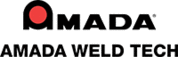

Catalog excerpts
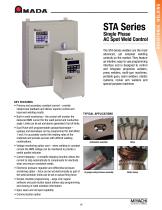
Single Phase AC Spot Weld Control The STA-Series welders are the most advanced, yet simplest welding controls on the market. They feature an intuitive, easy-to-use programming interface and is designed to control and integrate projection welders, press welders, multi-gun machines, portable guns, seam welders, robotic systems, rocker arm welders and special purpose machines. KEY FEATURES • Primary and secondary constant current – provide closed-loop feedback and deliver superior control and improved welding results. • Built-in weld monitoring – the control will monitor the delivered RMS current for the weld period and conduction angle. Limits can be set and alarms generated if out of limits. • Dual Pulse with programmable upslope/downslope – upslope and downslope can be programmed for both Weld 1 and 2 to accurately control the heating rates of the materials and provide success with difficult welding combinations. • Voltage monitoring option card – when welding in constant current the RMS voltage can be monitored to provide a useful quality indicator. • Current stepping – a versatile stepping function allows the current to step automatically to compensate for electrode wear and ensure consistent welds. • Electronic pressure regulator and differential pressure monitoring option – force can be set electronically as part of the weld schedule, limits can be set on actual firing force. • Simple, intuitive programming – large LCD, logical software and push button layout allows easy programming and viewing of weld schedule information. • Spot, seam and roll spot capability • Communication option TYPICAL APPLICATIONS Automotive assembly 10 gauge wiring harness assembly Motor fusing RESISTANCE WELDING
Open the catalog to page 1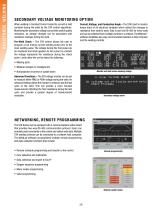
SECONDARY VOLTAGE MONITORING OPTION When welding in Constant Current mode the current is held constant during the weld by the STA control algorithms. Monitoring the secondary voltage can provide useful quality indicators, as voltage changes can be associated with resistance changes during the weld. Pre-Weld Check - The STA control allows the user to program a low energy current welding pulse prior to the main welding pulse. The voltage during this first pulse can be monitored and limits applied. As the current is constant the voltage represents the resistance during the check pulse. Limits...
Open the catalog to page 2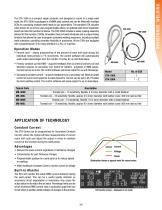
Operation Modes • Percent heat – allows programming of the percent of each half cycle during the individual weld periods in 1% increments. The control software will automatically scale output percentages over the number of cycles for up and downslope. • Primary constant current RMS – acquires feedback from an internal primary coil and therefore requires no secondary coil. Useful for robotics, programs in RMS values. Current can be set in kA. The control software will scale output for up and downslope. • Secondary constant current – acquires feedback from a secondary coil. Most accurate...
Open the catalog to page 3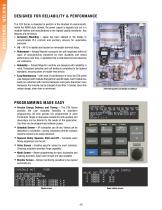
DESIGNED FOR RELIABILITY & PERFORMANCE The STA Series is designed to perform in the harshest of environments. Inside the NEMA style cabinet, the power supply is logically laid out in a modular fashion and manufactured to the highest quality standards. Key • Accessory Mounting - space has been allowed in the design to accommodate PLC controls and ancillary devices for automation • I/O - All I/O is labeled and located on removable terminal strips. • Robustness - Amada Miyachi's products are well respected within all types of manufacturing industries for their durability and robust performance...
Open the catalog to page 4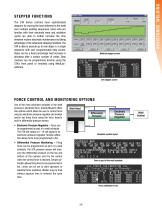
STEPPER FUNCTIONS The STA Series controls have sophisticated steppers for varying the heat delivered to the weld over multiple welding sequences. Users who are familiar with their electrode wear and oxidation cycles are able to further increase the time between routine electrode maintenance by taking advantage of the advanced stepping functions. The STA is able to execute up to nine steps in a single sequence with user programmable step counts. Steps can be a fixed percentage heat increase or decrease after a certain number of welds. Step routines can be programmed directly using the STAs...
Open the catalog to page 5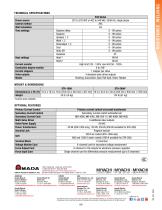
RESISTANCE WELDING TECHNICAL SPECIFICATIONS Power source Control method Weld schedules Time settings Heat settings Current monitor Conduction degree monitor Current steppers Valve outputs Modes STA Series 201 to 270 VAC or 402 to 540 VAC, 50/60 Hz, single phase AVC 64 Squeeze delay 0 - 99 cycles Squeeze 0 - 99 cycles Upslope 1, 2 0 - 99 cycles Weld 1, 2 0 - 99 cycles Downslope 1, 2 0 - 99 cycles Cool 0 - 99 cycles Hold, Off 0 - 99 cycles Impulses 25 Heat 1 80 kA Heat 2 80 kA High limit 100 - 150%, low limit 50 - 100% 0 to 180° 1 stepper per valve 4 standard valve driver outputs Chaining,...
Open the catalog to page 6All AMADA WELD TECH Inc. catalogs and technical brochures
-
TC-W100A
2 Pages
-
MEA-100B
2 Pages
-
MIB-300A/600A
2 Pages
-
CD-A125A CD-A300A CD-A1000A
2 Pages
-
Rotary Dial Index Systems
2 Pages
-
AMADA WELD TECH
24 Pages
-
HF-2700A / HF-2500A
4 Pages
-
CD-V Series
2 Pages
-
MD-A10000A/ MD-B5000A
2 Pages
-
ISQ Series
3 Pages
-
IPB-5000A-MU
2 Pages
-
MFP60 for aws3
2 Pages
-
MFP25 FRO AWS3
2 Pages
-
Series 320
2 Pages
-
newhorizon
3 Pages
-
F120, F160, FD120
4 Pages
-
KN-II Series
2 Pages
-
MH Weld Head Range
4 Pages
-
Accessries
9 Pages
-
Laser Microfabrication
2 Pages
-
ML-5120A
2 Pages
-
Systems
16 Pages
-
ML-5120
2 Pages
-
DC29-UB29-UB29A
4 Pages
-
LF Series Lasers
2 Pages
-
SA2200 Dual Oven
2 Pages
-
Laser Tube Cutting Systems
2 Pages
-
Heat Staking
2 Pages
-
Seam Laser Welder - 150W
2 Pages
-
Systems Datasheet
16 Pages
-
AX5000 Glovebox
2 Pages
-
MX2000 Glovebox
2 Pages
-
Benchmark AF8500 / AF 1250
2 Pages
-
Pulsed-Heat Hot-Bar
10 Pages
-
Benchmark SM8500
2 Pages
-
vacuum bakeout oven
2 Pages
-
Interposer Module
2 Pages
-
UV Laser Marking Systems
2 Pages
-
CO2 Laser Marking Systems
2 Pages
-
Fiber Laser Micro Welders
2 Pages
-
Sigma Laser Tube Cutter
2 Pages
-
Laser Marker Motion
2 Pages
-
Laser Welding Gloveboxes
2 Pages
-
Thermocouple Welder - TCW
2 Pages
-
Laser Accessories
7 Pages
-
Alpha Series
2 Pages
-
MX-2000 Glovebox Technical
2 Pages
-
AX-5000 Glovebox
2 Pages
-
Benchmark Accessories
9 Pages
-
Thin Line Weld Heads
8 Pages
-
Uniflow 4
2 Pages
-
Pulsar
2 Pages
-
LMC1 Laser Marker Motion
2 Pages
-
LW300-600A
2 Pages
-
LW50A-70-150A
2 Pages
-
LW5-15-25A
2 Pages
-
LF Series
2 Pages
-
50 Series Weld Heads
4 Pages
-
MH Series Weld Heads
4 Pages
-
MG3
12 Pages
-
MG3 Hot Bar Monitoring
3 Pages
-
Sarcon and Kapton Modules
2 Pages
-
Thin-line
8 Pages
-
IS series
2 Pages
-
ISB-300 A
2 Pages
-
Accessoires
9 Pages
-
DC25, UB25
4 Pages
-
Fine Laser Cutting Datasheet
4 Pages
-
laser markers and marker systems
16 Pages
-
Bonding Heads
2 Pages
-
MG3 UNIQUE PROCESS MONITORING
12 Pages
-
Process Calibration Tools
2 Pages
-
LaserCuttingSystems_Cut
4 Pages
-
Pincer Weld Head - MFP-Z
3 Pages