Catalog excerpts
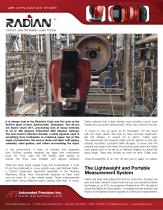
DuPont uses the Radian Laser Tracker It is always loud in the Reaction Coke and Ore area at the DuPont plant in New Johnsonville, Tennessee. Two 50-ton ore dryers churn 24-7, processing tons of heavy minerals at up to 400 degrees Fahrenheit (204 degrees Celsius). The end result is titanium dioxide, a white pigment used in everything from toothpaste to notebook paper, but at this stage of production, the area is dusty and tight, with piping, catwalks, steel girders, and rollers surrounding the dryer. In this environment, a team of workers and engineers from DuPont recently replaced the aged and overworked Dryer #2. They used the API Radian laser tracker to ensure the dryer was installed and aligned perfectly. While the dryer might appear huge and cumbersome, it must fit and be positioned in a very specific way, said Micheal Callan, a DuPont Equipment Alignment Specialist in the Rotating Machinery Group. New Johnsonville replaced its other coke and ore dryer, #1, a few weeks earlier. Those measurements were taken using traditional optics, taking more than 14 hours. Callan believed that a laser tracker could provide a much more reliable and accurate measurement, which was critical in the job. “A house is only as good as its foundation. It’s the same with the dryer vessel. We have to have accurate equipment, like the Radian, to ensure it’s in place,” Callan said. The replacement job required Callan and his partner on this job, rotating machinery consultant Mike Burgess, to know both the position and slope of the dryer. The trunions upon which the rollers were placed had to be set up at different heights to ensure the exact angle. There was virtually no room for error, Callan said. Three-thousandths of an inch off and you’re dead, he added. The Lightweight and Portable Measurement System Callan has been doing alignment jobs for more than 16 years. He saw that laser trackers would make set-up and operations faster and easier, so, in 2012, he acquired a Radian from API. He said he chose the Radian for its portability – compared to other trackers, the Radian is the lightest tracker capable of continuous measurement. Automated Precision Inc. | 15000 Johns Hopkins Drive | Rockville, MD 20850 | 06221 729 805 0 | info@apisensor.com | www.apisensor.com
Open the catalog to page 1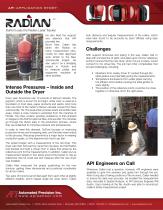
DuPont uses the Radian Laser Tracker He also liked the support and attention that API provided him. Since then, Callan has taken the Radian on many measurement jobs, mostly for roller alignment work similar to the New Johnsonville project. He also used it on a dredging project in Florida and to measure plates and equipment insulation at other facilities. Intense Pressures – Inside and Outside the Dryer took distance and angular measurements of the rollers, which were later found to be accurate by plant officials using tape measurements. Challenges With support structures and piping in the...
Open the catalog to page 2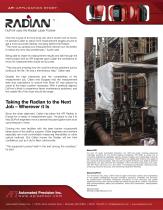
DuPont uses the Radian Laser Tracker Over the course of an hour-long call, which Austin took at home, he advised Callan to place more measurement targets around to get a more accurate reading, including behind the Radian. “The more you spread your measurement network out, the better. It makes any error less problematic,” Austin said. Being able to share his measurement results and talk through the entire project with an API engineer gave Callan the confidence to know his measurements would be accurate. “That was just amazing how he could find those problems just by looking at the file. He...
Open the catalog to page 3All API - Automated Precision Europe GmbH catalogs and technical brochures
-
DYNAMIC 9D LADAR
12 Pages
-
iScan3D
2 Pages
-
API Metrology Services
6 Pages
-
API RapidScan 2
2 Pages
-
API Active Target
1 Pages
-
API SmartTrack Sensor
1 Pages
-
Robotic Measurement Software
2 Pages
-
Machine Tool Calibration
3 Pages
Archived catalogs
-
API vProbe
1 Pages
-
BALLBAR
1 Pages
-
SPINDLE ANALYZER
1 Pages
-
Swivelcheck Datasheet
1 Pages
-
Autocollimator Datasheet
1 Pages
-
Laser Rail Tech Sheet
1 Pages