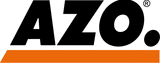

Catalog excerpts
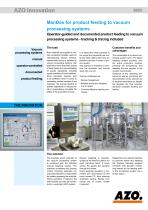
AZO Innovation ManDos for product feeding to vacuum processing systems Operator-guided and documented product feeding to vacuum processing systems - tracking & tracing included Vacuum processing systems manual operator-controlled documented product feeding The task Raw materials are supplied to modern production facilities used for manufacturing sauces, ketchup, mayonnaise, soups or spreads by vacuum processing systems, that generally involve automatic dosing of base liquids and manual feeding of powder ingredients, including squall quantities of liquid additives. Since automatic systems tend to be inefficient when it comes to processing diverse varieties of raw materials, the manual feeding of powder ingredients is indispensable in guaranteeing complete flexibility of the production process. It is indeed the small quantities in the recipe that constitute raw materials which define taste and are therefore decisive in terms of product quality. The objective is therefore to combine the automatic and manual steps into one unit. The key challenges are: • Recipe management • Reliable dosing and weighing true to recipe • Ensuring effective tracking and tracing Customer benefits and advantages The combination of a vacuum processing system and a PC-based weighing system provides, over the entire production process, precisely the transparency and reliability that are required in the modern food industry. Guidance of the operating personnel as well as monitoring and documentation of the process are of decisive importance as, despite the flexibility, the final customer demands complete tracking and tracing. The solution The zoamatic smart controller of the vacuum processing system is combined with the ManDos manual weighing system. The zoamatic undertakes the process control, including automatic dosing while ManDos is responsible for reliably preparing the small additives quantities. If required, the entire system can also be connected to a customers ERP system. Manual weighing is operator-guided at the ManDos station for each individual batch. A touch screen PC guides the operator through the recipe. Every weighing operation is monitored and documented by the touch screen PC, thus ensuring automatic tracing. Recipe tolerances are, of course, closely monitored. Registering raw material batches by barcode reader and labelling the finished manually weighed container with barcode monitoring directly at the feeding point in the processing system are a further option.
Open the catalog to page 1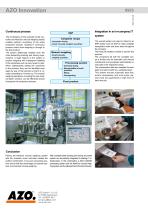
Continuous process The combination of the zoamatic smart controller and ManDos manual weighing facility enables optimum monitoring of the entire production process, resulting in continuous process control from weighing in through to the final product. The system additionally satisfies even the most demanding tracking and tracing requirements. A major feature of the system is product weighing with subsequent labelling of the containers such as pots, bowls or tubs. When subsequently adding the containers to the process, they can be identified once again by way of the barcode so that it is...
Open the catalog to page 2All AZO Group catalogs and technical brochures
-
Conveying unit M235-38
2 Pages
-
UFS 75
2 Pages
-
AZODOS
4 Pages
-
ShuttleDos®
4 Pages
-
RoLog®
2 Pages
-
DosiBox®
2 Pages
-
AZO BATCHTAINER®
2 Pages
-
AZO liquids
20 Pages
-
Quaiphar
8 Pages
-
BG
6 Pages
-
Azo WMD
2 Pages
-
AZO Dough Lines
2 Pages
-
ShuttleDos
2 Pages
-
ManDos Mobile
2 Pages
-
mixer container
2 Pages
-
ManDos
2 Pages