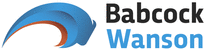

Catalog excerpts
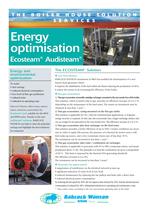
• fuel savings • reduced electrical consumption • low level of flue gas pollutants • reduced noise • reduction in operating costs Babcock Wanson offers many optimi- sation solutions, particularly the Ecosteam® pack, suitable for the BWS Audisteam® software, BABCOCK WANSON can help to value the potential savings and highlight the best solutions Low-NOx burners BABCOCK WANSON investment in R&D has enabled the development of a new burner head geometry which: • improve the distribution of the fuel within the flame reducing the production of NOx ; • reduce the excess of air increasing the efficiency of the boiler. Flue-gas economisers 1/ Flue-gas économiser, removable cartridge exdianger mounted in the rear smoke box oftfie boiler. This solution, which is suited only to gas, provides an efficiency increase of 4 to 5 % depending on the temperature of the feed-water. The return on investment may be obtained in less than 1 year* ; 2/ Flue-gas économiser, casing-mounted on the flue-gas outlet. This solution is applicable for NG / fuel-oil combined-fuel applications, or if greater energy recovery is required. In this case, the économiser has a larger exchange surface and can no longer be incorporated in the rear smoke box. The efficiency increase is 5 to 6 % ; 3/ Flue-gas économiser plus heat exchanger on the feed-water. This solution provides a boiler efficiency of up to 96%. Certain conditions are neces- sary in order to apply this process: the presence of a thermal de-aerator and a cold feed make-up source, and a low condensate return rate of less than 70 %. The investment can be recovered in less than 1 year* ; 4/ Flue-gas économiser, plus water / combustion air exchanger. This solution is applicable to processes with 85 to 90% condensate return, and steam production above 15 t/h. The principle is to heat the combustion air up to a temperature of 80 °C. This limit is imposed by the thermal NOx generating threshold. The investment can be recovered in less than 2 years*. Electronic fan speed control • suppression of interference on the electrical network at start up, • significant reduction of noise level at low load, • reduced maintenance by replacing the fan pulleys and belts with a direct drive • reduced electrical power consumption: by reducing the fan speed by 20%, the air output is also reduced by 20%, but the electrical power consumption is reduced by 50%. Substantial reductions in operating and maintenance costs. * These value varies according to the size and annual operating time of the boiler Babcock Wanson _ CNIM Group _
Open the catalog to page 1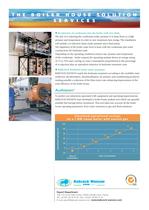
B O I L E R H O U S E S O L U T I O N S E R V I C E S ◆ Re-injection of condensate into the boiler with zero flash The aim of re-injecting the condensate under pressure is to keep them at a high pressure and temperature in order to save maximum heat energy. The installation will include a re-injection drum under pressure and a feed pump. The regulation of the boiler water level is done with the condensate plus water coming from the feedwater tank. Depending on the operating conditions (return rate, pressure and temperature of the condensate - boiler output) the operating analysis shows an...
Open the catalog to page 2All Babcock Wanson catalogs and technical brochures
-
e-Pack
2 Pages
-
VAP PREMIUM
2 Pages
-
VAP RR
2 Pages
-
STEAM SOLUTIONS
12 Pages
-
TPC-B THERMAL FLUID HEATER
2 Pages
-
BWR FIRETUBE STEAM BOILER
2 Pages
-
BWD FIRETUBE STEAM BOILER
2 Pages
-
NBWB FIRETUBE STEAM BOILER
2 Pages
-
The Boiler House Solution
2 Pages
-
WDF Direct Fired Air Heaters
2 Pages
-
Fire tube steam boiler BWR
2 Pages
-
Thermal fluid Heaters TPC
2 Pages
-
Fire Tube Boilers BWD
2 Pages
-
Hot water boilers EPC AC
2 Pages
-
System One
2 Pages
-
Thermal fluid Heaters EPC-H
2 Pages
-
Thermal fluid Heaters TPC LN
2 Pages
-
Thermal fluid Heaters TPC-H
2 Pages
-
EUROSTEAM
2 Pages
-
Process air heaters
2 Pages
-
Air Vein burners
2 Pages
-
Thermal fluid Heaters EPC-ES
2 Pages
-
Hot water boilers HW Pack
4 Pages
-
Fire tube steam boiler BWB
2 Pages
-
Thermal Fluid Heater TPC-LN
2 Pages
-
Thermal Fluid Heater TPC
2 Pages
Archived catalogs
-
Fire-tube Boiler - BWD
2 Pages
-
BW Energy Optimisation
2 Pages
-
Fire-tube Boiler - BWR
2 Pages
-
Fire-tube Boiler - BWB
2 Pages