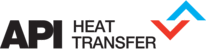
Group: API Heat Transfer
Catalog excerpts
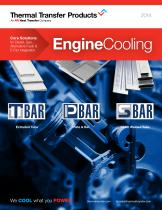
An API Heat Transfer Company Core Solutions for Diesel, Gas, Alternative Fuels & E-Fan Integration Extruded Tube EngineCooling eam Welded Tube
Open the catalog to page 1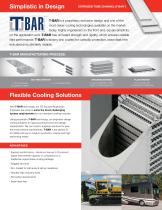
extruded tube channel (T-BAR™) T-BAR is a proprietary extrusion design and one of the most clever cooling technologies available on the market today. Highly engineered on the front end, equals simplicity on the application end. T-BAR has unrivaled strength and rigidity, which ensures reliable field performance. T-BAR is factory zinc coated for cathodic protection, seam/leak free extruded and ultimately reliable. T-BAR MANUFACTURING process: cutting station 1: Cut extruded aluminum tubing STACKING STATION 2: cut spacer bars Flexible Cooling Solutions With T-BAR technology, our OE-focused...
Open the catalog to page 2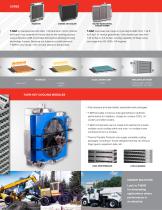
T-BAR is manufactured with Alloy 1100 aluminum micro channel and bars in our patented in-house tube-to-bar brazing process using a Nocolok CAB (Controlled Atmosphere Brazing) brazing technology furnace. Because our tubes are a solid extrusion, T-BAR is very robust—with no tube seams to fail and leak. Bolted radiator/oil cooler ComBO T-BAR core sizes can range in core height/width from 1 sq.ft. to 6 sq.ft. in various geometries. Core depths can vary from 1.25 inches to 5.5 inches. Cooling capability of these cores can range from 50-1000+ HP engines. Cool-down unit 6: Braze 1200˚ F Welding...
Open the catalog to page 3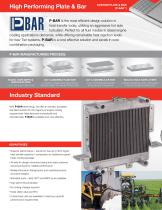
High Performing Plate & Bar custom plate & Bar (P-BAR™) P-BAR is the most efficient design solution in heat transfer today, utilizing an aggressive hot side turbulator. Perfect for all fluid medias in diesel engine cooling applications demands, while offering remarkable heat rejection levels for new Tier systems. P-BAR is a cost effective solution and excels in core combination packaging. P-BAR MANUFACTURING process: Select Core depth & Position plates 1: Cut top & bot tom pl ate Cut & Assemble Fluid Side BUILD & STACK CORE LAYERS 2: Position turbulator, side spacer bars between top and...
Open the catalog to page 4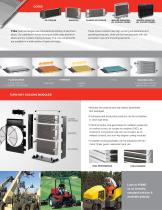
P-Bar heat exchangers are manufactured entirely of aluminum alloys. Our patented in-house brazing process uses aluminum alloys and our modern brazing furnace. The core components are available in a wide variety of types and sizes. Welded Radiator/ Oil Cooler Combo Bolted radiator/ oil cooler ComBO These robust coolers have high working temperatures and operating pressures. Units can be manufactured with any connection type and mounting elements. FLUX STATION 5: Flux core unit to prepare for brazing Welding Cell 9: Weld tank, ports & bracketry to core Turn-key cooling modules b odules are...
Open the catalog to page 5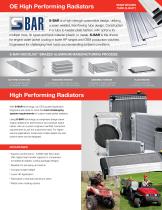
OE High Performing Radiators Seam Welded Tube (S-BAR™) S-Bar is a high strength automotive design, utilizing a seam welded, free flowing tube design. Constructed in a tube to header plate fashion, with options for multiple rows, fin types and tank material (plastic or metal). S-Bar is the choice for engine water jacket cooling in lower HP ranges and OEM production volumes. Engineered for challenging heat loads and demanding ambient conditions. S-BAR nocolok™ brazed aluminum MANUFACTURING process: CUTTING STATIONS STACKING STATION Assembly STATION FLUX STATION 1: Cut seam welded aluminum...
Open the catalog to page 6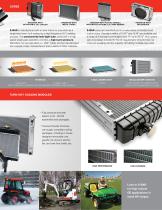
Radiator with detachable oil cooler Radiator with metal tanks S-BAR is manufactured with a close-tolerance tube that has a longitudinal seam butt-welded by a high frequency (H.F.) welding process. This permanently leak-tight tube, produced in a high speed single pass operation, provides a high burst pressure. Diameters can be held within +/- .002". Tubes can be manufactured from copper, brass, clad aluminum and a variety of other materials. furnace 5:Pre-Heat 6: Braze 1200˚ F Sent through a controlled atmospheric brazing (CAB) furnace Radiator with plastic tanks & integrated options, e.g....
Open the catalog to page 7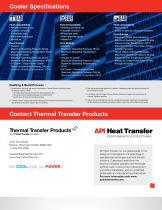
Fluid compatibility ■ Petroleum/mineral oils ■ Oil/water emulsion ■ Phosphate ester ■ Water/ethylene glycol ■ Heated air Core Ratings ■ Radiator Maximum Operating Pressure: 30 psi Maximum Operating Temperature: 250°F ■ Charge Air Cooler ^Maximum Operating Pressure: 30 psi Maximum Operating Temperature: 475°F ■ Oil Cooler / Transmission Cooler Maximum Operating Pressure: 250 psi Maximum Operating Temperature: 350°F Fluid Compatibility ■ Petroleum/mineral oils ■ Oil/water emulsion ■ Phosphate ester ■ Water/ethylene glycol ■ Heated air Core Ratings ■ Radiator Maximum Operating Pressure: 30...
Open the catalog to page 8All API Schmidt-Bretten catalogs and technical brochures
-
SCHMIDT EVAPORATORS
10 Pages
-
OCA Series
6 Pages
-
SIGMASTAR
2 Pages
-
Steam Surface Condensers.
1 Pages
-
Basco® Type 500
1 Pages
-
SCHMIDT® SIGMASHELL
8 Pages
-
BOL Series
8 Pages
-
PCR With FinSep®
1 Pages
-
Gland steam condenser
1 Pages
-
Hairpin heat exchangers
1 Pages
-
SIGMA Plate Heat Exchangers
10 Pages
-
AOC Series
4 Pages
-
AOL Series
4 Pages
-
BOL Series
6 Pages
-
Evaporators
8 Pages
-
SIGMASHELL
1 Pages
-
Basco Pipeline Aftercooler
8 Pages
-
Basco Type OP
8 Pages
-
Basco U-Tube
8 Pages
-
Basco/Whitlock Hub Design
16 Pages
-
Basco Type 500
12 Pages
Archived catalogs
-
EKT Series
2 Pages
-
BPCH Series
2 Pages
-
BPS Series
4 Pages
-
BP Series
20 Pages
-
EK Series
8 Pages
-
EC Series
6 Pages
-
CA Series
4 Pages
-
UC Series
5 Pages
-
DH Series
4 Pages
-
MA Series
4 Pages
-
OCA Series
28 Pages
-
AOC DC Fan Drive
4 Pages