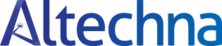
Catalog excerpts
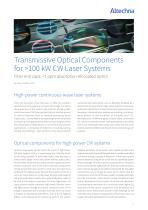
Transmissive Optical Components for >100 kW CW Laser Systems Fiber end caps, <1 ppm absorption AR coated optics By Marius Gželka, 2019 High-power continuous-wave laser systems Since the invention of the first laser in 1960, the constant development and expansion of laser technology has led to the production of the modern-day versions of high-power continuous-wave (CW) laser systems that are now being used in various industries (such as material processing, heavy industry, etc.). As they help to increase the growth of companies and open up new opportunities, they are becoming one of the key components of these sectors. In one of the most common applications - processing of materials (including cutting, drilling and welding) - laser systems bring many benefits compared with alternatives, such as flexibility (enabled by a wide choice of parameters), high speed, precision processes, automation feasibility and low maintenance requirements [1]. Nowadays, industrial laser systems are reaching continuouswave powers at the hundreds of kilowatts level [2]. Manufacturers of different types of lasers (fiber, solid-state, CO2, etc.) are involved in power-scaling competition, and while that is one of the goals that unites them, there are also some shared unwanted effects that they all face in developing such systems. Optical components for high-power CW systems Optical components are the most critical part of high-power CW laser systems which, in most cases, are a limiting factor for the output power. In solid state lasers, they are used in almost every stage (intra-cavity, beam delivery optics, etc.), while for fiber lasers they are mostly used for output and beam delivery purposes. One of the most important components of high-power fiber laser systems is end caps. End caps must withstand the highest power fluences (the purpose of the end cap is an initial reduction of the power density) while keeping the appropriate beam quality; thus, special attention needs to be paid to this optical component [3]. Since high-power CW laser systems enable extremely high power fluences, when the light passes through the optical component part of the energy is absorbed and converted into heat, which can have a number of detrimental side effects. One of these negative effects is the heating of the remaining parts of the system (holders, electronic schemes etc.) which poses a threat to the appropriate performance of the laser system. Another side effect is thermal lensing, it causes a distortion of the beam quality and the beam focusing, which could lead to a potential system failure (damage of further optical components) or introduce inaccuracies into the application [4]. The worst case scenario is laser-induced damage to the optical component [5]. Damaged components can no longer be used, which means that the maintenance and cost of the laser system increases with each low LIDT component. It also results in major disruptions to the further development of the system. Since thermal absorption is the dominant mechanism in a continuous-wave regime [5], absorption of the optical component must be reduced to a minimum level. These issues present a real challenge for the manufacturers of optical components, whose main task is to enable the further development of such laser systems.
Open the catalog to page 1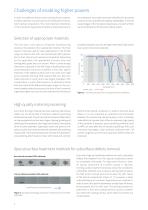
Challenges of enabling higher powers In order to enable the further power scaling of laser systems, constant attention must be paid to the development of topnotch optical components. The most important milestones in the manufacturing process of optical components have to be understood. Once they have been identified, the processes must be strictly controlled and display repeatability. There are several stages of the manufacturing process, and each of them can be limiting factor for the entire optical system. Selection of appropriate materials possible absorption sources, the right materials...
Open the catalog to page 2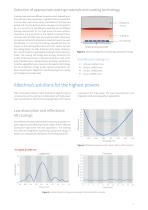
Selection of appropriate coating materials and coating technology Coating materials have different properties and, depending on the customer’s laser parameters, a perfect fit has to be selected. In some cases, even when all the parameters of the laser are locked and only the pulse duration changes (ns compared to fs), it is necessary to use different materials due to different damage mechanisms [5]. For high-power CW laser systems, absorption is the key factor of the optical component; thus, coating materials that have the lowest possible absorption and special methods for absorption...
Open the catalog to page 3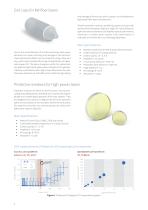
End caps for kW fiber lasers and damage of the end cap which causes a lot of problems for high-power fiber laser manufacturers. Altechna provides a solution by offering custom end caps with extremely low absorption (Figure 5), high LIDT values (Figure 6), tight mechanical tolerances and flawless optical performance, resulting in a perfect beam quality. Every specification is evaluated and confirmed in our metrology laboratory. Due to the small diameter of the fiber extremely high power densities can cause scorching and damage of the end-face. These detrimental effects can be avoided by...
Open the catalog to page 4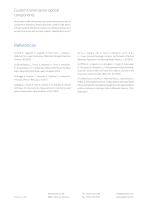
Custom transmissive optical components We are able to offer solutions for any custom transmissive optical components (windows, lenses, prisms, etc.) used for high-power CW laser systems. Feel free to contact our professional team and we will provide you with our best support: sales@altechna.com References [1] Hull R., Jagadish C., Osgood, Jr. R.M., Parisi J., Wang Z., Warlimont H. / Laser Processing of Materials, Springer, Materials Science 139 (2010) [5] Yu, J., Xiang, X., He, S., Yuan, X., Zheng, W., Lü, H., & Zu, X. / Laser-Induced Damage Initiation and Growth of Optical Materials,...
Open the catalog to page 5