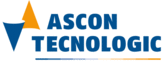
Group: ASCON TECNOLOGIC Group

Catalog excerpts
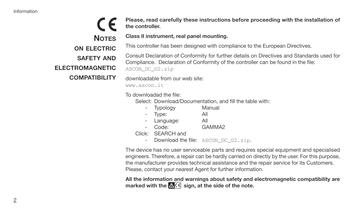
proceeding with the installation of to the European Directives. on Directives and Standards used for controller can be found in the file: table with: zip. requires special equipment and specialised on directly by the user. For this purpose, the repair service for its Customers. information. and electromagnetic compatibility are note.
Open the catalog to page 3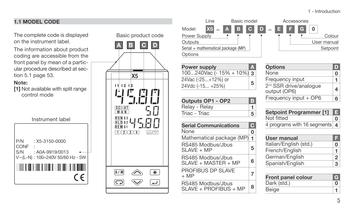
5 1 - Introduction – model Accessories Colour User manual Setpoint C D E F G 0 A 3 5 5 B 1 5 C 0 2nd SSR drive/analogue output (OP6) 4 Options D None 0 6 7 8 Setpoint Programmer [1] E Not fitted 0 4 programs with 16 segments 4 User manual F Italian/English (std.) 0 French/English 1 German/English 2 Spanish/English 3 Front panel colour G Dark (std.) 0 Beige 1 Frequency input 1 Frequency input + OP6 6 1
Open the catalog to page 6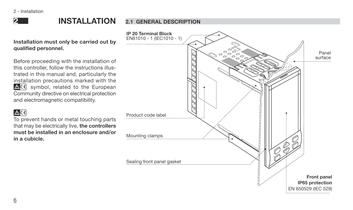
Front panel IP65 protection EN 650529 (IEC 529) Panel surface
Open the catalog to page 7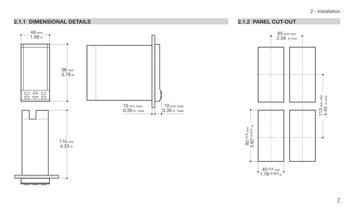
7 2 - Installation PANEL CUT-OUT 65 mm min 2.56 in min 45+0.6 mm 1.78+0.023 in 3.62+0.031 in 113 mm min 4.45 in min
Open the catalog to page 8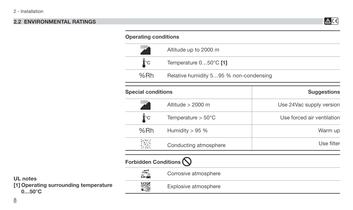
B condensing Use filter Warm up Use forced air ventilation Use 24Vac supply version Suggestions
Open the catalog to page 9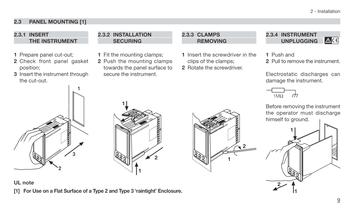
9 2 - Installation the 2.3.4 INSTRUMENT UNPLUGGING B 1 Push and 2 Pull to remove the instrument. Electrostatic discharges can damage the instrument. Before removing the instrument the operator must discharge himself to ground. 1MÙ 2 1 1
Open the catalog to page 10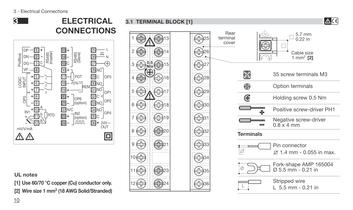
Terminals Cable size 1 mm2 [2] 5.7 mm 0.22 in B 35 screw terminals M3 Option terminals Holding screw 0.5 Nm Positive screw-driver PH1 Negative screw-driver 0.8 x 4 mm Pin connector q 1.4 mm - 0.055 in max. Fork-shape AMP 165004 Ø 5.5 mm - 0.21 in Stripped wire L 5.5 mm - 0.21 in
Open the catalog to page 11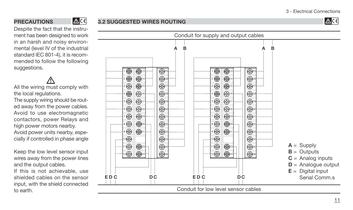
28 27 30 29 26 25 31 32 33 34 35 36 A B 11 3 - Electrical Connections cables cables B A = Supply B = Outputs C = Analog inputs D = Analogue output E = Digital input Serial Comm.s
Open the catalog to page 12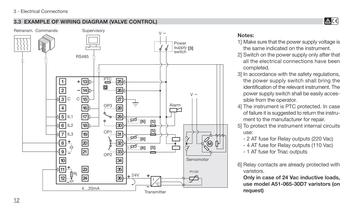
B Notes: Make sure that the power supply voltage is the same indicated on the instrument. Switch on the power supply only after that the electrical connections have been completed. accordance with the safety regulations, the power supply switch shall bring the identification of the relevant instrument. The power supply switch shall be easily accessible from the operator. The instrument is PTC protected. In case failure it is suggested to return the instrument to the manufacturer for repair. protect the instrument internal circuits use: AT fuse for Relay outputs (220 Vac) AT fuse for Relay...
Open the catalog to page 13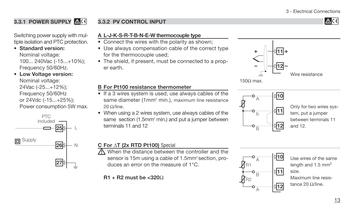
13 3 - Electrical Connections B Wire resistance 150Ù max. Only for two wires system, put a jumper between terminals 11 and 12. Use wires of the same length and 1.5 mm2 size. Maximum line resistance 20 Ù/line. 10 11 12 A B A R2 R1 10 11 12 A b B 11 12
Open the catalog to page 14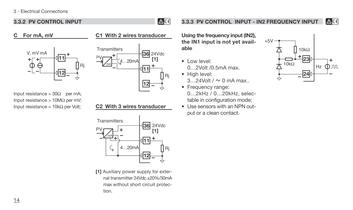
INPUT - IN2 FREQUENCY INPUT B IN2), available selectable mode; output +5V 23 24 10kÙ 10kÙ Hz
Open the catalog to page 15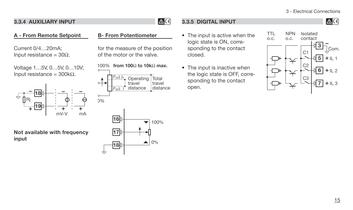
15 3 - Electrical Connections B the corresponding 3 7 6 TTL o.c. Isolated contact Com. IL 3 IL 2 C2 C3 5 NPN o.c. IL 1 C1
Open the catalog to page 16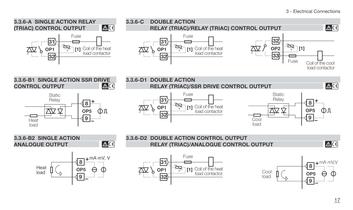
17 3 - Electrical Connections CONTROL OUTPUT B OUTPUT B OUTPUT B Fuse Coil of the cool load contactor 32 33 OP2 [1] Cool load Static Relay 8 9 OP5 8 9 Cool OP5 load mA mV,V
Open the catalog to page 18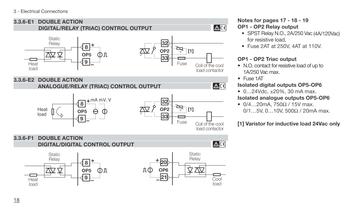
Notes for pages 17 - 18 - 19 - OP2 Relay output SPST Relay N.O., 2A/250 Vac (4A/120Vac) for resistive load, Fuse 2AT at 250V, 4AT at 110V. - OP2 Triac output O. contact for resistive load of up to 1A/250 Vac max. Fuse 1AT Isolated digital outputs OP5-OP6 0…24Vdc, ±20%, 30 mA max. Isolated analogue outputs OP5-OP6 4…20mA, 750Ù / 15V max. 1…5V, 0…10V, 500Ù / 20mA max. Varistor for inductive load 24Vac only
Open the catalog to page 19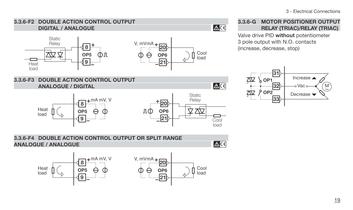
19 3 - Electrical Connections 3.3.6-G MOTOR POSITIONER OUTPUT RELAY (TRIAC)/RELAY (TRIAC) Valve drive PID without potentiometer pole output with N.O. contacts increase, decrease, stop) OP1 33 32 31 OP2 Vac Decrease Increase M~
Open the catalog to page 20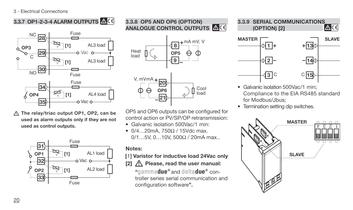
SERIAL COMMUNICATIONS (OPTION) [2] B Galvanic isolation 500Vac/1 min; Compliance to the EIA RS485 standard Modbus/Jbus; Termination setting dip switches. C C MASTER SLAVE 1 2 3 13 14 15 1 2 3 4 MASTER SLAVE
Open the catalog to page 21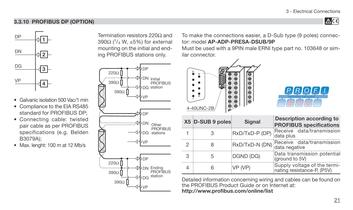
B 21 3 - Electrical Connections concerning wiring and cables can be found on Guide or on Internet at: online/list 33 easier, a D-Sub type (9 poles) connector: PRESA-DSUB/9P male ERNI type part no. 103648 or similar Signal Description according to PROFIBUS specifications TxD-P (DP) Receive data/transmission data plus TxD-N (DN) Receive data/transmission data negative VP) (DG) Data transmission potential (ground to 5V) Supply voltage of the terminating resistance-P, (P5V)
Open the catalog to page 22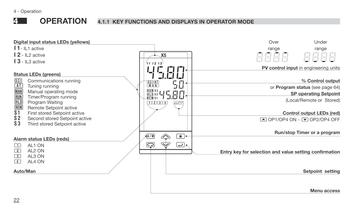
MODE Over range Under range SP operating Setpoint (Local/Remote or Stored) % Control output or Program status (see page 64) Control output LEDs (red) åOP1/OP4 ON - çOP2/OP4 OFF Run/stop Timer or a program selection and value setting confirmation Setpoint setting Menu access 8_8_8_8_ -8-8-8-8 PV control input in engineering units
Open the catalog to page 23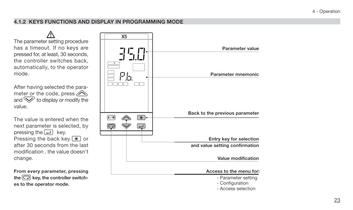
23 4 - Operation value mnemonic parameter selection confirmation modification menu for: setting selection
Open the catalog to page 24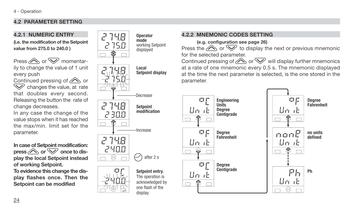
SETTING page 26) display the next or previous mnemonic or %will display further mnemonics every 0.5 s. The mnemonic displayed parameter is selected, is the one stored in the Unit °f Unit none Unit ph Degree Fahrenheit no units defined Ph
Open the catalog to page 25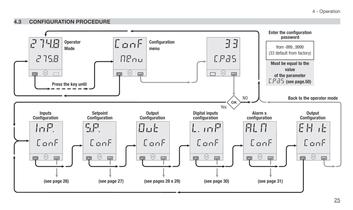
25 4 - Operation EHit ALM Conf Conf (see page 31) Back to the operator mode Enter the configuration password Must be equal to the value of the parameter C.Pas (see page.50) from -999...9999 (33 default from factory) Alarm s configuration Output Configuration
Open the catalog to page 26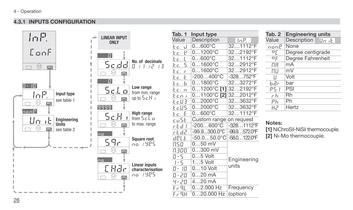
Hertz ph Hz PInp . 1112°F request Engineering 122.0°F 572.0°F 1112°F 752°F 2912°F 2912°F 2192°F 1112°F Value Description éUnit Tab. 2 Engineering units none None rh °C Degree centigrade °f Degree Fahrenheit Rh MA mA MU mV U Volt Ph bar bar psI PSI Frequency 3272°F 2192°F 1112°F 3632°F 3632°F 2012°F Notes: [1] NiChroSil-NiSil thermocouple. [2] Ni-Mo thermocouple.
Open the catalog to page 27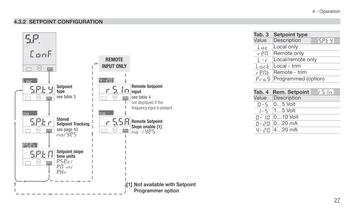
27 4 - Operation Tab. 4 Rem. Setpoint Value Description 0=5 0…5 Volt 1=5 1…5 Volt 0=20 0…20 mA Tab. 3 4=20 4…20 mA Setpoint type 0=10 reM.t Remote - trim 0…10 Volt érs.In loc.t Local - trim l=r Local/remote only reM Remote only loc Local only Value Description éS.P.ty Prog Programmed (option)
Open the catalog to page 28All ASCON TECNOLOGIC catalogs and technical brochures
-
REFRIGERATION CATALOGUE 2020
85 Pages
-
NP4
2 Pages
-
ZIS EIIRLIBGPMAT2018
1 Pages
-
KR1E
4 Pages
-
VA7810 Series Self-Calibrating
10 Pages
-
ClimaPAC
8 Pages
-
at on cloud
8 Pages
-
Sensitive Touch - Data sheet
4 Pages
-
Z31/Y39 - Data sheet
4 Pages
-
ASCOMB - Technical bulletin
12 Pages
-
CATALOGO PRODOTTI 2014/2015
113 Pages
-
Refrigeration catalogue 2016
168 Pages
-
TCPDE M
2 Pages
-
Sensitive Touch
4 Pages
-
opmt
2 Pages
-
m81
6 Pages
-
MP02
2 Pages
-
Loop_components_catalogue_2015
49 Pages
-
Deltadue series
8 Pages
-
Gammadue series
8 Pages
-
IO-CB series
4 Pages
-
Climatic test chambers.
2 Pages
-
Paperless recorder
4 Pages
-
Industrial operator panel
2 Pages
Archived catalogs
-
TRH-MINI
3 Pages
-
TRH52
4 Pages
-
TRH21
4 Pages
-
Pneumatic Actuators
7 Pages