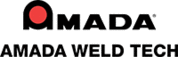

Catalog excerpts
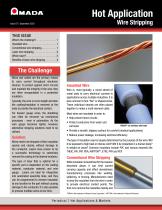
Hot Application Wire Stripping This issue What’s the challenge? . . . . . . . . . . . . . . . Insulated wire. . . . . . . . . . . . . . . . . . . . . Conventional wire stripping . . . . . . . . . . . Laser wire stripping . . . . . . . . . . . . . . . . Which laser?. . . . . . . . . . . . . . . . . . . . . . Benefits of laser wire stripping. . . . . . . . The Challenge Wires and cables are the primary means to carry current throughout electronic devices. To protect against short circuits and maintain the integrity of the wire, they are often encapsulated in a protective insulation. Typically, the wire is cut to length and then the coating/insulation is removed at the ends to provide the electrical contact. For heavier gauge wires, the sheathing can often be removed via mechanical processes - even in automation. As the wire gauge becomes lighter, however, alternative stripping solutions need to be utilized. Insulated Wire Wire is, most typically, a round strand of metal used to carry electrical currents in applications across multiple industries. It is less common to find “flat” or shaped wires. These individual strands are often placed together to make a multi-element cable. Most wires are insulated in order to: • Help prevent short circuits • Protect conductors from water and corrosion PEBAX®1 on stainless steel tube • Provide a smooth, slippery surface for comfort (medical applications) • Reduce power leakage, increasing electrical efficiency Solution: Wires need to be stripped of their insulation quickly and cleanly, without damage to the conductor. Lasers have proven to be a successful technology to selectively remove the coating in the desired locations. The type of laser that is optimal for a specific part is dependent on the coating material, conductor material, and wire gauge. Lasers are ideal for integration into automated assembly lines, and they can be programmed to remove insulation at any location on the part without causing damage to the conductor. It is also possible to process multiple wires at one time. The type of insulation used is largely determined by the purpose of the wire. Will it be exposed to high heat or intense cold? Will it be implanted in a human body? Is weight an issue? Common insulators include PVC and various enamels like THEIC, PAI, PVF, PDA, KAPTON®2, ETFE, PFA and FEP. Conventional Wire Stripping While insulation is beneficial for the reasons described above, it can limit current carrying capacity and affect downstream manufacturing processes like welding, soldering, or brazing. Manufacturers need to strip the insulation from the wire in order to provide electrical contact points. The trick is to remove the insulation cleanly and PEBAX is the trademark of Arkema France Corporation 2KAPTON is the trademark of Dupont Electronics
Open the catalog to page 1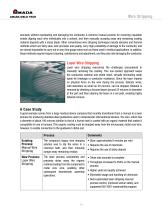
Wire Stripping precisely without overheating and damaging the conductor. A common manual process for removing insulation entails dipping each wire individually into a solvent, and then manually scraping away any remaining coating material deposits with a sharp blade. Other conventional wire stripping techniques include abrasive and thermal methods which are fairly slow, lack precision and quality, carry high probability of damage to the conductor, and are almost impossible to carry out on very fine gauge wires such as those used in medical applications. In addition, these methods require...
Open the catalog to page 2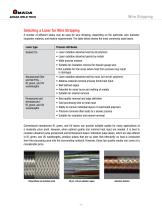
Wire Stripping Selecting a Laser for Wire Stripping A number of different lasers may be used for wire stripping, depending on the particular wire diameter, insulation material, and feature requirements. The table below shows the most commonly used lasers. Laser type Process attributes • Laser radiation absorbed well by all polymers • Laser radiation absorbed poorly by metals • Wide process window • Suitable for insulation removal for heavier gauge wire • Not suitable for fine wires where heat from process may result in damages Nanosecond fiber and Nd:YVO4 IR, green, and UV wavelengths •...
Open the catalog to page 3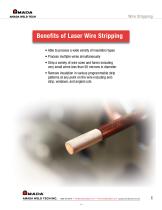
Wire Stripping Benefits of Laser Wire Stripping • Able to process a wide variety of insulation types • Process multiple wires simultaneously • Strip a variety of wire sizes and forms including very small wires less than 50 microns in diameter Copyright© 2022 AMADA WELD TECH INC. • Remove insulation in various programmable strip patterns at any point on the wire including endstrip, windows, and a
Open the catalog to page 4All AMADA WELD TECH Inc. catalogs and technical brochures
-
TC-W100A
2 Pages
-
MEA-100B
2 Pages
-
MIB-300A/600A
2 Pages
-
CD-A125A CD-A300A CD-A1000A
2 Pages
-
Rotary Dial Index Systems
2 Pages
-
AMADA WELD TECH
24 Pages
-
HF-2700A / HF-2500A
4 Pages
-
CD-V Series
2 Pages
-
MD-A10000A/ MD-B5000A
2 Pages
-
ISQ Series
3 Pages
-
IPB-5000A-MU
2 Pages
-
MFP60 for aws3
2 Pages
-
MFP25 FRO AWS3
2 Pages
-
Series 320
2 Pages
-
newhorizon
3 Pages
-
F120, F160, FD120
4 Pages
-
KN-II Series
2 Pages
-
MH Weld Head Range
4 Pages
-
Accessries
9 Pages
-
Laser Microfabrication
2 Pages
-
ML-5120A
2 Pages
-
Systems
16 Pages
-
ML-5120
2 Pages
-
DC29-UB29-UB29A
4 Pages
-
LF Series Lasers
2 Pages
-
SA2200 Dual Oven
2 Pages
-
Laser Tube Cutting Systems
2 Pages
-
Heat Staking
2 Pages
-
Seam Laser Welder - 150W
2 Pages
-
Systems Datasheet
16 Pages
-
AX5000 Glovebox
2 Pages
-
MX2000 Glovebox
2 Pages
-
Benchmark AF8500 / AF 1250
2 Pages
-
Pulsed-Heat Hot-Bar
10 Pages
-
Benchmark SM8500
2 Pages
-
vacuum bakeout oven
2 Pages
-
Interposer Module
2 Pages
-
UV Laser Marking Systems
2 Pages
-
CO2 Laser Marking Systems
2 Pages
-
Fiber Laser Micro Welders
2 Pages
-
Sigma Laser Tube Cutter
2 Pages
-
Laser Marker Motion
2 Pages
-
Laser Welding Gloveboxes
2 Pages
-
Thermocouple Welder - TCW
2 Pages
-
Laser Accessories
7 Pages
-
Alpha Series
2 Pages
-
MX-2000 Glovebox Technical
2 Pages
-
AX-5000 Glovebox
2 Pages
-
Benchmark Accessories
9 Pages
-
Thin Line Weld Heads
8 Pages
-
Uniflow 4
2 Pages
-
Pulsar
2 Pages
-
LMC1 Laser Marker Motion
2 Pages
-
LW300-600A
2 Pages
-
LW50A-70-150A
2 Pages
-
LW5-15-25A
2 Pages
-
LF Series
2 Pages
-
50 Series Weld Heads
4 Pages
-
MH Series Weld Heads
4 Pages
-
MG3
12 Pages
-
MG3 Hot Bar Monitoring
3 Pages
-
Sarcon and Kapton Modules
2 Pages
-
Thin-line
8 Pages
-
IS series
2 Pages
-
ISB-300 A
2 Pages
-
Accessoires
9 Pages
-
DC25, UB25
4 Pages
-
Fine Laser Cutting Datasheet
4 Pages
-
laser markers and marker systems
16 Pages
-
Bonding Heads
2 Pages
-
MG3 UNIQUE PROCESS MONITORING
12 Pages
-
Process Calibration Tools
2 Pages
-
LaserCuttingSystems_Cut
4 Pages
-
Pincer Weld Head - MFP-Z
3 Pages