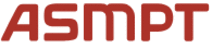
Catalog excerpts
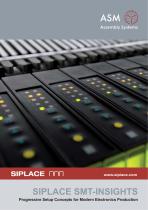
SIPLACE SMT-INSIGHTS Progressive Setup Concepts for Modern Electronics Production
Open the catalog to page 1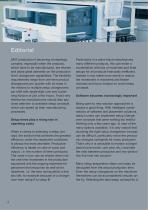
Editorial SMT production is becoming increasingly complex, especially when the products, which have to be manufactured, are diverse and place great demands on the production line’s changeover capabilities. The flexibility requirements range from one-time product changeovers per quarter with lot sizes in the millions to multiple setup changeovers per shift with single-digit runs and a planning horizon of just a few hours. That’s why electronics manufacturers should also pay close attention to available setup concepts which can speed up their manufacturing processes. Setup times play a rising...
Open the catalog to page 2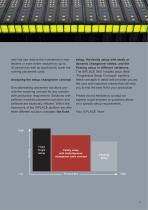
new line can reduce the investment in new feeders or even entire modules by up to 30 percent as well as significantly lower the running placement costs. Analyzing the setup changeover concept Groundbreaking placement solutions provide the matching concept for any conceivable production requirement. Solutions with perfectly matched placement solutions and software are especially efficient. Within the framework of the SIPLACE platform we offer three different solution concepts: the fixed setup, the family setup with static or dynamic changeover tables, and the floating setup in different...
Open the catalog to page 3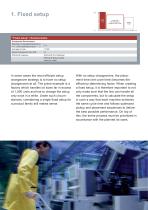
1. Fixed setup “Fixed setup” characteristics In some cases the most efficient setup changeover strategy is to have no setup changeovers at all. The prime example is a factory which handles lot sizes far in excess of 1,000 units and has to change the setup only once in a while. Under such circumstances, considering a single fixed setup for a product family still makes sense. With no setup changeovers, the placement time (net cycle time) becomes the efficiency-determining factor. When creating a fixed setup, it is therefore important to not only make sure that the line can handle all the...
Open the catalog to page 4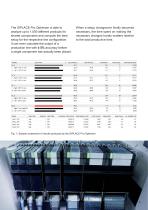
The SIPLACE Pro Optimizer is able to analyze up to 1,000 different products for shared components and compute the best setup for the respective line configuration. It can even calculate the output of a production line with ± 5% accuracy before a single component has actually been placed. When a setup changeover finally becomes necessary, the time spent on making the necessary changes hardly matters relative to the total productive time. Fig. 1: Sample screenshot of results produced by the SIPLACE Pro Optimizer
Open the catalog to page 5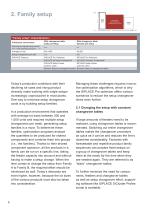
“Family setup” characteristics: Today’s production conditions with their declining lot sizes and rising product diversity make working with single setups increasingly unproductive in most plants. One way to minimize setup changeover costs is by building setup families. In a production environment that operates with average lot sizes between 200 and 1,000 units and requires multiple setup changeovers per week, generating setup families is a must. To determine these families, optimization programs analyze the quantities to be produced for shared components and combine them into groups (i.e.,...
Open the catalog to page 6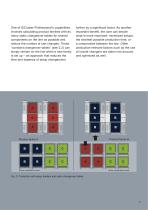
One of SiCluster Professional’s capabilities involves calculating product families with as many static changeover tables for shared components on the line as possible and reduce the number of cart changes. These “constant changeover tables” (see 2.2) can simply remain on the line when a new family is set up – an approach that reduces the time and expense of setup changeovers further by a significant factor. As another important benefit, the user can decide what is more important: minimized setups, the shortest possible production time, or a compromise between the two. Other...
Open the catalog to page 7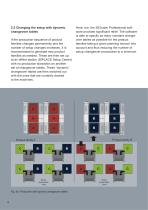
2.2 Changing the setup with dynamic changeover tables If the production sequence of product families changes permanently and the number of setup changes increases, it is recommended to generate new product families as needed. These are then set up at an offline station (SIPLACE Setup Center) with no production slowdown on another set of changeover tables. These “dynamic” changeover tables are then switched out with the ones that are currently docked to the machines. Here, too, the SiCluster Professional software provides significant relief. The software is able to specify as many constant...
Open the catalog to page 8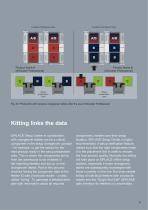
Constant changeover table Constant changeover table Product family A (SiCluster Professional) Product family B (SiCluster Professional) Setup preparation area Setup preparation area Fig. 3b: Production with dynamic changeover tables after the use of SiCluster Professional Kitting links the data SIPLACE Setup Center in combination with changeover tables can be a critical component in the setup changeover concept – for example, to get the setups for the next product ready in the setup preparation area. This is where the components arrive from the warehouse to be installed in the matching...
Open the catalog to page 9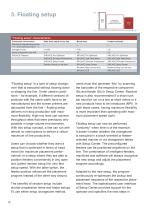
“Floating setup” characteristics “Floating setup” is a type of setup changeover that is executed without slowing down or stopping the line. Under certain conditions - for example, if different versions of products with the same width have to be manufactured and the screen printers are decoupled from the line - floating setup delivers non-stop production with maximum flexibility. High-mix lines can achieve throughput rates that were previously only possible in large-volume environments. With this setup concept, a line can run with almost no interruptions to deliver a virtual maximum of line...
Open the catalog to page 10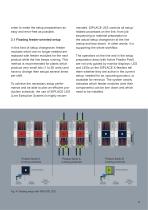
order to make the setup preparations as easy and error-free as possible. 3.1 Floating feeder-oriented setup In this kind of setup changeover, feeder modules which are no longer needed are replaced with feeder modules for the next product while the line keeps running. This method is recommended for plants which produce very small lots (1 to 50 units) and have to change their setups several times per shift. To achieve the necessary setup performance and be able to plan an efficient production schedule, the use of SIPLACE LES (Line Execution System) is highly recom- Product family A is being...
Open the catalog to page 11All ASM Assembly Systems catalogs and technical brochures
-
SIPLACE CA2
4 Pages
-
DEK TQ printer platform
4 Pages
-
Stencils from the global No. 1
20 Pages
-
DEK NeoHorizon iX platform
12 Pages
-
DEK TQ
4 Pages
-
IPC-HERMES-9852
2 Pages
-
Galaxy Printing Platform
4 Pages
-
SIPLACE X-Series S
20 Pages
-
SIPLACE TX
4 Pages
-
SMT Factory
6 Pages
-
White Paper
20 Pages
-
SIPLACE SX
12 Pages
-
ADAMOS
2 Pages
-
ASM ProcessExpert
12 Pages
-
Advanced Packaging
20 Pages
-
SMT Smart Network
28 Pages
-
SIPLACE SX-Series
12 Pages
-
SIPLACE TX
4 Pages