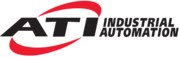

Catalog excerpts
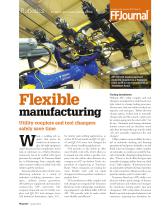
As seen in the January 2013 issue of BY GRETCHEN SALOIS, SENIOR EDITOR ATI QC-210 master and tool modules coupled on a Yaskawa robot with an end-of-arm tool at Tennessee Rand. Flexible manufacturing Utility couplers and tool changers safely save time hen a welding job requires that pieces be worked on at various angles, the right equipment makes the process less complicated. A fuel tank or sub-frame on a Harley-Davidson motorcycle has to be welded with expert precision, for example. At Tennessee Rand Inc. in Chattanooga, Tenn., using the right system ensures workers can safely work with robots to get the job done. Tennessee Rand provides robotic manufacturing solutions to a variety of industries including automotive, aerospace, military, power generation, off-road/heavy equipment and recreation (motorcycles, ATV, watercraft). The company frequently uses G4 utility couplers and QC-210 tool changers from ATI Industrial Automation, Apex, N.C., FFJournal® January 2013 for robotic spot-welding applications, as well as ATI’s tool stands and QC-21, QC41 and QC-310 series tool changers for other robotic handling applications. “ATI provides us the ability to offer more flexible work cells, which allows us to expand not only within a specific company, but also within other divisions of a company as well,” says Andrew Neely, vice president of engineering at Tennessee Rand. “More companies are looking for more flexible work cells for rapid changeover between product variations or product lines.” “ATI manufactures utility couplers and tool changers so companies like Tennessee Rand can create cutting-edge manufacturing equipment,” says Robert Little, CEO of ATI. “We provide tools to make robots more flexible and efficient.” Tooling breakdown Without ATI’s utility couplers and tool changers, manufacturers would need multiple robots to change tooling processes, whereas now, only one robot is needed, saving time, cost and space. “Before this tool change option, workers had to manually change tools and this caused a safety issue for workers going into the robot cells,” Little says. “Automatic tool changes eliminate human contact and are therefore much safer than having workers go into the robot cell and manually implement the tool changes.” Utility couplers connect utilities for manual or automatic docking and fixturing operations to load power, hydraulics, air and fluids. Like tool changers, utility couplers are automatic, so workers can avoid the hazard of manually changing tooling between jobs. “There’s a lot of effort that goes into manually changing utilities from say, fluid to air,” Little explains. “If instead you have an automated method to do that, it provides for a fast connection, taking seconds as opposed to minutes, and it is much safer.” Tennessee Rand uses ATI’s utility couplers for robotic quick-change of fixtures on/off indexers and robotic tool changers for end-of-arm tooling and/or spot gun changeover. ATI’s setup allows Tennessee Rand to provide automated solutions to i
Open the catalog to page 1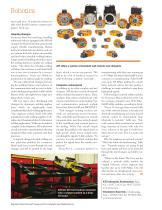
Robotics tween part runs. “It makes the systems we offer more flexible between customer programs,” Neely says. Ongoing changes Tennessee Rand has used large handling robots and indexers equipped with ATI tool changers for Harley-Davidson projects that require flexible manufacturing. Robots dock and undock between fixtures and can run various fuel tank, frame sub-assembly and final frame assembly welding fixtures. Larger material handling robots then move the welding fixtures to smaller arc welding robots. “This allows for a flexible welding cell where the customer is not limited with one or...
Open the catalog to page 2All ATI Industrial Automation catalogs and technical brochures
-
Manual tool changers
2 Pages
-
Robotic & CNC Deburring Tools
12 Pages
-
Collision Sensor catalog
8 Pages
-
Utility coupler
2 Pages
-
Corporate overview
8 Pages