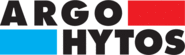

Catalog excerpts
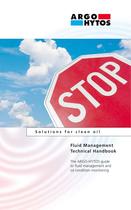
Fluid Management Technical Handbook The ARGO-HYTOS guide to fluid management and oil condition monitoring S o l u t i o n s f o r c l e a n o i l
Open the catalog to page 1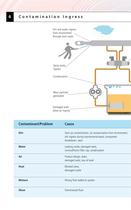
Contaminant/Problem Cause Dirt Start up contamination, oil contamination from environment, dirt ingress during maintenance/repair, component breakdown, wear Water Leaking cooler, damaged seals, no/insufficient filler cap, condensation Air Product design, leaks, damaged seals, low oil level Heat Blocked valve, damaged cooler Mixture Wrong fluid added to system Shear Overstressed fluid Condensation Wear particles generated Damaged seals allow air ingress Dirt and water ingress from environment through worn seals C o n t a m i n a t i o n I n g r e s s Spray water ingress
Open the catalog to page 6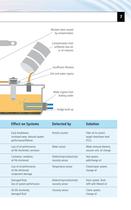
Effect on Systems Detected by Solution Early breakdown, Particle counter Filter oil to correct increased wear, reduced system target cleanliness level performance/lifetime (TCL) Loss of oil performance, Water sensor Water removal element, oil life shortened, corrosion vacuum unit, oil change Cavitation, oxidation, Dielectricity/conductivity/ Seal system, oil life shortened viscosity sensor add/change oil Loss of oil performance, Temperature sensor Check/repair system, oil life shortened, change oil component damage Damaged fluid, Dielectricity/conductivity/ Drain system, flush, loss of...
Open the catalog to page 7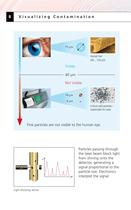
75 ìm Critical solid particles – responsible for wear 14 ìm 4 ìm Not Visible Particles passing through the laser beam block light from shining onto the detector, generating a signal proportional to the particle size. Electronics interpret the signal. Light blocking sensor V i s u a l i z i n g C o n t a m i n a t i o n Visible Human hair (40…120 ìm) 40 ìm Fine particles are not visible to the human eye. mv t
Open the catalog to page 8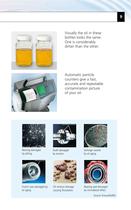
Visually the oil in these bottles looks the same. One is considerably dirtier than the other. Automatic particle counters give a fast, accurate and repeatable contamination picture of your oil. Bearing damaged by pitting Shaft damaged by erosion Damage caused by oil aging Clutch case damaged by oil aging Oil mixture damage causing floculation Bearing seal damaged by microdiesel effect Source: KraussMaffei Verschleiß der Laufflächen Ölalterungsprodukte
Open the catalog to page 9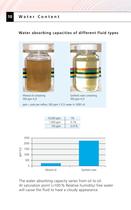
10 Wa t e r C o n t e n t Water absorbing capacities of different fluid types The water absorbing capacity varies from oil to oil. At saturation point (>100 % Relative humidity) free water will cause the fluid to have a cloudy appearance. Mineral oil containing Synthetic ester containing 500 ppm H2O 500 ppm H2O ppm = parts per million, 500 ppm = 0,5 l water in 1000 l oil 10,000 ppm 1% 1,000 ppm 0.1% 100 ppm 0.01% ppm H2O 2500 2000 1500 1000 500 0 Mineral oil Synthetic ester
Open the catalog to page 10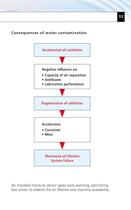
An installed moisture sensor gives early warning, permitting fast action to extend the oil lifetime and machine availability. 11 Consequences of water contamination Negative influence on: • Capacity of air separation • Antifoams • Lubrication performance Accelerated oil oxidation Degeneration of additives Accelerates: • Corrosion • Wear Shortened oil lifetime System failure
Open the catalog to page 11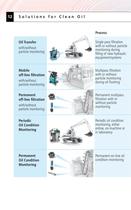
Oil Transfer with/without particle monitoring Mobile off-line filtration with/without particle monitoring Permanent off-line filtration with/without particle monitoring Periodic Oil Condition Monitoring Permanent Oil Condition Monitoring Process Single pass filtration with or without particle monitoring during filling of new hydraulic equipment/systems Multipass filtration with or without particle monitoring during oil flushing Permanent multipass filtration with or without particle monitoring Periodic oil condition monitoring, either online, on-machine or in laboratory Permanent on-line...
Open the catalog to page 12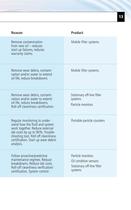
Reason Remove contamination from new oil – reduces start up failures, reduces warranty claims Product Mobile filter systems Remove wear debris, contamination and/or water to extend oil life, reduce breakdowns Remove wear debris, contamination and/or water to extend oil life, reduce breakdowns. Roll-off cleanliness certification. Regular monitoring to understand how the fluid and system work together. Reduce external lab costs by up to 90%. Troubleshooting tool. Roll off cleanliness certification. Start up wear debris analysis. Follow proactive/predictive maintenance regimes. Reduce...
Open the catalog to page 13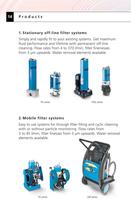
1. Stationary off-line filter systems Simply and rapidly fit to your existing systems. Get maximum fluid performance and lifetime with permanent off-line cleaning. Flow rates from 4 to 370 l/min, filter finenesses from 3 ìm upwards. Water removal elements available. 14 P r o d u c t s FA series UM series FN series FNA series 2. Mobile filter systems Easy to use systems for through filter filling and cyclic cleaning with or without particle monitoring. Flow rates from 3 to 45 l/min, filter finesses from 3 ìm upwards. Water removal elements available.
Open the catalog to page 14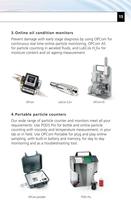
3. Online oil condition monitors Prevent damage with early stage diagnosis by using OPCom for continuous real time online particle monitoring, OPCom AS for particle counting in aerated fluids, and LubCos H20+ for moisture content and oil ageing measurement. 4. Portable particle counters Our wide range of particle counter and monitors meet all your requirements. Use PODS Pro for bottle and online particle counting with viscosity and temperature measurement, in your lab or in field. Use OPCom Portable for plug and play online sampling, with built-in battery and memory, for day to day...
Open the catalog to page 15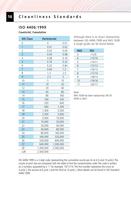
ISO 4406:1999 is a 3 digit code, representing the cumulative counts per ml at 4, 6 and 14 ì m(c). The counts at each size are compared with the table to find the contamination code. The code is written as 3 numbers separated by a '/'. For example: 19/17/14. The first number represents the count at 4 ì m(c ), the second at 6 ì m(c ) and the third at 14 ì m(c ). More details can be found in ISO Standard 4406:1999. C 16 l e a n l i n e s s S t a n d a r d s Counts/ml, Cumulative ISO 4406:199 Although there is no direct relationship between ISO 4406:1999 and NAS 1638 a rough guide can be found...
Open the catalog to page 16All ARGO-HYTOS catalogs and technical brochures
-
MLS3-06
10 Pages
-
C5.3511 · C5.3516 · C5.3529
3 Pages
-
LS 040 · LS 075
6 Pages
-
ES 075
6 Pages
-
Catalogue Hydraulic Drives
65 Pages
-
Catalogue Fluid Management
69 Pages
-
Filtration Guideline
20 Pages
-
Light Line
4 Pages
-
Off-line Filtration
2 Pages
-
Catalogue Filtration
342 Pages
-
Catalogue Lightline
50 Pages
-
RC series
4 Pages
-
TS3 MTS2
6 Pages
-
TS4 MTS
6 Pages
-
ECOLINE
8 Pages
-
SR4P2-B2
4 Pages
-
SR1P2-A2
4 Pages
-
PRM7-10
10 Pages
-
PRM8-06
4 Pages
-
PRM2-04
20 Pages
-
PRM6-10
20 Pages
-
PRM7-06
10 Pages
-
PRM2-06
20 Pages
-
PRM7-04
10 Pages
-
Coils
18 Pages
-
Datasheet RPEL1-06
6 Pages
-
Datasheet RPH2-06
4 Pages
-
Datasheet RPR3-04
4 Pages
Archived catalogs
-
MDA Highlights 2015
24 Pages
-
Solutions for clean Oil
6 Pages
-
Brochure for Endusers
2 Pages
-
Agritechnica Highlights 2015
32 Pages
-
Brochure Wind Energy
2 Pages
-
EXAPOR MAX 2
3 Pages
-
Guidelines
21 Pages
-
Product summary
16 Pages
-
ARGO-HYTOS program summary
16 Pages