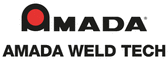
Catalog excerpts
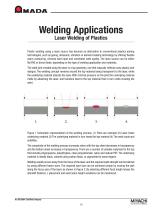
Welding Applications Laser Welding of Plastics Plastic welding using a laser source has become an alternative to conventional plastics joining technologies, such as gluing, ultrasonic, vibration or element heating technology by offering flexible seam contouring, minimal heat input and consistent weld quality. The laser source can be either Nd:YAG or direct diode, depending on the type of welding application and materials. The weld joint created using the laser is a lap geometry, one that naturally reflects many plastic joint designs. The welding concept revolves around the top material being transparent to the laser, while the underlying material absorbs the laser. With minimal pressure on the joint the underlying material melts by absorbing the laser, and transfers heat to the top material that in turn melts creating the weld. Figure 1 Schematic representation of the welding process. (1) Parts are clamped (2) Laser heats underlying material (3) The underlying material in turn heats the top material (4) The weld cools and solidifies. The complexity of the welding process increases when with the top sheet decreases in transparency and the bottom sheet increases in transparency. There are a number of suitable materials for the top that include polypropylene, polyethylene, clear polycarbonate, nylon and natural PET. The underlying material is ideally black, colored using carbon black, or pigmented to some degree. Welding usually occurs away from the focus of the laser, and the required weld strength can be tailored by using different beam sizes. The required spot size can be achieved simply by moving the part along the focus axis of the laser, as shown in Figure 2. By selecting different focal length lenses the standoff distance, z placement and weld seam height variations can be maximized.
Open the catalog to page 1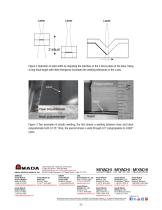
Figure 2 Selection of weld width by adjusting the interface in the Z focus plane of the laser. Using a long focal length with little divergence increases the welding tolerances in the z axis. Figure 3 Two examples of plastic welding; the first shows a welding between clear and black polycarbonate both 0.125” thick, the second shows a weld through 0.5” polypropylene to 0.062” nylon. 1820 S. Myrtle Ave. • Monrovia, CA 91016 US T: (626) 303-5676 • F: (626) 358-8048 info@amadamiyachi.com • www.amadamiyachi.com ISO 9001 Certified Company • 24/7 Repair Service: 1-866-751-7378 AMERICAS Amada...
Open the catalog to page 2