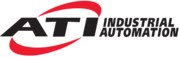

Catalog excerpts
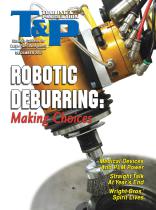
production strategies
Open the catalog to page 1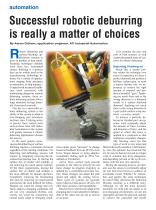
Successful robotic deburring is really a matter of choices By Aaron Odham, application engineer, ATI Industrial Automation Robotic deburring and surface-finishing applications continue to grow in number as lean manufacturing techniques demand more from less. Automated surface finishing is a process that can be widely used in the manufacturing technology industry for a variety of applications ranging from aerospace to automotive to ship industry.1 Coupled with increased healthcare costs associated with maintaining dangerous manual deburring systems, these robotic deburring systems have...
Open the catalog to page 2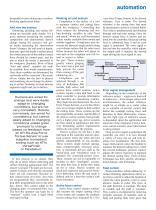
demanded in most deburring or surfacefinishing applications today. And now the science Deburring, grinding, and surface finishing are basically quite simple. For a given material (assuming the material composition and characteristic doesn’t change during the process) and given media (assuming the abrasiveness doesn’t change), the end result is dependent only upon the media’s surface speed, the contact pressure of the media (contact force divided by contact area), and the rate at which the media is presented to the workpiece (feedrate). Most of these “feed and speed” variables are readily...
Open the catalog to page 3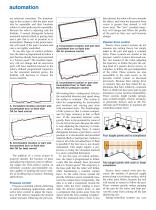
automation are relatively consistent. The disadvantage to this system is that the parts must also be repeatable and their locations relative to robot path must be repeatable. Because the robot is adjusting only the feedrate, it cannot distinguish between unwanted material (flash or parting line) and a part that is out of position or is inconsistent. Damage to the parent material will result if the part’s location and size is not tightly controlled. To use this type of control architecture, the robot is programmed to follow a part that has already been processed and is a “known good.” The...
Open the catalog to page 4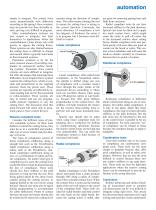
simple to integrate. The contact force varies proportionally with deflection according to the spring’s force constant, and can provide less than desirable resuits, proving very difficult to program. Mass counterbalance systems are also simple to integrate, but limit themselves to applications where the counterbalance’s mass always acts with gravity to oppose the cutting forces. These systems are also limited because the cutting force is difficult to change and inertial effects typically limit them to floor-mounted systems. Pneumatic actuation is by far the most common means of providing...
Open the catalog to page 5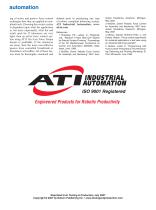
ing of active and passive force control techniques how they are applied to compliant tools. Choosing the correct system is dependent upon what the application is, but more importantly, what the end result must be. If tolerances are very tight, then an active force control system using ATI’s Six-Axis Force Torque Sensor is justifiable. If the tolerances are loose, then the more cost-effective passive force controlled VersaFinish or Flexdeburr will suffice. All of these factors must be thoroughly examined and defined prior to purchasing any type of robotic compliant deburring system. ATI...
Open the catalog to page 6All ATI Industrial Automation catalogs and technical brochures
-
Manual tool changers
2 Pages
-
Robotic & CNC Deburring Tools
12 Pages
-
Collision Sensor catalog
8 Pages
-
Utility coupler
2 Pages
-
Corporate overview
8 Pages