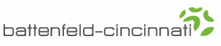
Catalog excerpts
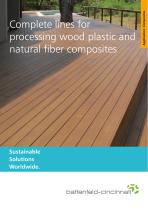
Page 1 – © Battenfeld-Cincinnati 2019 – Applications: Complete lines for composite processing Application: Composites Complete lines for processing wood plastic and natural fiber composit
Open the catalog to page 1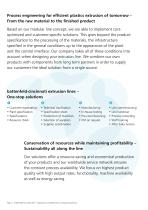
Process engineering for efficient plastics extrusion of tomorrow – From the raw material to the finished product Based on our modular line concept, we are able to implement costoptimized and customer-specific solutions. This goes beyond the product specification to the processing of the materials, the infrastructure specified in the general conditions up to the appearance of the plant and the control interface. Our company takes all of these conditions into account when designing your extrusion line. We combine our own products with components from long term partners in order to supply our...
Open the catalog to page 2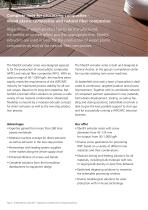
Complete lines for processing composites – Wood plastic composites and natural fiber composites Regardless of which product has to be manufactured, battenfeld-cincinnati offers you the appropriate line. fiberEX extruders are used in lines for the production of wood plastic composites as well as for natural fiber composites. The fiberEX extruder series was designed especially for the production of wood plastic composites (WPC) and natural fiber composites (NFC). With an output range of 30-1,000 kg/h, the machine series exactly meets the requirements of the WPC/NFC industry for maximized...
Open the catalog to page 3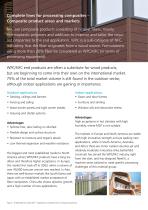
Complete lines for processing composites – Composite product areas and markets NFC are composite products consisting of natural fibers, mainly thermoplastic polymers and additives to improve and tailor the required properties to the end application. WPC is a sub-category of NFC, indicating that the fiber originates from a wood source. Formulations using more than 20% fiber be considered as WPC/NFC (in terms of processing equipment). WPC/NFC end products are often a substitute for wood products, but are beginning to come into their own on the international market. 75% of the total market...
Open the catalog to page 4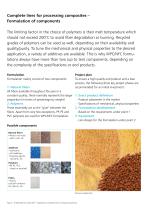
Complete lines for processing composites – Formulation of components The limiting factor in the choice of polymers is their melt temperature which should not exceed 200°C to avoid fiber degradation or burning. Recycled grades of polymers can be used as well, depending on their availability and quality/purity. To tune the mechanical and physical properties to the desired application, a variety of additives are available. This is why WPC/NFC formulations always have more than two (up to ten) components, depending on the complexity of the specifications or end products. Formulation Formulation...
Open the catalog to page 5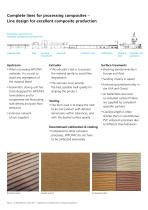
Complete lines for processing composites – Line design for excellent composite production Schematic overview of a standard composite extrusion line Tipping table Surface treatment Upstream • hen conveying WPC/NFC W materials, it is crucial to avoid any segregation of the material blend • ravimetric dosing unit has G to be designed for WPC/NFC formulations and to compensate the fluctuating bulk density and poor flow behaviors • xtensive network E of sub-suppliers Cooling tanks Shaping tool Extruder incl. upstream Extruder • he extruder’s task is to process T the material gently to avoid...
Open the catalog to page 6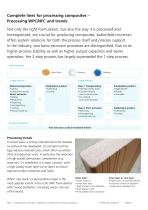
Complete lines for processing composites – Processing WPC/NFC and trends Not only the right formulation, but also the way it is processed and homogenized, are crucial for producing composites. battenfeld-cincinnati offers system solutions for both the process itself and process support. In the industry, two basic extrusion processes are distinguished. Due to its higher process stability as well as higher output capacities and easier operation, the 2-step process has largely superseded the 1-step process. Raw materials Polymers Wood fibers 1-Step Process Material preparation • rying D •...
Open the catalog to page 7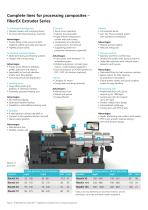
Complete lines for processing composites – fiberEX Extruder Series 1a Horizontal dosing unit • aterial hopper with emptying device M • C drive with fixed frequency converter A Advantages: • recise filling of the screws for WPC, P dryblend, pellets, granulate and regrind • ighest process safety H 1b Vertical crammer feeder • ptimized dosing and feeding solution O • opper with stirring wings H Advantages: • recise screw filling for dryblend, P pellets, granulate and regrind • pplicable for low bulk densities A and/or poor flow abilities • or broad particle size distribution F 4 Control • ouch...
Open the catalog to page 8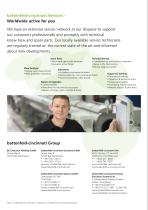
battenfeld-cincinnati Services – Worldwide active for you We have an extensive service network at our disposal to support our customers professionally and promptly with technical know-how and spare parts. Our locally available service technicians are regularly trained on the current state of the art and informed about new developments. Spare Parts • ailor-made spare parts packages T • nnovative screw design I Wear Analysis • egular wear measurement R • ear protection consulting W Technical Service • ommissioning, maintenance, inspection C • epair-in-the-field-Hotline R • emote diagnosis...
Open the catalog to page 9All Battenfeld-cincinnati USA catalogs and technical brochures
-
PVC Pelletizing Extruders
9 Pages
-
Application: irrigation
6 Pages
-
application profile EN
4 Pages
-
Global extrusion solutions EN
12 Pages