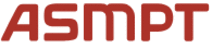
Catalog excerpts
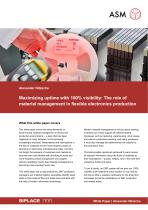
Alexander Nitzsche Maximizing uptime with 100% visibility: The role of material management in flexible electronics production What this white paper covers This white paper covers the rising demands on synchronized material management in electronics production environments – a topic that has been neglected in many factories, but is becoming increasingly important. Weaknesses and interruptions in the flow of materials are the most frequent causes of downtime in electronics manufacturing today. And let’s not forget: the pressure of customers and markets to become ever more flexible with shrinking lot sizes and more frequent product changeovers and tougher delivery deadlines means that material management is becoming more important every day. This white paper will to help executives, SMT production managers and material logistics specialists identify weak spots in their material flow and make improvements with the help of modern information technology. Modern material management is not just about tracking inventory but it must support all material-related processes such as receiving, warehousing, stock issues and returns, production planning, and setup processes. It must also manage the replenishment of material to the production lines. The best possible results are achieved if users receive all relevant information about the flows of materials at their workstations – quickly, reliably, and in line with their respective duties and tasks. To put it bluntly, an ERP system will not give you 100% visibility of all material at every location in your factory, but that is what is needed, particularly for the shop floor processes and at the workstations in SMT production and related areas. White Paper | Alexander Nitzs
Open the catalog to page 1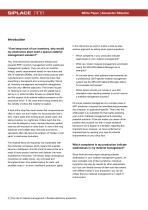
White Paper | Alexander Nitzsche Introduction “If we keep track of our inventory, why would my electronics plant need a special material management solution?” Yes, most electronics manufacturers already have powerful ERP, inventory management and/or warehouse management systems. They can print out inventory listings, predict requirements based on new orders and bills of materials (BOMs), and report what products were manufactured in recent months. Does that mean that everything is transparent and running smoothly? Not at all. Inventory management and material management have two very...
Open the catalog to page 2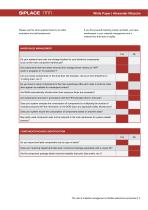
Please use this short questionnaire for an initial evaluation and self-assessment. White Paper | Alexander Nitzsche If you find yourself checking mostly red fields, you have weaknesses in your material management and a material flow that lacks in agility. Are the component package labels machine-readable (barcode, data matrix, etc.)? The role of material management in flexible electronics production | 3
Open the catalog to page 3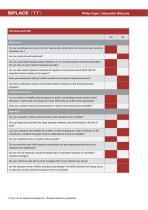
White Paper | Alexander Nitzsche PROCESS SUPPORT Do your warehouse and your shop floor operate with printed pick lists, inventory lists, receiving checklists, etc.? Are your pick lists path-optimized? Are your automated storage systems (Kardex, etc.) or material towers controlled separately? Do you have to enter material requests manually? Do you take classic physical inventories to regularly reconcile your actual stock with the theoretical stock numbers in the system? Does your warehouse staff get notified in advance of required material provisions? Are these notifications issued not...
Open the catalog to page 4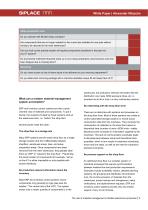
White Paper | Alexander NitzscheSetup preparation area Do you operate with flexible setup concepts? Are components that are no longer needed for the current job available for new jobs without having to be returned to the main warehouse? Can you look up the precise location of required components anywhere in the plant via your IT system? Do provisioned materials frequently stack up in your setup preparation area because a job has been delayed due to missing items? Do you have access to lists of items about to be delivered to your receiving department? Do you label each incoming package with...
Open the catalog to page 5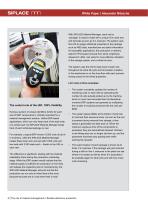
White Paper | Alexander Nitzsche The central role of the UID: 100% Visibility Having a system of unique identifiers (UIDs) for each reel of SMT components is critically important for a material management solution. Unlike ERP-based applications, which can only keep track of the total units of a certain part, the SIPLACE Material Manager keeps track of each individual package or reel. For example, a typical ERP shows 10,000 units of part A in inventory, while the SIPLACE Material Manager breaks these down into one reel with 5,000 units and two reels with 2,500 reels each - thanks to the UID...
Open the catalog to page 6
White Paper | Alexander Nitzsche No SMT-specific functionalities SMT production has several characteristics that can't be mapped in ERP systems or only at very great expense. A simple example is the recording of exposure times for moisture-sensitive devices and the automatic blocking of their use if these exposure times are exceeded. This is exactly the point where modern solutions like SIPLACE's Material Manager come into play. They supplement the higher-level ERP systems and link them with the production processes on the shop floor level. They also provide manufacturers wanting to make...
Open the catalog to page 7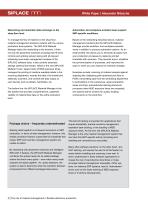
White Paper | Alexander Nitzsche Networking and automatic data exchange on the shop floor level To manage the flow of material on the shop floor, material management solutions network with the various production-level systems. The SIPLACE Material Manager takes this networking to the extreme. It links not only the placement machines including their fill level controls and splicing sensors along with all relevant scheduling and setup management modules of the SIPLACE software suite, it also controls automatic storage systems like Kardex, Hanel or the new SIPLACE Material Tower, keeps tracks...
Open the catalog to page 8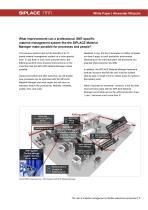
White Paper | Alexander NitzscheWhat improvements can a professional, SMT-specific material management system like the SIPLACE Material Manager make possible for processes and people? The previous sections laid out the benefits of an IT-based material management system on a more general level. To put them in even more concrete terms, the following sections show process improvements on the shop floor that the SIPLACE Material Manager makes possible. Using some before and after scenarios, we will explain how processes can be optimized with the SIPLACE Material Manager and what impact this...
Open the catalog to page 9All ASM Assembly Systems catalogs and technical brochures
-
SIPLACE CA2
4 Pages
-
DEK TQ printer platform
4 Pages
-
Stencils from the global No. 1
20 Pages
-
DEK NeoHorizon iX platform
12 Pages
-
DEK TQ
4 Pages
-
IPC-HERMES-9852
2 Pages
-
Galaxy Printing Platform
4 Pages
-
SIPLACE X-Series S
20 Pages
-
SIPLACE TX
4 Pages
-
SMT Factory
6 Pages
-
SIPLACE SMT-INSIGHTS
16 Pages
-
SIPLACE SX
12 Pages
-
ADAMOS
2 Pages
-
ASM ProcessExpert
12 Pages
-
Advanced Packaging
20 Pages
-
SMT Smart Network
28 Pages
-
SIPLACE SX-Series
12 Pages
-
SIPLACE TX
4 Pages