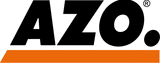

Catalog excerpts
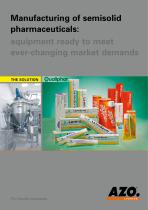
Manufacturing of semisolid pharmaceuticals: equipment ready to meet ever-changing market demands THE SOLUTION
Open the catalog to page 1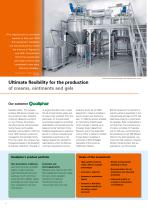
»The requirement for increased capacity is fully met. With this equipment, Qualiphar can now produce four times the amount of Algipan in one shift. Compared to the former equipment: one week's work is now completed in two days, cleaning included.« Johan Janssens, Validation Engineer, Qualiphar Qualiphar-Gifrer. The company employs 430 persons spread over two production sites: Qualiphar in Bornem (Belgium) and Gifrer in Lyon (France). All products manufactured are sold exclusively in pharmacies and hospitals. Qualiphar was founded in 1937 and since 1970 has been owned and managed by the...
Open the catalog to page 2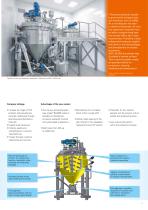
»The pharmaceutical industry is governed by stringent laws and directives, such as GMPs. As a manufacturer we need to abide by these laws. As such, any equipment acquired must be able to support these laws and comply with a set of user requirements. Therefore a close collaboration between supplier and client is vital during design and development of process equipment. AZO LIQUIDS has always kept Qualiphar’s interest at heart. This is why the system meets all specified criteria for production, cleaning, handling and maintenance.« Johan Janssens, Validation Engineer, Qualiphar Flexible...
Open the catalog to page 3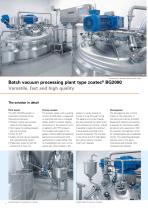
Good access to process vessel and melt vessel Batch vacuum processing plant type zoatec® BG2000 Versatile, fast and high qualityThe solution in detail Plant layout The AZO LIQUIDS system is essentially composed of the following components: • Process module with process vessel and homogeniser • One hopper for adding powders and one for liquids • Pump for CIP • Supply unit with vacuum generator and heating/cooling system • Preparation vessel to melt fat compounds or heat oils Process module The process vessel, with a working volume of 2,000 litres, is supported on load cells and has an...
Open the catalog to page 4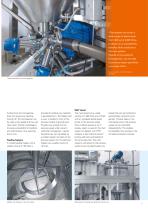
»The system can cover a wide range of batch sizes: from 400 up to 2,000 litres. It allows us to successfully transfer other products to the new system. Thanks to the powerful homogeniser, we are able to produce larger quantities in a single shift.« Johan Janssens, Validation Engineer, Qualiphar Good accessibility to the homogeniser Furthermore the homogeniser does not require any cleaning. During CIP, the homogeniser can be used at any speed and thus will clean itself. Another advantage is the easy accessibility for handling and maintenance, thus reducing down time. Feeding hoppers A mobile...
Open the catalog to page 5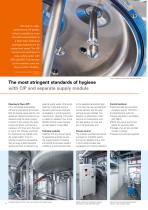
»The built-in, highperformance CIP system makes it possible to clean the plant automatically in a short time. Individual cleaning programs can be created and saved. The CIP functions are optimised in close collaboration with AZO LIQUIDS. This testifies to the excellent customer focus at AZO LIQUIDS.« Johan Janssens, Validation Engineer, Qualiphar Spray nozzles for a powerful Cleaning In Place The most stringent standards of hygiene with CIP and separate supply module Cleaning In Place (CIP) CIP is conducted automatically without any alterations to the plant. Both the process vessel and the...
Open the catalog to page 6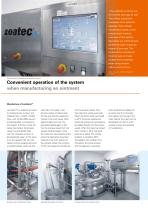
»The zoamatic controls are convenient and easy to use. They allow production processes to be perfectly adjusted. The process visualisation gives a clear, practical and intuitive overview of the system. Operators are informed and guided through recipes by means of prompts. The recipe editor provides an intuitive way to create recipes and to manage them using version history and control.« Johan Janssens, Validation Engineer, Qualiphar Manufacture of Lamiderm®: Lamiderm® is a water/oil emulsion for treating burns, sunburn and reddened skin. A batch of 2,000 litres, with the BG 2000 vacuum...
Open the catalog to page 7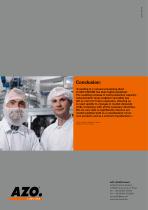
Conclusion: »Investing in a vacuum processing plant of AZO LIQUIDS has been highly beneficial. The resulting increase in total production capacity, reduced batch times andplant versatility has left us room for future expansion, allowing us to react quickly to changes in market demands while complying with all the necessary directives. We are now able to significantly improve our market position both as a manufacturer of our own products and as a contract manufacturer.« Johan Janssens, Validation Engineer, Qualiphar (on left in photo) AZO LIQUIDS GmbH Gottlieb-Daimler-StraRe 4 D-79395...
Open the catalog to page 8All AZO Group catalogs and technical brochures
-
Conveying unit M235-38
2 Pages
-
UFS 75
2 Pages
-
AZODOS
4 Pages
-
ShuttleDos®
4 Pages
-
RoLog®
2 Pages
-
DosiBox®
2 Pages
-
AZO BATCHTAINER®
2 Pages
-
AZO liquids
20 Pages
-
BG
6 Pages
-
Azo WMD
2 Pages
-
AZO Dough Lines
2 Pages
-
ShuttleDos
2 Pages
-
ManDos Mobile
2 Pages
-
processing system
2 Pages
-
mixer container
2 Pages
-
ManDos
2 Pages