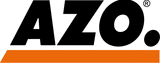

Catalog excerpts
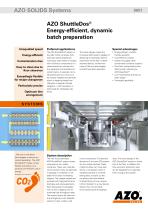
AZO ShuttleDos® Energy-efficient, dynamic batch preparation Unequalled speed Energy-efficient Contamination-free Easy to clean due to floor clearance Exceedingly flexible for recipe changeover Particularly precise Optimum line arrangement Preferred applications The AZO ShuttleDos® system is the right choice wherever fully automatic batch preparation involving a wide variety of recipes with numerous components in a closed system as well as strict line separation and avoidance of contamination is required. Up to 20 batches per hour with up to ten exactly weighed components within a weighing range from 100 gram to several hundred kilograms – AZO innovation is tailor-made for challenges like these. Special advantages The clever design makes the innovative AZO system capable of delivering an exemplary level of automation which has not been achieved before, furthermore many of the key technologies involved have been patented. Energy-efficient, climatefriendly operation Cost-effective solution Greater throughput than conventional container systems Dust-free, contamination-free docking and undocking by AZO CleanDock® Low-maintenance and easy to clean design Universally applicable „We rely on the latest technologies to secure our market leadership. The AZO ShuttleDos® makes us fast, flexible and allows us to produce with efficient use of energy.“ Quotation of a customer System description The new fully automated AZO ShuttleDos® system doses components into mobile containers. These raw materials can be stored in silos, be delivered in big bags or containers or be added from sacks via feeding hoppers. The storage vessels are provided with high-performance discharge and dosing elements. Each dosing point is equipped with its own weighing unit for achieving high throughput rates. The system allows for optimum line arrangement with separate areas for major, medium and minor components. The decisive elements of the new AZO system are the mobile shuttles. These mobile shuttles can move past drums or containers where a weighing process is currently taking place, and pick up the containers that have already finished filling and now require further transport to a new dosing station. This new principle enormously boosts throughput rates. The entire design of the AZO ShuttleDos® system is raised free of the floor. In addition the fully automatic production area can be designed for an operatorfree r
Open the catalog to page 1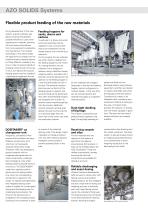
AZO SOLIDS Systems Flexible product feeding of the raw materials During development of this new system, a great emphasis was placed on giving the greatest possible flexibility to users when supplying raw materials, allowing the most economical delivery form to be selected for production and manufacture. The modular technology in this area provides the opportunity to change over the individual product feeding stations by fitting different modules at any time in order to respond rapidly to changing market trends. Of course, if this is not required the product feeding stations can be installed...
Open the catalog to page 2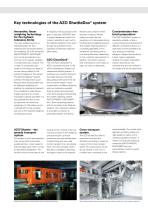
Key technologies of the AZO ShuttleDos® system Innovative, linear weighing technology for the tightest tolerance limits This new weighing system is characterised by its floor clearance and its precise dosing and weighing. 20 to 30 containers (BATCHTAINER®, MIXTAINER® etc.) can be provided per hour, with five to ten exactly weighedin components per container. The number of components per recipe is not limited, but does of course have an effect on the overall throughput of the system. The AZO ShuttleDos® system achieves this high batch count because each dosing station has its dedicated...
Open the catalog to page 3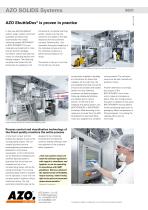
AZO ShuttleDos® is proven in practice In this new AZO ShuttleDos® system, large, medium and small quantities are dosed fully automatically into mobile collecting vessels (MIXTAINER® or BATCHTAINER®). The raw materials are stored both in silos and are fed from big bags, containers, cartons and sacks by means of unloading stations and feeding hoppers. The collecting containers are locked into the dosing line for weighing in the components. An optical scanning system makes sure that the containers are loaded in the right sequence and are positioned correctly. Following this, fully automatic...
Open the catalog to page 4All AZO Group catalogs and technical brochures
-
Conveying unit M235-38
2 Pages
-
UFS 75
2 Pages
-
AZODOS
4 Pages
-
RoLog®
2 Pages
-
DosiBox®
2 Pages
-
AZO BATCHTAINER®
2 Pages
-
AZO liquids
20 Pages
-
Quaiphar
8 Pages
-
BG
6 Pages
-
Azo WMD
2 Pages
-
AZO Dough Lines
2 Pages
-
ShuttleDos
2 Pages
-
ManDos Mobile
2 Pages
-
processing system
2 Pages
-
mixer container
2 Pages
-
ManDos
2 Pages