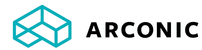
Catalog excerpts
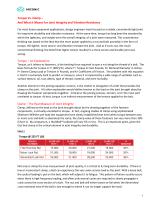
For most heavy equipment applications, design engineers have focused on a stable, consistently tight joint for long-term durability and vibration resistance. At the same time, torque has long been the standard by which the tightness, and maybe even the overall integrity, of a joint were measured. This conventional thinking was based on the idea that the more power applied to a nut and bolt assembly in the form of torque, the tighter, more secure, and vibration resistant the joint. And as it turns out, like much conventional thinking, the belief that higher torque resulted in a more secure and durable joint was wrong. Torque - An Explanation Torque, as it relates to fasteners, is the twisting force required to spin a nut along the thread of a bolt. The basic formula for torque is T= (KDP)/12, where T= Torque in Foot Pounds, D= Nominal Diameter in Inches, P= Desire Clamp Load or Tension in Pounds, and K= Coefficient of Friction. The problem with this equation is that K is extremely hard to predict or measure, since it is impacted by a wide range of variables such as surface texture, oil, rust, debris, type of thread, material, and even humidity. Another element in the joining equation, tension, is the stretch or elongation of a bolt that provides the clamp on the joint. A further explanation would define tension as the load on the joint brought about by drawing the fastener components together. Critical to the joining process, tension, is for the most part unrelated to torque. At best, torque is an indirect measurement of the tension applied to the bolt. Clamp - The Real Measure of Joint Integrity Clamp, defined as the load on the joint brought about by the drawing together of the fastener components, is virtually unrelated to torque. In fact, ongoing studies of clamp using sophisticated Skidmore-Wilhelm pre-load test equipment have clearly established that even when torque between two or more nuts and bolts is absolutely the same, the clamp value of these fasteners can vary more than 30% (Chart 1). By comparison, a HuckBolt® lockbolt will vary 5% or less. This is an important point, given the fact that clamp is the critical element in joint integrity and durability. Not only is clamp the true measurement of joint quality, it is critical to its long-term durability. If there is low or inconsistent clamp, a bolt can experience the very same service load as the joint. With a loose bolt, the cyclical loading is put on the bolt, which will subject it to fatigue. This pattern of failure usually occurs when there is high frequency loading, and often only several cycles are required to slowly propagate a crack across the cross-section of a bolt. The nut and bolt will either loosen or fail when the diminished cross-sectional area of the bolt is low enough to where it can no longer support the load.
Open the catalog to page 1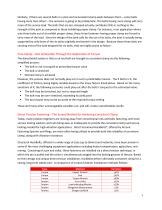
Similarly, if there are several bolts in a joint and inconsistent clamp exists between them - some bolts having more than others - the outcome is going to be problematic. The bolts having more clamp will carry more of the service load. The bolts that are less clamped actually contribute little or nothing to the strength of the joint as compared to those exhibiting proper clamp. For instance, in an application where only three bolts out of six exhibit proper clamp, those three fasteners having proper clamp are forced to carry most of the load. Since the design of the joint calls for the use...
Open the catalog to page 2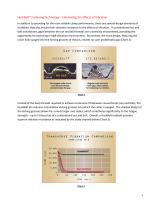
HuckBolt® Fastening Technology - Eliminating the Effects of Vibration In addition to providing for the most reliable clamp performance, there are several design elements of HuckBolts that also ensure their ultimate resistance to the effects of vibration. In conventional nut and bolt installations, gaps between the nut and bolt threads are universally encountered, providing the opportunity for loosening in high-vibration environments. By contrast, the Huck design, featuring the collar fully swaged into the locking grooves of the pin, creates no such problematic gap (Chart 2). The swaged...
Open the catalog to page 3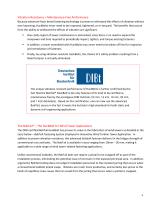
Vibration-Resistance = Maintenance-Free Performance Because advanced Huck-brand fastening technology is proven to withstand the effects of vibration without ever loosening, HuckBolts never need to be inspected, tightened, or re-torqued. The benefits that accrue from this ability to withstand the effects of vibration are significant. One costly aspect of tower maintenance is eliminated, since there is no need to expend the manpower and time required to periodically inspect, tighten, and torque existing fasteners. In addition, a tower assembled with HuckBolts may never need to be taken off...
Open the catalog to page 4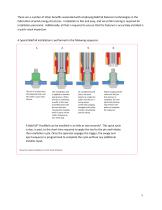
There are a number of other benefits associated with employing BobTail fasteners technologies in the fabrication of wind energy structures. Installation is fast and easy, and very little training is required for installation personnel. Additionally, all that is required to ensure that the fastener is accurately installed is a quick visual inspection. A typical BobTail installation is performed in the following sequence: 1. The pin is inserted into the prepared hole, and the collar is spun onto the pin. The pin is inserted into the prepared hole, and the collar is spun onto the pin. The...
Open the catalog to page 5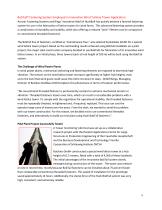
BobTail® Fastening System Employed in Innovative Wind Turbine Tower Application Arconic Fastening Systems and Rings’ innovative BobTail HuckBolt has quickly become a favored fastening system for use in the fabrication of lattice towers for wind farms. This advanced fastening system provides a combination of durability and stability, while also offering a reduced “joint” lifetime cost (in comparison to conventional threaded fasteners). The BobTail line of fasteners, certified as “maintenance-free,” was selected by Butzkies GmbH for a special wind lattice tower project. Based on the...
Open the catalog to page 6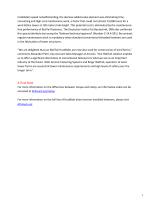
Installation speed notwithstanding, the decisive added value element was eliminating timeconsuming and high-cost maintenance work, a factor that could cost almost 15,000 Euros for a wind lattice tower at 130 meters hub height. This potential cost is eliminated by the maintenancefree performance of BobTail fasteners. The Deutsches Institut für Bautechnik, DIBt also confirmed this special attribute by issuing the ‘National technical approval’ (Number Z-14.4-591). By contrast, regular maintenance work is mandatory when standard conventional threaded fasteners are used in the fabrication of...
Open the catalog to page 7All Arconic catalogs and technical brochures
-
V964L Series
22 Pages
-
2812L Series Slam Latch
6 Pages
-
Green Energy Brochure
4 Pages
-
Magna-Bulb®
3 Pages
-
HuckForce Powerig™ Range
8 Pages
-
DIBt Newsletter
9 Pages
-
Huck 360 White Paper
5 Pages
-
Huck v. Time White Paper
4 Pages
-
Blind Fastener White Paper
5 Pages
-
Simmonds Nylstop DHE Series
2 Pages
-
Simmonds Nylstop MHT Series
2 Pages
-
Simmonds Nylstop PH Series
2 Pages
-
Simmonds Nylstop T Series
2 Pages
-
Simmonds Nylstop P Series
2 Pages
-
Simmonds Nylstop Series
3 Pages
-
Simmonds Cold Forging
2 Pages
-
Simmonds Product Brochure
2 Pages
-
Marson Threaded Inserts
7 Pages
-
Marson Value Rivets
4 Pages
-
Marson Product Brochure
44 Pages
-
SNEP Brochure
4 Pages
-
Recoil OEM
2 Pages
-
Recoil Kit for End User
2 Pages
-
Recoil Auto Aftermarket
2 Pages
-
Recoil product brochure
6 Pages
-
Camloc Handles CAM-D30
1 Pages
-
Camloc Handles CAM-D20
1 Pages
-
Camloc Handles CAM-D10
1 Pages
-
Camloc Hinges HC80
1 Pages
-
Camloc Hinges HC70
2 Pages
-
Camloc Hinges HC60
1 Pages
-
Camloc Hinges HC50
1 Pages
-
Camloc Hinges HC40
1 Pages
-
Camloc Hinges HC30
2 Pages
-
Camloc Hinges HC20
2 Pages
-
Camloc Hinges HC10
2 Pages
-
Camloc Hinges HI60
1 Pages
-
Camloc Hinges HI50
1 Pages
-
Camloc Hinges HI40
1 Pages
-
Camloc Hinges HI30
2 Pages
-
Camloc Hinges HI20
2 Pages
-
Camloc Hinges HS50
1 Pages
-
Camloc Hinges HS40
1 Pages
-
Camloc Hinges HS30
1 Pages
-
Camloc Hinges HS20
1 Pages
-
Camloc Hinges HS10
1 Pages
-
Camloc Locks CAM-L70
1 Pages
-
Camloc Locks CAM-L60
15 Pages
-
Camloc Locks CAM-L50
3 Pages
-
Camloc Locks CAM-L40
3 Pages
-
Camloc Locks CAM-L30
6 Pages
-
Camloc Locks CAM-L20
9 Pages
-
Camloc Locks CAM-L10
8 Pages
-
Camloc Locks, Hinges, Handles
75 Pages
-
Camloc Catalogue Keenserts
9 Pages
-
Camloc V18L Series
4 Pages
-
Camloc V917L Series
5 Pages
-
Camloc V951L Series
6 Pages
-
Camloc V96L Series
2 Pages
-
Camloc V95L Series
2 Pages
-
Camloc 1429L Series
5 Pages
-
Camloc CAM-PT10 Series
4 Pages
-
Camloc D4002 Series
10 Pages
-
Camloc Product Brochure
6 Pages
-
Camloc 715F Series
3 Pages
-
Camloc 991F Series
5 Pages
-
Camloc 2600-2700 Series
11 Pages
-
Camloc 50F Series (3700N)
6 Pages
-
Camloc 50F Series (900N)
6 Pages
-
Camloc 15F Series
3 Pages
-
Camloc 5F Series
4 Pages
-
Bobtail
2 Pages
-
Huck LockBolts
7 Pages
-
Magna-Lok®
10 Pages
-
FloorTight®
4 Pages
-
BOM®
4 Pages
-
Auto-Bulb?
2 Pages
-
Magna-Tite?
5 Pages
-
HuckLok?
2 Pages
-
Huck® LockBolts®
1 Pages
-
DIBt APPROVAL NEWSLETTER
6 Pages
-
244BT
22 Pages
-
255
2 Pages
-
245
2 Pages
-
241E
2 Pages
-
LH-224 Series
2 Pages
-
2025 Series
2 Pages
-
C6L®
14 Pages
-
The Huck® Product Range
7 Pages
Archived catalogs
-
BOBTAIL®_2015
8 Pages
-
HS7 Series (Huck-Spin Tool)
2 Pages
-
2480 Series
2 Pages
-
Hucktainer®
8 Pages
-
Hucktainer Encaps®
8 Pages
-
Magna-Grip®
10 Pages
-
C50L®
15 Pages
-
C120L®
18 Pages
-
BobTail®
2 Pages
-
FloorTight®
7 Pages
-
Auto-Bulb?
8 Pages