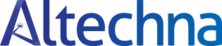
Catalog excerpts
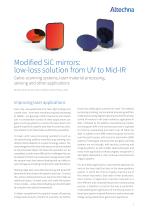
Modified SiC mirrors: low-loss solution from UV to Mid-IR Galvo-scanning systems, laser material processing, sensing and other applications By Deividas Buinovskis, Marius Gželka, Aivaras Pečiulis, 2022 Improving laser applications Every day, new applications for laser light emerge and current ones – from laser manufacturing and processing to LiDARs – are growing in both importance and market size. A considerable number of these applications use galvo scanning systems to control the laser beam and guide it to perform a specific task. Altechna now has a lowloss solution to do these tasks as efficiently as possible. To begin with, laser-processing operations (such as micromachining, additive manufacturing, marking, and others) heavily depend on a system’s energy output. The more energy from the initial laser beam can be transmitted to the processed object, the faster the operation can be completed, and the more difficult the challenges that can be tackled. Furthermore, lower beam energy losses inside the system mean less internal heating that can affect or even damage surrounding components inside the device. Heating might also cause thermal lensing and focal shift phenomena that worsen the system’s precision. To avoid this, active cooling solutions are required, which take up additional space, increase costs and make the system more complex – unless internal heating can be eliminated by using low-loss optical components. To better comprehend the potential impact of lowering energy losses by even a fraction of a percent, we need to know how widely galvo scanners are used. The material processing (marking, micromaterial processing and kW+ material processing) segment alone accounted for almost a third of revenue in the laser market by application in 2021. Followed by the additive manufacturing market, that has grown 30% in the last two years and is expected to continue accelerating and reach over $9 billion by 2024. In addition, the LiDAR market has grown five times over the past 10 years, with a burst in automotive LiDAR systems. If these giant industries that use galvo scanning systems are not enough, add security, scanning and imaging systems, as well as R&D, space telescopes and many more applications whose progress and growth is also highly dependent on the continuous improvement of galvo systems. For all of these applications, improvement depends not only on the laser itself, but also on the beam guidance system, in which the mirrors of galvo scanners are of the utmost importance. Each step of their production, from choices of application-oriented materials to a time-efficient and competitively priced manufacturing process, is therefore crucial on the way to perfection. Understanding the significance of minimizing losses in these laser systems inspired Altechna to seek and provide energy-saving solutions for galvo scann
Open the catalog to page 1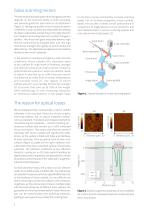
Galvo scanning mirrors The end result of any laser system that uses galvo scanners depends on the scanner’s ability to both accurately and precisely guide the laser beam to its destination (Figure 1). Having top-quality mirrors inside the system is therefore crucial, as these are responsible for keeping the beam undistorted and pointing in the right direction 24/7 despite surrounding heat and constant changes in position. They must have good and stable flatness, high thermal conductivity to dissipate heat, and very high mechanical strength and rigidity to avoid mechanical deformations. The...
Open the catalog to page 2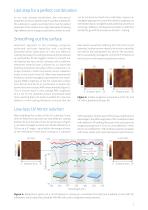
Last step for a perfect combination As we have already established, the mechanical properties of silicon carbide make it a perfect material for the substrate in a galvo scanning mirror, but the optical properties of the surface are a major downside. Achieving high reflectance for energy conservation, similar to what can be achieved on fused silica substrates, requires an intelligent approach to control the surface’s roughness. As mentioned above, straightforward polishing would be a very long, inefficient, and expensive process, so Altechna decided to go with the process we do best –...
Open the catalog to page 3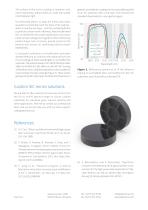
As mentioned before, to keep the initial laser beam wavefront undistorted, both the base of the coating – which is now the sub-layer – and the coating itself have to provide a certain level of flatness. Altechna delivered this, as needed for the custom applications not only to preserve beam energy, but to guide it while maintaining perfect shape. And, of course, precise control of the process was proven by confirming batch-to-batch repeatability. A successful verification of modification principles allowed Altechna to continue with advanced low loss mirror coatings at other wavelengths on a...
Open the catalog to page 4