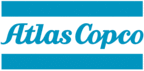

Catalog excerpts
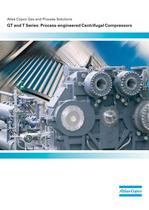
Atlas Copco Gas and Process Solutions GT and T Series: Process-engineered Centrifugal Compressors
Open the catalog to page 1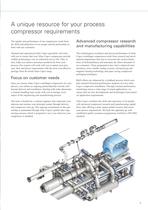
3 A unique resource for your process compressor requirements The quality and performance of our compressors result from the skills and dedication of our people and the partnership we form with our customers. Talented and experienced Atlas Copco specialists will work with you to ensure that your Atlas Copco compressors provide reliable performance over an unlimited service life. That, in turn, helps you achieve maximum productivity form your process. Our experts will work with you to match your pressure, flow and power requirements with the most cost-effective package from the broad Atlas...
Open the catalog to page 3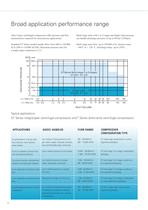
Broad application performance range Typical applications GT Series integral-gear centrifugal compressors and T Series direct-drive centrifugal compressors. Atlas Copco centrifugal compressors offer pressure and flow characteristics required for most process applications. Standard GT Series models handle flows from 600 to 250,000 m3/h (300 to 118,000 ACFM). Maximum pressure ratio for a single-stage compressor is 3.5. Multi-stage units with 2 to 8 stages and higher inlet pressure can handle discharge pressures of up to 90 bar (1305psi). Multi-stage units flow: up to 250,000 m3/h. Suction...
Open the catalog to page 4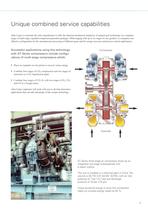
5 Unique combined service capabilities Successful applications using this technology with GT Series compressors include configurations of multi-stage compressors which: • Place an expander on one pinion to recover waste energy. • Combine four stages of CO2 compression and two stages of ammonia in a CO2 liquefaction plant. • Combine four stages of CO2 H2 with two stages of H2, CO2 and CO in a Syngas plant. Atlas Copco engineers will work with you to develop innovative applications that can take advantage of this unique technology. Atlas Copco is currently the only manufacturer to offer the...
Open the catalog to page 5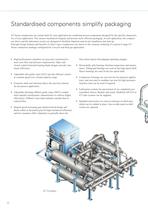
6 Standardised components simplify packaging GT Series compressors are custom built for your application by combining proven components designed for the specific characteristics of your application. This ensures mechanical integrity and permits more efficient packaging. In each application, the compressor, driver and the lubrication system are designed to facilitate shipment and on-site installation and start-up. Principal design features and benefits of Atlas Copco compressors are shown in this cutaway rendering of a typical 6-stage GT Series compressor package configured for a recycle and...
Open the catalog to page 6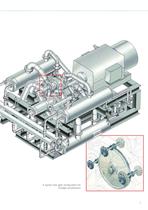
7 A typical rotor gear configuration for 6-stage compressors
Open the catalog to page 7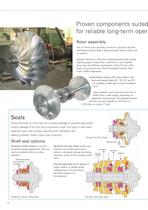
8 Rotor assembly The GT Series rotor assembly consists of a precisely matched and balanced pinion shaft, a high-speed gear, thrust collars, and an impeller. Impeller selection is made from standard geometrically similar impeller groups. Unique flow coefficients in each impeller group meet the different requirements of the GT Series flow range. All geometries have been thoroughly tested by Atlas Copco’s R&D department. Radial-bladed impellers (90°) and impellers with backward leaning blades (45°, 50°, 65° and 70°) are available in either open or closed configurations. Open impellers can be...
Open the catalog to page 8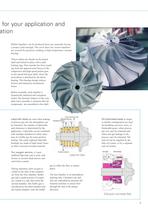
9 d for your application and ration Milled impellers can be produced from any materials having a proper yield strength. The cover discs for closed impellers are secured by precision welding or high temperature vacuum brazing. Thrust collars are shrunk on the pinion shaft and locked in place with a split locking ring. They transfer the force resulting from the opposed axial forces of the compressor and high-speed pinion gear to low-speed bull gear shaft, where the axial thrust is absorbed by the thrust bearing. This bearing design reduces friction and minimises mechanical losses. Before...
Open the catalog to page 9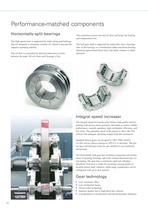
10 Horizontally-split bearings The high-speed rotor is supported by radial tilting pad bearings that are designed to eliminate virtually all vibration and provide superior operating stability. The oil flow is controlled by directed lubrication nozzles between the pads. Oil exit from each bearing is free. This minimises power loss and oil flow and keeps the bearing pad temperatures low. The bull gear shaft is supported by multi-lobe sleeve bearings. One of the bearings is a combination radial and thrust bearing featuring tapered land thrust faces that allow rotation in either direction....
Open the catalog to page 10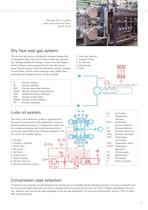
11 Lube oil system The Atlas Copco lubrication system is engineered for the specific requirements of the application, using our standard packaged designs. It is designed to ensure that the compressor bearings and integral gearing always receive the proper lubrication. Systems designed to API 614 or 672 are available options. 1. Oil tank 2. Auxiliary oil pump 3. Relief valve 4. Oil cooler 5. Oil filter 6. Control valve 7. Main oil pump 8. Oil dust filter fan 9. Reverse protection system Compressor case selection Compressor case materials are determined by the specific gas to be handled and...
Open the catalog to page 11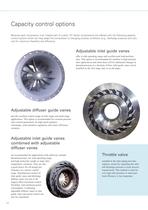
12 Because each compressor is an integral part of a plant, GT Series compressors are offered with the following capacity control options which can help adapt the compressor to changing process conditions (e.g., discharge pressure and volume) for maximum flexibility and efficiency. Capacity control options Adjustable inlet guide vanes offer a wide operating range and excellent part load performance. This option is recommended for medium to high pressure ratio applications and when there will be substantial changes in demand pressure as a function of flow. Inlet guide vanes can be installed...
Open the catalog to page 12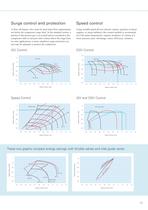
13 Surge control and protection A blow off bypass valve must be used when flow requirements are below the compressor surge limit. In the standard system, a portion of the process gas is re-cooled and re-circulated to the compressor inlet to increase inlet volume above the surge limit. In some applications, a motor shutdown surge protection system may be adequate to protect the compressor. Speed control Using variable speed drivers (electric motors, gasoline or diesel engines, or steam turbines), this control method is recommended if the plant characteristic requires turndown of volume at a...
Open the catalog to page 13All ATLAS Copco Compressors USA catalogs and technical brochures
-
SCROLL COMPRESSORS SF / SF+
7 Pages
-
LZ OIL-FREE COMPRESSOR
5 Pages
-
TP-Series
2 Pages
-
T-Series
2 Pages
-
H series
2 Pages
-
ZM31 -246
3 Pages
-
T3W Water Well Drill
1 Pages
-
Condensate Management
2 Pages
-
Atlas Copco Portable Air
2 Pages
-
Membrane Nitrogen Generators
2 Pages
-
mVAC-250 ? mVAC-9200
12 Pages
-
P 37 - P 275
12 Pages
-
Brochure GA 11+-30/GA 15-30 VSD
20 Pages
-
Brochure G 110-250
8 Pages
-
Brochure ZH+
16 Pages
-
Brochure ZH 350+
12 Pages
-
Brochure ZS+ VSD
20 Pages
-
Brochure ZS
20 Pages
-
Brochure ZB 5-120 VSD
12 Pages
-
Brochure ZB 100-160 VSD
12 Pages
-
Marine Air Booklet
68 Pages
-
Brochure FX 1-21
5 Pages
-
Brochure FD
9 Pages
-
Brochure OSC/OSD
8 Pages
-
Brochure CD 1-22+
2 Pages
-
Driving Expander Technology
29 Pages
-
MED Breathing and Surgical Air
12 Pages
-
Silicone free Filters
2 Pages
-
Compressed Air Filters
12 Pages
-
FD 5-4000
6 Pages
-
ZB 100-160 VSD 100-160 kW
12 Pages
-
ZR/ZT 55-90 FF & ZR/ZT 90 VSD-FF
22 Pages
-
AQ 30-55/ AQ 37-55 VSD
18 Pages
-
Oil-free Scroll Compressors
12 Pages
-
LFx 0.7-2.0
12 Pages
-
GA 30+-90/GA 37-90 VSD®
16 Pages
-
Atlas Copco Railway compressors
12 Pages
-
GN 4-18 kW/5.5-25 hp
6 Pages
-
GX 2-11
6 Pages
-
XA(M,H)S 500-750
2 Pages
-
XAS 137 XAHS 107
2 Pages
-
HardHat™
6 Pages
-
BD 100-3000
8 Pages