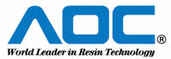
Catalog excerpts
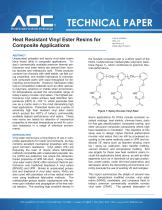
Heat Resistant Vinyl Ester Resins for Composite Applications John E. McAlvin AOC, LLC 950 Hwy 57 E Collierville, TN 38017 Unsaturated polyester and epoxy vinyl ester resins have broad utility in composite applications. Today’s commercially available premium thermal performance vinyl ester resins are derived from novolac epoxies and methacrylic acid. These products combine low viscosity with shelf stable, yet fast curing properties, and enable fabricators to manufacture composite parts with rapid throughput for demanding environments. However, fabricators often look to competitive materials such as other specialty polymers, ceramics or metals when environmental temperatures exceed the serviceable range of today’s epoxy novolac vinyl esters. The highest performance vinyl esters achieve heat distortion temperatures (HDT) of ~165 °C, which precludes their use as a matrix resin in the most demanding high heat applications. Presented herein are a series of extremely high heat resistant vinyl ester resins which exceed the HDT’s of today’s commercially available highest performance vinyl esters. These new resins are tested for retention of mechanical properties at elevated temperature as well for corrosion resistance in a range of chemical environments. INTRODUCTION Vinyl ester resins have a long history of use in composite applications for harsh environments, as they combine excellent mechanical properties with very good corrosion resistance. Vinyl esters (VE) are frequently the resin of choice where fabrication methods compatible with unsaturated polyester resins (UPR) are preferred, but where the aforementioned properties of UPR fall short. Epoxy novolac vinyl ester resins (NVE) offer improved thermal performance over traditional bisphenol A vinyl esters (BPAVE) and UPR. Similar to unsaturated polyesters and bisphenol A vinyl ester resins, NVEs are also cured with peroxides via a free radical mechanism using traditional fabrication methods. The methacrylate groups readily copolymerize with styrene upon initiation and propagation of the free radical reaction. The resulting high crosslink density in the finished composite part is a direct result of the NVEs multifunctional methacrylate polymeric backbone (figure 1), which contributes to premium thermal performance. Figure 1: Epoxy Novolac Vinyl Ester Some applications for NVEs include corrosion resistant coatings, heat shields, chimney liners, parts for flue gas desulfurization, composite tooling, and other structural composite components where high heat resistance is mandated. The objective of this study was to design higher thermal performance novolac vinyl esters that can still be processed according to the same methods used in UPR and traditional VE resins such as filament winding, hand lay / spray up, pultrusion, resin transfer molding, vacuum infusion, and compression molding. End use targets for these new heat resistant resins include the applications listed above, as well as other segments such as in downhole oil and gas production, power plants, under the hood automotive, and aerospace where the demanding environments currently preclude the use of existing VE technologies. This report summarizes the details of several new higher temperature modified novolac vinyl ester resins (MNVE) candidates, and compares them to today’s premium commercially available novolac vinyl ester (CNVE). The general descri
Open the catalog to page 1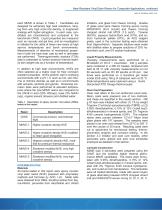
Heat Resistant Vinyl Ester Resins for Composite Applications, continued John E. McAlvin, AOC, LLC each MNVE is shown in Table 1. Candidates are designed for extremely high heat resistance, ranging from very high cross link density, to toughened analogs with higher elongation. In each case, candidates are characterized and compared to the benchmark CNVE. Liquid properties are measured such as viscosity and gel time, and an investigation is initiated for the utility of these new resins at high service temperatures and harsh environments. Measurements of retention of mechanical properties in...
Open the catalog to page 2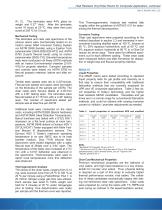
Heat Resistant Vinyl Ester Resins for Composite Applications, continued John E. McAlvin, AOC, LLC W, C). The laminates were 44% glass by weight and 0.27” thick. After the laminates cured 16 hours at 25 ºC, they were then post cured at 205 ºC for 5 hours. Mechanical Testing The laminates and clear cast specimens of the various resins were mechanically tested on an Instron series 5984 Universal Testing System via ASTM D638 (tensile) using a Epsilon Tech extensometer [3542-0200-025-HT2] and ASTM D790 (3-point flexural bend) using an Instron extensometer [2630-110]. Elevated temperature tests...
Open the catalog to page 3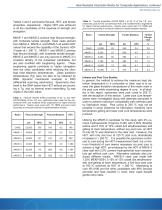
Heat Resistant Vinyl Ester Resins for Composite Applications, continued John McAlvin, AOC, LLC Tables 3 and 4 summarize flexural, HDT, and tensile properties, respectively. Higher HDT was achieved in all the candidates at the expense of strength and elongation. Table 4. Tensile properties (ASTM D638 ) at 25 °C of the 1/8” nonreinforced casts for the conventional NVE and modified NVEs engineered for higher thermal performance. Resins were cured with 1% TBPB and post cured according to schedule outlined in experimentation section. Resin MNVE-1 and MNVE-2 achieve high flexural strength, with...
Open the catalog to page 4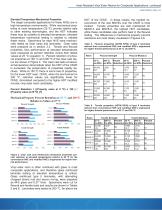
Heat Resistant Vinyl Ester Resins for Composite Applications, continued John McAlvin, AOC, LLC Elevated Temperature Mechanical Properties The target composite applications for these NVEs are in high temperature environments. While mechanical properties at room temperature (25 ºC) provide relative data to other existing technologies, and the HDT indicates these may be suitable at elevated temperature, elevated temperature mechanical testing is needed to validate these resins. Specimens for each NVE were mechanically tested as clear casts and laminates. Clear casts were prepared as in section...
Open the catalog to page 5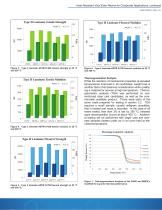
Heat Resistant Vinyl Ester Resins for Composite Applications, continued Type II Laminate Tensile Strength Figure 3. Type 2 laminate ASTM D-638 tensile strength at 25 °C Type II Laminate Flexural Modulus Figure 6. Type 2 laminate ASTM D-790 flexural modulus at 25 °C Type II Laminate Tensile Modulus Figure 4. Type 2 laminate ASTM D-638 tensile modulus at 25 °C Type II Laminate Flexural Strength Figure 5. Type 2 laminate ASTM D-790 flexural strength at 25 °C Thermogravimetric Analysis While the retention of mechanical properties at elevated temperatures improved in all candidates, weight loss...
Open the catalog to page 6All AOC catalogs and technical brochures
-
AOC Crosslink, Volume 18
12 Pages
-
AOC Crosslink, Volume 19
12 Pages
-
Chroma-Tek Specialty Dispersions
13 Pages
-
AOC Resins Capabilities
8 Pages
-
Vibrin® Gel Coats
10 Pages
-
Resin Technology for CIPP
6 Pages
-
EcoTek® Sustainable Resins
4 Pages
-
Vipel® Resins for CIPP
8 Pages
-
CIPP RESINS
4 Pages
-
wind energy
6 Pages
-
AOC Crosslink
16 Pages
-
AOC Crosslink, Volume 16
16 Pages
-
Vipel® Guide to Fabricating
40 Pages
-
Atryl® Closed Mold Resins
4 Pages
-
Vipel® Resins for CIPP
8 Pages
-
Vipel® Vinyl Ester Brochure
6 Pages
-
Vibrin® Brochure
4 Pages
-
Hydropel® Brochure
4 Pages
-
Vipel® Corrosion Guide
32 Pages
-
AOC Capabilities Brochure
8 Pages