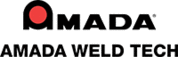

Catalog excerpts
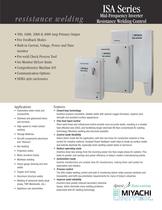
Applications • Automotive sheet metal and components • Stainless and galvanized doors and furniture • High-speed bi-metal contact welding • Storage Batteries • Aircraft components (aluminum and titanium) • Nut welding • Projection welds • Motor armature fusing • Markless welding • Heavy gauge shelving and wire welds • Copper wire fusing • Aluminum structure welds • Welding of advanced steels (dual phase, TRIP, Martensitic, etc.) • Appliance sub-assemblies Features • Closed loop technology Inverters produce consistent, reliable welds with optimal nugget formation, superior joint strength and excellent surface appearance. • Fine heat input control Short weld times and millisecond control provide more accurate welds, resulting in a smaller heat affected zone (HAZ), and facilitating longer electrode life than conventional AC welding technology. Markless welding also becomes possible. • Control mode flexibility Select which mode fits the application, with fast rise times for conductive material or finer control for resistive material. Constant Power feedback mode helps to break up surface oxides and extends electrode life, especially when welding coated steels or aluminum. • Reduce operating costs Inverters draw less energy from the incoming power line than single phase AC welders. This leads to greater cost savings and power efficiency in today’s modern manufacturing plants. • Automation-ready Inverter transformers are smaller than AC transformers, making them well suited for automation and robotics. • Process control The ISA’s stable welding control and built-in monitoring deliver wider process windows and traceability, and fulfill documentation requirements for many of today’s industries. • Improve weld reliability Inverters have greatly reduced secondary inductive losses, which eliminate many welding problems associated with AC welding technology. resistance welding ISA Series Mid-Frequency Inverter Resistance Welding Control • 500, 1000, 2000 & 4000 Amp Primary Output • Five Feedback Modes • Built-in Current, Voltage, Power and Time monitor • Pre-weld Check Process Tool • Set Monitor Hi/Low limits • Comprehensive Machine I/O • Communication Options • NEMA style enclosures
Open the catalog to page 1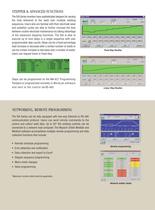
STEPPER & ADVANCED FUNCTIONS NETWORKING, REMOTE PROGRAMMING The ISA Series can be fully equipped with two-way Ethernet or RS-485 communication protocol. Users can send remote commands to the control and collect weld data. Up to 30* ISA welding controls can be connected to a network host computer. The Miyachi Unitek Weldlab and Weldnet software accomplishes multiple remote programming and data collection functions that include: • Remote schedule programming • Error detection and notification • Data collection and export to Excel® • Stepper sequence programming • Menu mode changes • Valve...
Open the catalog to page 2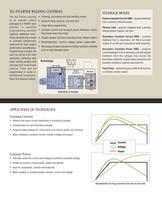
ISA INVERTER WELDING CONTROLS APPLICATION OF TECHNOLOGY • Chaining, successive and spot welding modes • Squeeze delay, squeeze, cool and hold • Forge delay programming • Constant current and constant power feedback modes, fixed pulse open loop mode • Flexible stepper functions (including linear stepper option) • Monitoring limits – current / voltage / power / pulse width • Nine programmable impulses for temper sensitive materials such as high strength steels The ISA Series consists of an inverter control packaged in a “NEMA” style cabinet, a versat i l e programming pendant (optional...
Open the catalog to page 3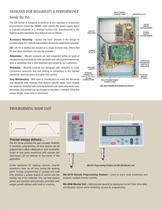
DESIGNED FOR RELIABILITY & PERFORMANCE Inside the ISA…. The ISA Series is designed to perform in the harshest of production environments. Inside the “NEMA” style cabinet the power supply layout is logically designed in a modular fashion and manufactured to the highest quality standards. Key features are as follows: Accessory Mounting – Space has been allowed in the design to accommodate PLC controls and ancillary devices for automation purposes. I/O – All I/O is labeled and located on a single terminal strip. Device Net I/O and other interfaces can also be provided. Robustness – Miyachi...
Open the catalog to page 4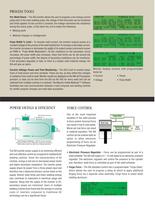
Pre-Weld Check – The ISA inverter allows the user to program a low energy current pulse prior to the main welding pulse; the voltage of this first pulse can be monitored and limits applied. As the current is constant, the voltage represents the resistance during the check pulse. Limits allow the unit to detect the following: • Missing parts • Material changes or misalignment Pulse Width % Limit – To develop weld current, the inverter outputs pulses of a constant voltage to the primary of the weld transformer.To increase or decrease current, the inverter increases or decreases the width of...
Open the catalog to page 5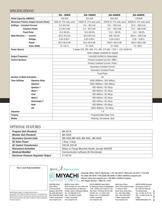
ISA - 500CR ISA-1000CR ISA-2000CR ISA-4000CR Rated Capacity (480VAC) 182 kVA 325 kVA 650 kVA 1250kVA Maximum Primary Output Current (Peak) 500A @ 15% duty cycle 1000A @ 12% duty cycle 2000A @ 12% duty cycle 4000A @ 12% duty cycle Settings – Constant Current 2.0-40.0 kA 4.0 – 80.0 kA 8.0 – 160.0 kA 32.0 – 200.0 kA Constant Power 2.0-60.0 kW 4.0 – 80.0 kW 8.0 – 160.0 kW 15.0 – 300.0 kW Fixed Pulse 10.0-99.9% 10.0-99.9% 10.0 – 99.9% 10.0 – 99.9% Weld Monitors – Current 00.0-40.0 kA 00.0-80.0 kA 000-160 kA 000.0 – 200.0 kA Voltage 0.00-9.99 V 0.00-9.99 V 0.00-9.99 V 0.00 – 9.99 V Power...
Open the catalog to page 6All AMADA WELD TECH Inc. catalogs and technical brochures
-
TC-W100A
2 Pages
-
MEA-100B
2 Pages
-
MIB-300A/600A
2 Pages
-
CD-A125A CD-A300A CD-A1000A
2 Pages
-
Rotary Dial Index Systems
2 Pages
-
AMADA WELD TECH
24 Pages
-
HF-2700A / HF-2500A
4 Pages
-
CD-V Series
2 Pages
-
MD-A10000A/ MD-B5000A
2 Pages
-
ISQ Series
3 Pages
-
IPB-5000A-MU
2 Pages
-
MFP60 for aws3
2 Pages
-
MFP25 FRO AWS3
2 Pages
-
Series 320
2 Pages
-
newhorizon
3 Pages
-
F120, F160, FD120
4 Pages
-
KN-II Series
2 Pages
-
MH Weld Head Range
4 Pages
-
Accessries
9 Pages
-
Laser Microfabrication
2 Pages
-
ML-5120A
2 Pages
-
Systems
16 Pages
-
ML-5120
2 Pages
-
DC29-UB29-UB29A
4 Pages
-
LF Series Lasers
2 Pages
-
SA2200 Dual Oven
2 Pages
-
Laser Tube Cutting Systems
2 Pages
-
Heat Staking
2 Pages
-
Seam Laser Welder - 150W
2 Pages
-
Systems Datasheet
16 Pages
-
AX5000 Glovebox
2 Pages
-
MX2000 Glovebox
2 Pages
-
Benchmark AF8500 / AF 1250
2 Pages
-
Pulsed-Heat Hot-Bar
10 Pages
-
Benchmark SM8500
2 Pages
-
vacuum bakeout oven
2 Pages
-
Interposer Module
2 Pages
-
UV Laser Marking Systems
2 Pages
-
CO2 Laser Marking Systems
2 Pages
-
Fiber Laser Micro Welders
2 Pages
-
Sigma Laser Tube Cutter
2 Pages
-
Laser Marker Motion
2 Pages
-
Laser Welding Gloveboxes
2 Pages
-
Thermocouple Welder - TCW
2 Pages
-
Laser Accessories
7 Pages
-
Alpha Series
2 Pages
-
MX-2000 Glovebox Technical
2 Pages
-
AX-5000 Glovebox
2 Pages
-
Benchmark Accessories
9 Pages
-
Thin Line Weld Heads
8 Pages
-
Uniflow 4
2 Pages
-
Pulsar
2 Pages
-
LMC1 Laser Marker Motion
2 Pages
-
LW300-600A
2 Pages
-
LW50A-70-150A
2 Pages
-
LW5-15-25A
2 Pages
-
LF Series
2 Pages
-
50 Series Weld Heads
4 Pages
-
MH Series Weld Heads
4 Pages
-
MG3
12 Pages
-
MG3 Hot Bar Monitoring
3 Pages
-
Sarcon and Kapton Modules
2 Pages
-
Thin-line
8 Pages
-
IS series
2 Pages
-
ISB-300 A
2 Pages
-
Accessoires
9 Pages
-
DC25, UB25
4 Pages
-
Fine Laser Cutting Datasheet
4 Pages
-
laser markers and marker systems
16 Pages
-
Bonding Heads
2 Pages
-
MG3 UNIQUE PROCESS MONITORING
12 Pages
-
Process Calibration Tools
2 Pages
-
LaserCuttingSystems_Cut
4 Pages
-
Pincer Weld Head - MFP-Z
3 Pages