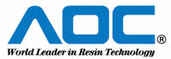
Catalog excerpts
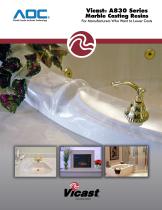
Warttt Lratlrr in Hrsitt TefftttahHjif Marble Casting Resins For Manufacturers Who Want to Lower Costs CASTING RESIN
Open the catalog to page 1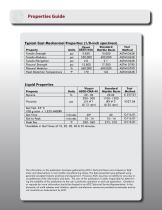
Properties Guide Typical Cast Mechanical •Available in Gel Times of 10, 20. 30, 40 & 55 minutes. The information in this publication has been gathered by AOC's Technical Team and is based on field trials, and observations in cast marble manufacturing shops. The data presented were gathered using generally accepted industry practices and equipment. However, AOC assumes no liability for accuracy or completeness of the information and data. The user of this publication is solely responsible for determin- ing the suitability of this publication to the user's particular operation or end-use...
Open the catalog to page 2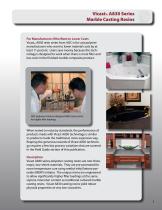
Vicast® A830 Series Marble Casting Resins For Manufacturers Who Want to Lower Costs Vicast® A830 resin series from AOC is for cast polymer manufacturers who want to lower material costs by at least 11 percent. Users save money because this technology is designed to work when there is more filler and less resin in the finished marble composite product. AOC polymer chemists designed A830 series resins for higher filler loadings. When tested to industry standards, the performance of products made with Vicast A830 technology is similar to products made the traditional, more expensive way....
Open the catalog to page 3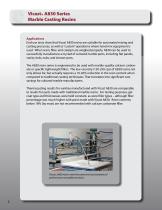
Vicast® A830 Series Marble Casting Resins Applications End-use tests show that Vicast A830 resins are suitable for automated mixing and casting processes, as well as “custom” operations where hand-mix equipment is used. When resin, filler, and catalyst are weighed properly, A830 can be used to successfully manufacture a myriad of cultured marble parts, including flat panels, vanity sinks, tubs, and shower pans. The A830 resin series is engineered to be used with marble-quality calcium carbonate or specific lightweight fillers. The low viscosity (150-250 cps) of A830 resins not only allows...
Open the catalog to page 4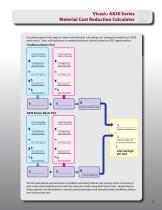
Vicast® A830 Series Material Cost Reduction Calculator Use photocopies of this page to create worksheets for calculating cost savings by using Vicast® A830 series resins. Users with questions or needing assistance should contact an AOC representative. Traditional Resin Part pounds of resin/filler matrix to fill the mold pounds of resin/filler matrix to fill the mold =$ resin cost per part filler cost per part $ Total per traditional part A830 Series Resin Part pounds of resin/filler matrix to fill the mold pounds of resin/filler matrix to fill the mold Total per A830 part lbs. of filler per...
Open the catalog to page 5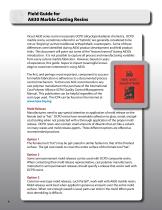
Field Guide for A830 Marble Casting Resins Vicast A830 series resins incorporate DCPD (dicyclopentadiene) chemistry. DCPD marble resins, sometimes referred to as “hybrids,” are generally considered to be not as “forgiving” as their traditional orthophthalic counterparts. Some of these differences were identified during A830 product development and field product trials. This document will point out some of the “lessons learned” during A830’s introduction. It is not possible to capture all process and manufacturing variables from every culture marble fabricator. However, based on years of...
Open the catalog to page 6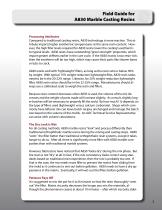
Field Guide for A830 Marble Casting Resins Processing Attributes Compared to traditional casting resins, A830 technology is more reactive. This attribute imparts higher exothermic temperatures at the same resin content. However, the high filler levels required for A830 resins lower the casting’s exotherms to typical levels. A830 resins have outstanding “green strength” properties, which impart greater stiffness earlier in the cure cycle. If the A830 matrix is too resin-rich, then the exotherm will be too high, which may cause thick parts like shower bases or tubs to crack. A830 works well...
Open the catalog to page 7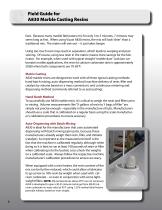
Field Guide for A830 Marble Casting Resins lizes. Because many marble fabricators mix for only 3 to 5 minutes, 7 minutes may seem long at first. When using Vicast A830 resins, the mix will look “drier” than a traditional mix. The matrix will wet-out -- it just takes longer. Using too much resin may result in separation, which leads to warping and poor veining. Of course, using less resin in the matrix means more savings for the fabricator. For example, when used with typical straight “marble dust” (calcium carbonate) marble applications, the resin to calcium carbonate ratio is approximately...
Open the catalog to page 8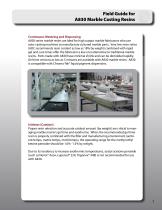
Field Guide for A830 Marble Casting Resins Continuous Metering and Dispensing A830 series marble resins are ideal for high output marble fabricators who use auto-casting machines to manufacture cultured marble parts. Very low resin ratios (AOC recommends resin content as low as 18% by weight) combined with rapid gel and cure times offer the fabricator a low cost alternative to traditional marble resins. Parts made with A830 have minimal shrink and can be demolded rapidly. Gel time versions as low as 5 minutes are available with A830 marble resins. A830 is compatible with Chroma-Tek® liquid...
Open the catalog to page 9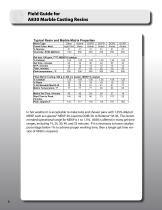
Field Guide for A830 Marble Casting Resins Typical Resin and Marble Matrix Properties Resin Type Cured Color, Neat % Styrene Viscosity, RV#2 @20rpm Ortho Light Pink 31 1140 Gel test, 100 gms, 77°F, MEKP-9 catalyst % Catalyst 1.25 Gel time, minutes 25 GTP, minutes 12 Total, minutes 37 Peak temperature , °F 290 Matrix Gel Time, minutes Start Time to Peak, minutes Peak, degrees F In hot weather it is acceptable to make tubs and shower pans with 1.25% diluted MEKP, such as Luperox® MEKP-30, Luperox DDM-30, or Butanox® M-30. The recommended operational range for MEKP is 1 to 1.5%. A830 is...
Open the catalog to page 10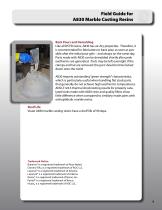
Field Guide for A830 Marble Casting Resins Back Pours and Demolding Like all DCPD resins, A830 has air-dry properties. Therefore, it is recommended for fabricators to back pour as soon as possible after the initial pour gels – and always on the same day. Parts made with A830 can be demolded shortly after peak exotherms are generated. Parts may be left overnight if the clamps and hat are removed; the part should not be locked down onto the mold. A830 imparts outstanding “green strength” characteristics, which is particularly useful when handling flat stock parts that generally do not achieve...
Open the catalog to page 11All AOC catalogs and technical brochures
-
AOC Crosslink, Volume 18
12 Pages
-
AOC Crosslink, Volume 19
12 Pages
-
Chroma-Tek Specialty Dispersions
13 Pages
-
AOC Resins Capabilities
8 Pages
-
Vibrin® Gel Coats
10 Pages
-
Resin Technology for CIPP
6 Pages
-
EcoTek® Sustainable Resins
4 Pages
-
Vipel® Resins for CIPP
8 Pages
-
CIPP RESINS
4 Pages
-
wind energy
6 Pages
-
AOC Crosslink
16 Pages
-
AOC Crosslink, Volume 16
16 Pages
-
Vipel® Guide to Fabricating
40 Pages
-
Atryl® Closed Mold Resins
4 Pages
-
Vipel® Resins for CIPP
8 Pages
-
Vipel® Vinyl Ester Brochure
6 Pages
-
Vibrin® Brochure
4 Pages
-
Hydropel® Brochure
4 Pages
-
Vipel® Corrosion Guide
32 Pages
-
AOC Capabilities Brochure
8 Pages