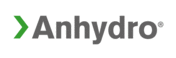

Catalog excerpts
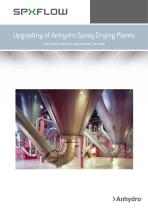
Upgrading of Anhydro Spray Drying Plants F O R E X T R A CA PAC I T Y A N D E N E R GY S AV I N G S
Open the catalog to page 1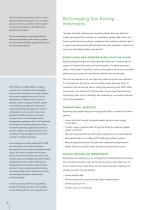
SPX Flow Technology Danmark A/S is an international engineering company with a consistent goal to provide our customers with the optimal processing technology and the highest plant Re-Energizing Your Existing Investments performance standards. The dairy and food industries are competing harder than ever before to We have specialized in supplying the optimal design and engineering with respect to production performance, flexibility, energy efficiency and environmental protection. sustain and expand their positions in competitive markets. Many dairy and food manufacturers are looking to...
Open the catalog to page 2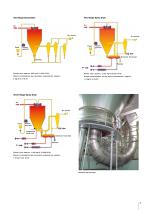
One-Stage Spray Dryer Two-Stage Spray Dryer Three-Stage Spray Dryer Integrated fluid bed External fluid bed
Open the catalog to page 3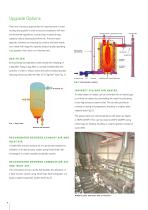
Upgrade Options There are numerous opportunities for improvements in most existing drying plant in order to ensure compliance with new environmental regulations, recover heat, increase drying capacity, reduce cleaning downtime etc. The best result depends, however, on choosing the solution that best meets your needs with regard to capacity, product quality, operating cost, payback time, return on investment etc. BAG F I LT E R Environmental considerations often dictate the installing of a bag filter. Today, a bag filter is normally installed after the cyclones in order to reduce costs and...
Open the catalog to page 4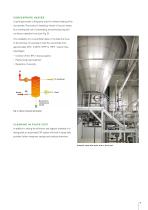
C O N C E N T R AT E H E AT E R A spiral type heater is frequently used for indirect heating of the concentrate. The product is heated by means of vacuum steam, thus avoiding the risk of overheating, and achieving long and continuous operation time. (see Fig. 3). The installation of a concentrate heater in the feed line close to the atomiser, for example to heat the concentrate from approximately 45°C to 80°C (1 13°F to 176°F , means three advantages: • Increase of 8 to 9% in drying capacity • Pasteurising heat treatment • Reduction of viscosity Ai r Barometric condensate outlet Fig. 3:...
Open the catalog to page 5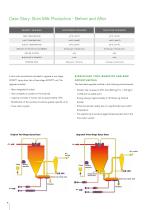
Case Story: Skim Milk Production - Before and After P R O D U CT : S K I M M I L K A skim milk manufacturer decided to upgrade a two-stage 2CSD77 spray dryer into a three-stage 3CSD77 unit. The upgrade included: The described upgrade resulted in the following enhancements: • Powder rate increase of 37% from 800 kg/h to 1,100 kg/h • New complete air system for the fluid bed • Capacity increase of suction fan by approximately 10% • Energy saving if approximately 0.15 kW per kg finished • Modification of the cyclones to achieve greater quantity of air • Fines return system powder • Enhanced...
Open the catalog to page 6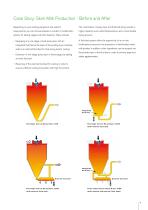
Case Story: Skim Milk Production - Before and After Depending on your existing equipment and specific The combination of spray dryer and fluid bed drying results in requirements, you can choose between a number of modification higher capacity, lower outlet temperatures, and a more flexible options for adding stages and other features. These include: drying process. • Equipping of a one-stage conical spray dryer with an A fluid bed system offers the opportunity of an on-line integrated fluid bed at the base of the existing dryer chamber, lecithination process for the production of...
Open the catalog to page 7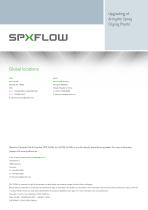
Upgrading of Anhydro Spray Drying Plants Peoples Republic of China Based in Charlotte, North Carolina, SPX FLOW, Inc. (NYSE: FLOW) is a multi-industry manufacturing leader. For more information, please visit www.spxflow.com S P X F LOW T E C H N O LO GY DA N M A R K A / S SPX FLOW, Inc. reserves the right to incorporate our latest design and material changes without notice or obligation. Design features, materials of construction and dimensional data, as described in this bulletin, are provided for your information only and should not be relied upon unless confirmed in writing. Please...
Open the catalog to page 8All Anhydro catalogs and technical brochures
-
Anhydro Fluid Bed Technologies
12 Pages
-
Anhydro Dosing System
2 Pages
-
Anhydro Evaporation Process
8 Pages
-
FOOD+BEVERAGE
4 Pages