose handling system and boom Overall height (m) Working width (m) * Max. mixing depth (m) Installed power (kW) DuoCutter Standard SideCutter * Width perpendicular to panel axis CSM...
Open the catalog to page 12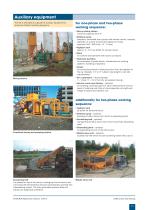
Auxiliary equipment The list is intended as a guide for auxiliary equipment to ensure an efficient working sequence. For one-phase and two-phase working sequence: • Slurry mixing station minimum capacity 20 m3/h • Delivery pump frequency controlled slurry pump with remote control, capacity depends on volume of panel and speed of mixing. (typically: 200 – 600 l/min, 12 – 15 bar) • Agitator tank approx. 3 – 5 m3 (as buffer for cement slurry) • Silos for cement and bentonite with screw conveyors • Hydraulic backhoe for excavation of guide trench, maintenance of working platform, handling of...
Open the catalog to page 13All BAUER Maschinen GmbH catalogs and technical brochures
-
brochure BAUER
20 Pages
-
BAUER Dynamic Compaction
4 Pages
-
Ground Improvement
16 Pages
-
SMW Soil Mixing Wall – System
12 Pages
-
SMW Soil Mixing Wall ? System
12 Pages
-
VDW Double Head Drilling System
12 Pages
-
MC 64 Foundation crane
14 Pages
-
MC 96 Foundation crane
14 Pages
-
MC 128 Foundation crane
10 Pages
-
BD 50 Decanter
8 Pages
-
Well Drilling Unit
4 Pages
-
Ground Improvement
16 Pages
-
TBA 300 Deep Drilling Unit
8 Pages
-
TBA 200 Deep Drilling Unit
8 Pages
-
Exploration and Mining Equipment
12 Pages
-
MC Foundation Cranes
12 Pages
-
TR Depth Vibrators
4 Pages
-
BC 32 Trench Cutter
6 Pages
-
BG 36 H Rotary Drilling Rig
12 Pages
-
BG 20 H Rotary Drilling Rig
12 Pages
-
BG 12 H Rotary Drilling Rig
12 Pages