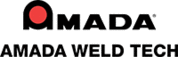

Catalog excerpts
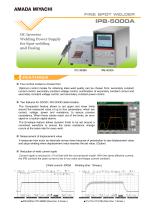
FINE SPOT WELDER IPB-5000A DC Inverter Welding Power Supply for Spot welding and Fusing FEATURES ■ Four control modes to choose from Optimum control modes for obtaining ideal weld quality can be chosen from; secondary constant current control, secondary constant voltage control, combination of secondary constant current and secondary constant voltage control, and secondary constant power control. ■ Two features for GOOD / NO GOOD determination The Comparator feature allows to set upper and lower limits around the measured value of up to four parameters; which are current, voltage, power and resistance, to assure process consistency. When those values reach out of the limits, an error signal or a caution signal alarms. The Envelope feature allows dynamic limits to be set around a monitored waveform to ensure the same resistance change occurs at the same rate for every weld. ■ Measurement of displacement value It measures how much an electrode moves down because of penetration to see displacement value and stops welding when displacement value reaches the set value. (Option) ■ Reduction of weld current ripple Current ripple is reduced to 1/3 of that with the conventional model. With the same effective current, the IPB controls the peak current to be in low value and keeps current constant. [ Weld current: 4000A
Open the catalog to page 1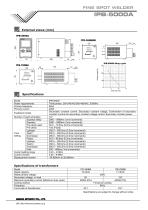
FINE SPOT WELDER Specifications Model Power requirements Primary frequency Primary current Feedback modes Number of weld schedules Squeeze delay Squeeze Pre-check weld Pre-check Upslope Time Weld 1 setting Downslope Pause Upslope Weld 2 Downslope Hold Current setting range Current monitor Displacement monitor Specifications of transformers Model Rated capacity Rated primary voltage Secondary voltage, no load Maximum secondary current (Maximum duty cycle) Cooling method Frequency Turns ratio of transformers Specifications are subject to change without notice.
Open the catalog to page 2All AMADA WELD TECH Inc. catalogs and technical brochures
-
TC-W100A
2 Pages
-
MEA-100B
2 Pages
-
MIB-300A/600A
2 Pages
-
CD-A125A CD-A300A CD-A1000A
2 Pages
-
Rotary Dial Index Systems
2 Pages
-
AMADA WELD TECH
24 Pages
-
HF-2700A / HF-2500A
4 Pages
-
CD-V Series
2 Pages
-
MD-A10000A/ MD-B5000A
2 Pages
-
ISQ Series
3 Pages
-
IPB-5000A-MU
2 Pages
-
MFP60 for aws3
2 Pages
-
MFP25 FRO AWS3
2 Pages
-
Series 320
2 Pages
-
newhorizon
3 Pages
-
F120, F160, FD120
4 Pages
-
KN-II Series
2 Pages
-
MH Weld Head Range
4 Pages
-
Accessries
9 Pages
-
Laser Microfabrication
2 Pages
-
ML-5120A
2 Pages
-
Systems
16 Pages
-
ML-5120
2 Pages
-
DC29-UB29-UB29A
4 Pages
-
LF Series Lasers
2 Pages
-
SA2200 Dual Oven
2 Pages
-
Laser Tube Cutting Systems
2 Pages
-
Heat Staking
2 Pages
-
Seam Laser Welder - 150W
2 Pages
-
Systems Datasheet
16 Pages
-
AX5000 Glovebox
2 Pages
-
MX2000 Glovebox
2 Pages
-
Benchmark AF8500 / AF 1250
2 Pages
-
Pulsed-Heat Hot-Bar
10 Pages
-
Benchmark SM8500
2 Pages
-
vacuum bakeout oven
2 Pages
-
Interposer Module
2 Pages
-
UV Laser Marking Systems
2 Pages
-
CO2 Laser Marking Systems
2 Pages
-
Fiber Laser Micro Welders
2 Pages
-
Sigma Laser Tube Cutter
2 Pages
-
Laser Marker Motion
2 Pages
-
Laser Welding Gloveboxes
2 Pages
-
Thermocouple Welder - TCW
2 Pages
-
Laser Accessories
7 Pages
-
Alpha Series
2 Pages
-
MX-2000 Glovebox Technical
2 Pages
-
AX-5000 Glovebox
2 Pages
-
Benchmark Accessories
9 Pages
-
Thin Line Weld Heads
8 Pages
-
Uniflow 4
2 Pages
-
Pulsar
2 Pages
-
LMC1 Laser Marker Motion
2 Pages
-
LW300-600A
2 Pages
-
LW50A-70-150A
2 Pages
-
LW5-15-25A
2 Pages
-
LF Series
2 Pages
-
50 Series Weld Heads
4 Pages
-
MH Series Weld Heads
4 Pages
-
MG3
12 Pages
-
MG3 Hot Bar Monitoring
3 Pages
-
Sarcon and Kapton Modules
2 Pages
-
Thin-line
8 Pages
-
IS series
2 Pages
-
ISB-300 A
2 Pages
-
Accessoires
9 Pages
-
DC25, UB25
4 Pages
-
Fine Laser Cutting Datasheet
4 Pages
-
laser markers and marker systems
16 Pages
-
Bonding Heads
2 Pages
-
MG3 UNIQUE PROCESS MONITORING
12 Pages
-
Process Calibration Tools
2 Pages
-
LaserCuttingSystems_Cut
4 Pages
-
Pincer Weld Head - MFP-Z
3 Pages