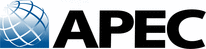

Catalog excerpts
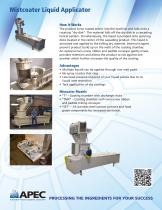
Mistcoater Liquid Applicator How it Works The product to be coated enters into the machine and falls onto a rotating “dry disk”. The material falls off the dry disk in a cascading helical pattern. Simultaneously, the liquid is pumped onto spinning disks located in the center of the cascading product. This liquid is atomized and applied to the falling dry material. Internal scrapers prevent product build up on the walls of the coating chamber. An optional twin screw ribbon and paddle conveyor gently mixes, provides retention and allows the product to rub against one another which further increases the quality of the coating. Advantages • Multiple liquids can be applied through one inlet point • No spray nozzles that clog • Less head pressure required of your liquid pumps due to no liquid inlet restriction • Tack application of dry coatings Miscoater Models • “T” – Coating chamber with discharge chute • “TMX” – Coating chamber with twin screw ribbon and paddle mixing conveyor. • “SST” – All stainless steel contact surfaces and food grade components for increased sanitation.
Open the catalog to page 1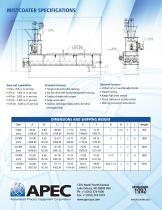
MISTCOATER SPECIFICATIONS Sizes and Capabilities • 5 Ton - 250 cu. ft. per hour • 20 Ton - 1,000 cu. ft. per hour • 40 Ton - 2,000 cu. ft. per hour • 70 Ton - 3,500 cu. ft. per hour • 120 Ton - 6,000 cu. ft. per hour Optional Features • CEMA IV or Food Grade Finish • Heat tracing • Keep full level sensor • Close tolerance construction • Mixing conveyor extensions Standard Features • Flanged inlet and outlet openings • Dry disk drive with timing belt/sprocket reduction • Coating chamber with scraper • Single access door • Stainless steel liquid disk(s) with v-belt drive and support legs...
Open the catalog to page 2All APEC catalogs and technical brochures
-
MICROINGREDIENT SYSTEMS
2 Pages
-
Ribbon Mixer
2 Pages
-
Liquid Dosing
1 Pages
-
ProFlo
2 Pages