
Group: Balluff

Catalog excerpts
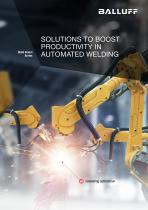
Weld Select Series SOLUTIONS TO BOOST PRODUCTIVITY IN AUTOMATED WELDING
Open the catalog to page 1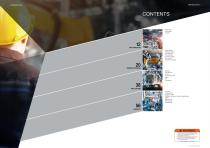
Weld Select Series | 3 2 | Weld Select Series CONTENTS Philosophy Technology Actions BEST PRACTICES Weld Spatter Physical Impact Nut Detection Photoelectric Cylinder Position Connectivity Inductive Coupling COMMON PROBLEMS Sensing Connectivity Joining I/O Architectures Vision IIoT Traceability Inductive Photoelectric Magnetic Field Machine Vision and Optical Identification Safety Networking Connectivity Accessories
Open the catalog to page 2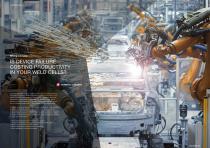
4 | Weld Select Series Weld Select Series | 5 Welding Automation IS DEVICE FAILURE COSTING PRODUCTIVITY IN YOUR WELD CELLS? The Weld Select Series is an industry proven group of Balluff products designed for use in the most inhospitable welding environments. Poor sensor selection costs welders in every industry increased downtime, unnecessary maintenance, delayed delivery, and lost profits. Balluff presents a complete package of welding solutions that extends sensor life and increases productivity in the harshest welding environments. This guide contains two sections. The front section is...
Open the catalog to page 3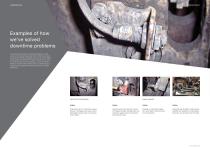
6 | Weld Select Series Weld Select Series | 7 Examples of how we’ve solved downtime problems The standard expectation in automated welding is a high volume of component replacement and maintenance, repair and operations (MRO). Damaged sensors and burned cables cause unplanned downtime and reduced production, driving up overtime wage costs and creating a crunch on delivery timelines. We work with manufacturers on problem areas to develop the best application specific solutions to increase productivity. UNPROTECTED SENSORS CABLE DAMAGE Unprotected and non-bunkered sensors, sensors in...
Open the catalog to page 4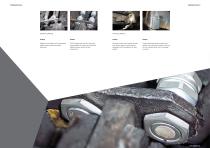
8 | Weld Select Series Weld Select Series | 9 SPATTER DAMAGE PHYSICAL IMPACT Spatter accumulation and unprotected pigtail sensors cause excessive downtime. PTFE coated prox mounts, protective tubing sealed with wrap, and sacrificial cables improve sensor life and productivity. Physical contact from loading of parts can quickly destroy a basic sensor, especially with the presence of weld spatter. Coated steel face sensors resist weld spatter and mechanical impact, and they can be brushed clean with no damage or issues.
Open the catalog to page 5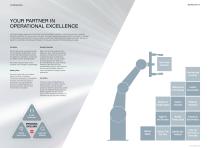
Weld Select Series | 11 10 | Weld Select Series YOUR PARTNER IN OPERATIONAL EXCELLENCE Automated welding requires robust solutions since most standard automation components and basic assembly practices typically do not hold up well in weld cells. To achieve operational excellence Balluff has worked for decades on best practices and solutions to improve uptime and eliminate nuisance stops from failed automation. We use our passion for automation and lasting technology for continuous improvement to help achieve your goals. Boosting Productivity We will improve the competitive position of our...
Open the catalog to page 6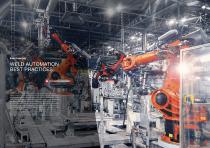
12 | Weld Select Series Weld Select Series | 13 Boost Productivity WELD AUTOMATION BEST PRACTICES A review of our partnerships over the decades shows the teams who have boosted productivity the best have taken a multi-angle approach to improving and implementing sensing and automation applications. Using best practices in sensing philosophy, we work together toward application specificity: selecting the right sensor, cable and protection for each situation, then learning and duplicating from that experience. Technology best practices include utilizing sensor coatings and multi-metal...
Open the catalog to page 7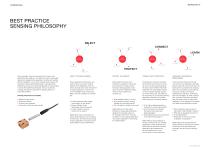
Weld Select Series | 15 14 | Weld Select Series BEST PRACTICE SENSING PHILOSOPHY SELECT CONNECT BEST PRACTICES BEST PRACTICES BEST PRACTICES BEST PRACTICES CONNECT PROTECT When working in harsh environments and in heavy duty applications like welding, it is important to take a multi-angle approach to designing the application. Working with existing sensor installations, you must to consider all the reasons for the sensor’s failure before determining a winning solution. While blind trial and error will eventually lead to improvements in sensor life, Balluff has developed, with our customers,...
Open the catalog to page 8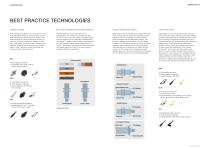
Weld Select Series | 17 16 | Weld Select Series BEST PRACTICE TECHNOLOGIES SENSOR COATINGS MULTI-METAL SENSING AND WELD FIELD IMMUNITY SURVIVE LOADING AND CONTACT CABLE PROTECTION Every application is different, but for sensors to survive in an automated welding environment there are some basic principles that are best practice. Plastic-faced brass housings on inductive sensors fail quickly in a weld cell, so special coatings are available for every type of application. Start with a basic coating as your standard. Where failures and issues occur, invest in better or best coatings to extend...
Open the catalog to page 9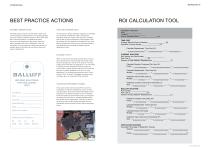
Weld Select Series | 19 18 | Weld Select Series BEST PRACTICE ACTIONS DOCUMENT SENSOR FAILURE AUDIT HIGH DOWNTIME CELLS Throwing sensors away every shift doesn’t have to be normal. Instead of dumping them in the closest garbage can, start a sensor collection system or bin in each work area. Have the operator or maintenance person document what happened to the sensor, where the failure happened and when it happened. Track this information for a few weeks and quickly see where the problem areas of the plant are, and which issues you need to address first. It is important to take a systematic...
Open the catalog to page 10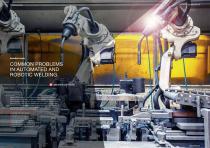
20 | Weld Select Series Weld Select Series | 21 Downtime Issues COMMON PROBLEMS IN AUTOMATED AND ROBOTIC WELDING Keeping a structural or component production line running with high efficiency is a big challenge. Welding throws off debris, spatter and molten metal making the environment dirty and difficult for standard automation products to survive. Operators loading parts hour after hour can impact sensors and cause physical damage to automation devices.In this section we will review the most common problems in automated and robotic welding and suggest solutions to the most common...
Open the catalog to page 11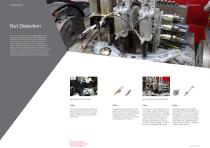
22 | Weld Select Series Weld Select Series | 23 Nut Detection One of the most common and frustrating applications in automated and robotic welding is reliably detecting the presence of a weld nut. There are some solutions and technologies on the market that have varying levels of success. Detection of the weld nut is very application specific: sense it during the load or in a secondary check station? How much space is available for a sensor and connector? Is it sensed from under the part or on top of the part? What is the size or shape of the nut? What are the tolerances? Each type of...
Open the catalog to page 12All Balluff GmbH catalogs and technical brochures
-
PRODUCTS FOR EFFICIENT AUTOMATION 5
656 Pages
-
PRODUCTS FOR EFFICIENT AUTOMATION 4
190 Pages
-
PRODUCTS FOR EFFICIENT AUTOMATION 3
584 Pages
-
PRODUCTS FOR EFFICIENT AUTOMATION 2
444 Pages
-
PRODUCTS FOR EFFICIENT AUTOMATION 1
796 Pages
-
PRODUCTS + NEWS
25 Pages
-
GUIDED CHANGEOVER SOLUTION
3 Pages
-
PRODUCTS FOR THE WASHDOWN AREAS
88 Pages
-
MOBILE EQUIPMENT
21 Pages
-
SOLUTIONS FOR DRIVE TECHNOLOGY
15 Pages
-
TAILOR-MADE QUALITY
5 Pages
-
WE MONITOR YOUR MACHINES
10 Pages
-
PACKAGING, FOOD AND BEVERAGE
76 Pages
-
MANAGING ALL YOUR DATA
6 Pages
-
MAGNETIC FIELD SENSORS
7 Pages
-
Balluff products and services
94 Pages
Archived catalogs
-
BES00PY
2 Pages
-
BES008L
2 Pages
-
BES02NC
2 Pages
-
BES01ZN
2 Pages
-
BES0028
2 Pages
-
BES05F9
2 Pages
-
BES054Z
2 Pages
-
BES0086
2 Pages
-
BES0042
2 Pages
-
BES013N
2 Pages
-
BES00H4
2 Pages
-
BES003P
2 Pages
-
BES00HC
2 Pages
-
BES00CK
2 Pages
-
BES01ZW
2 Pages
-
BES00EF
2 Pages
-
BES00HF
2 Pages
-
BES00P7
2 Pages
-
BES0068
2 Pages
-
BES060T
2 Pages
-
QUALITY DOWN TO THE LAST DETAIL
94 Pages
-
OPENING NEW PERSPECTIVES
13 Pages
-
BALLUFF TEST CAMPUS
15 Pages